CA Project Pics
Printed From: Unofficial Allis
Category: Allis Chalmers
Forum Name: Farm Equipment
Forum Description: everything about Allis-Chalmers farm equipment
URL: https://www.allischalmers.com/forum/forum_posts.asp?TID=194109
Printed Date: 28 Jul 2025 at 6:47am Software Version: Web Wiz Forums 11.10 - http://www.webwizforums.com
Topic: CA Project Pics
Posted By: dfwallis
Subject: CA Project Pics
Date Posted: 16 Mar 2023 at 9:08pm
I'm sure nobody really cares, but here's a couple of starting pics...small tree and grapevine encrusted.
|
Replies:
Posted By: dfwallis
Date Posted: 16 Mar 2023 at 9:09pm
Sorry about the formatting :( ...there, found the edit option, fixed.
|
Posted By: steve(ill)
Date Posted: 16 Mar 2023 at 9:22pm
looks like it has been there a while !
------------- Like them all, but love the "B"s.
|
Posted By: plummerscarin
Date Posted: 16 Mar 2023 at 9:26pm
The B I drug home started like that. Looking forward to watching your progress
|
Posted By: dfwallis
Date Posted: 16 Mar 2023 at 9:30pm
steve(ill) wrote:
looks like it has been there a while ! |
Yes, not really sure how long. But it WILL LIVE AGAIN IF I HAVE TO WITHDRAW EVERY LAST PENNY FROM MY 401K! (but hopefully not :), although today's spending was a good start on that).
|
Posted By: KMAG
Date Posted: 16 Mar 2023 at 9:50pm
We should do as found and fixed up post for inspiration.
|
Posted By: tractorboy
Date Posted: 17 Mar 2023 at 1:13am
Wow ,nice pictures! Safe to say she's been sitting a while! Keep us posted. keith so.va.
|
Posted By: rilenz
Date Posted: 17 Mar 2023 at 7:14am
am I looking at that right looks like it has a three point on the rear you sure that is'nt a ca
|
Posted By: steve(ill)
Date Posted: 17 Mar 2023 at 8:14am
it WILL LIVE AGAIN IF I HAVE TO WITHDRAW EVERY LAST PENNY
Joint the CLUB... to be a MEMBER, you have to spend TWICE a much on the tractor as it will be worth in the end !! ............. Its not about the money !
------------- Like them all, but love the "B"s.
|
Posted By: dfwallis
Date Posted: 17 Mar 2023 at 9:10am
rilenz wrote:
am I looking at that right looks like it has a three point on the rear you sure that is'nt a ca |
It is a 1952 CA. Positive. It has no 3-point hitch, just the normal 1952 pin hitch. In the picture, the drawbar is installed. The lift arms are fully down and the drawbar attaches to the lift arms and fits inside the U shaped arms. I was looking for a ready made 3-point kit for it but didn't find any. I see a kit that mounts on a drawbar, although not the pin hitch drawbar. I was thinking I could adapt the pin hitch drawbar to attach via split bearings to the rockshaft and thus my other post asking about the dimensions of the rockshaft.
|
Posted By: dfwallis
Date Posted: 17 Mar 2023 at 9:12am
steve(ill) wrote:
it WILL LIVE AGAIN IF I HAVE TO WITHDRAW EVERY LAST PENNY
Joint the CLUB... to be a MEMBER, you have to spend TWICE a much on the tractor as it will be worth in the end !! ............. Its not about the money ! | I'm already well above that amount :(
|
Posted By: Trinity45
Date Posted: 17 Mar 2023 at 9:20am
rilenz wrote:
am I looking at that right looks like it has a three point on the rear you sure that is'nt a ca |
Older CA, the lift arms run down like that, but you can put a 3ph on one, I have two CA's and I put a 3ph on one to use a finish mower on.
|
Posted By: steve(ill)
Date Posted: 17 Mar 2023 at 9:26am
look at the photo in the second post below...
https://www.allischalmers.com/forum/ca-3-point-hitch_topic169749.html" rel="nofollow - https://www.allischalmers.com/forum/ca-3-point-hitch_topic169749.html
------------- Like them all, but love the "B"s.
|
Posted By: steve(ill)
Date Posted: 17 Mar 2023 at 9:29am
you cqn also rig up something like this
------------- Like them all, but love the "B"s.
|
Posted By: dfwallis
Date Posted: 17 Mar 2023 at 9:31am
steve(ill) wrote:
look at the photo in the second post below...
https://www.allischalmers.com/forum/ca-3-point-hitch_topic169749.html" rel="nofollow - https://www.allischalmers.com/forum/ca-3-point-hitch_topic169749.html
|
That's the snap coupler draw bar. The pin hitch drawbar attaches to the lift arms, so I either have to first convert to snap coupler or I have to figure out a way to detach the pin hitch drawbar from the lift arms and attach to the rockshaft via split bearings or other custom mount.
|
Posted By: steve(ill)
Date Posted: 17 Mar 2023 at 9:32am
if you want to "make your own"..... the bar under the rear axle looks like a standard drawbar you can buy at TSC... and the two lower arms are just aftermarket arms, also available at TSC ........ then just add a couple stabalizers.
------------- Like them all, but love the "B"s.
|
Posted By: dfwallis
Date Posted: 17 Mar 2023 at 9:34am
Trinity45 wrote:
rilenz wrote:
am I looking at that right looks like it has a three point on the rear you sure that is'nt a ca |
Older CA, the lift arms run down like that, but you can put a 3ph on one, I have two CA's and I put a 3ph on one to use a finish mower on. |
I searched Steiner and several other places and they all said there was nothing specific to the CA (and probably more so the pre 1954 CA). If you know otherwise, I'd like to know where to get it or what mods are needed. I think I have a suitable mod in mind, if there is enough clearance behind the rockshaft.
|
Posted By: steve(ill)
Date Posted: 17 Mar 2023 at 9:40am
Gary... you got to look at what you have and what you want... Presently your upper arms are DOWN and the drawbar is connected between them..... for a 3 point, you need to anchor "something" under the axle to pin the lower arms to it.... The "anchor" is normally the bail area, or modified pin in that area..... You can also buy 3 points that attach to a crossbar between the final drive cases... like a C or B maybe ?
------------- Like them all, but love the "B"s.
|
Posted By: dfwallis
Date Posted: 17 Mar 2023 at 9:41am
steve(ill) wrote:
Gary... you got to look at what you have and what you want... Presently your upper arms are DOWN and the drawbar is connected between them..... for a 3 point, you need to anchor "something" under the axle to pin the lower arms to it.... The "anchor" is normally the bail area, or modified pin in that area..... You can also buy 3 points that attach to a crossbar between the final drive cases... like a C or B maybe ? |
yes
|
Posted By: steve(ill)
Date Posted: 17 Mar 2023 at 9:44am
couple more photos..... several ways to get there from here... just need to decide..some designs are STRONGER than other.. some are for a bushog and others stiff enough to pull a 10 ft disc..
https://www.allischalmers.com/forum/2point-to-3point-hitch-ca-conversion-question_topic51797.html" rel="nofollow - https://www.allischalmers.com/forum/2point-to-3point-hitch-ca-conversion-question_topic51797.html
------------- Like them all, but love the "B"s.
|
Posted By: dfwallis
Date Posted: 18 Mar 2023 at 9:03am
Borescope pics, some ok, some not so ok. Not the best image resolution.
|
Posted By: dfwallis
Date Posted: 18 Mar 2023 at 9:04am
Looks like he sent some duplicates or near duplicates.
|
Posted By: steve(ill)
Date Posted: 18 Mar 2023 at 9:37am
does the engine bar over ? what was in the oil pan ? are you going to rebuild , pull head and clean, or just fill jugs and let them soak to loosen things up ?
------------- Like them all, but love the "B"s.
|
Posted By: dfwallis
Date Posted: 18 Mar 2023 at 9:50am
steve(ill) wrote:
does the engine bar over ? what was in the oil pan ? are you going to rebuild , pull head and clean, or just fill jugs and let them soak to loosen things up ? |
Engine is locked. Brother has not decided yet. He was the last one to put new sleeves in it, so he's familiar with its issues. He's researching and thinking it over. He originally thought he would soak it for awhile, may still do that.
|
Posted By: TomC
Date Posted: 18 Mar 2023 at 2:33pm
I have a 52 CA it has a Cross Manufacturing 3 point on it, it hooks right to the snap coupler on the tractor, the top link hook up is two metal pieces welded to the rock shaft.Cross is out of Mindenmine Missouri,not sure I spelled that town right,
|
Posted By: dfwallis
Date Posted: 18 Mar 2023 at 4:25pm
TomC wrote:
I have a 52 CA it has a Cross Manufacturing 3 point on it, it hooks right to the snap coupler on the tractor, the top link hook up is two metal pieces welded to the rock shaft.Cross is out of Mindenmine Missouri,not sure I spelled that town right, |
Yes, but the 1952 did not come with a snap coupler. After 1954 it was available as an add-on. Since we have no snap coupler implements, only those that came with the original pin hitch and lift mechanism, I wasn't planning on converting to snap coupler at this time. I was wanting to make do with the original drawbar, but because the cross member goes all the way across between the lift arms, the 3 point lift arms would probably hit it on the lower end unless I mount the front pivot up quite high (to get the 3 point down to the recommended 7-8 inches from the ground).
|
Posted By: dfwallis
Date Posted: 18 Mar 2023 at 8:11pm
dfwallis wrote:
TomC wrote:
I have a 52 CA it has a Cross Manufacturing 3 point on it, it hooks right to the snap coupler on the tractor, the top link hook up is two metal pieces welded to the rock shaft.Cross is out of Mindenmine Missouri,not sure I spelled that town right, |
Yes, but the 1952 did not come with a snap coupler. After 1954 it was available as an add-on. Since we have no snap coupler implements, only those that came with the original pin hitch and lift mechanism, I wasn't planning on converting to snap coupler at this time. I was wanting to make do with the original drawbar, but because the cross member goes all the way across between the lift arms, the 3 point lift arms would probably hit it on the lower end unless I mount the front pivot up quite high (to get the 3 point down to the recommended 7-8 inches from the ground). |
Sorry, I've looked at that one many times but missed the tiny inset image showing a second version with the snap coupler loop having a tiny pin receiver welded on top. The images on the OKT site are mostly too small for me to read without a magnifying glass. But I also may have not looked too hard because it says "light duty" and does not look to me to be well designed/made. "light duty" would mean category 0 to me. It's hard for me to tell without dimensions, but it appears to have very narrow spacing of the cat 0 version. It does say cat 1 on the OKT site. Another thing is the arms appear to be fixed width. They're supposed to swing a little (maybe one swings and one doesnt). I'm no expert in 3 point design, but at this point, I'm not liking that one. Maybe I could be talked into it.
|
Posted By: TomC
Date Posted: 18 Mar 2023 at 9:04pm
I think what your looking at and what I have are two entirely different 3 point hitches,both my lower arms swing and are adjustable,it works fine with all the 3 point implements I have here and is very stoutly built.Good luck with it.
|
Posted By: steve(ill)
Date Posted: 18 Mar 2023 at 9:26pm
there are basically two different types of AFTERMARKET 3 points you can buy... This one you must remove your drawbar from the snap coupler ( or pin hitch)... and install this in its place ... The two arms are adjustable on width and one is pinned and swings outward. .......... this is made for the snap coupler, but could be MODIFIED to the pin hitch.
the second design is one that you bolt a cross bar to your drawbar, under the axle.. then mount the two lower 3 point arms to it.... There are other ways to do a 3 point, but the only AFTERMARKET are one of these two designs... You can do it different, but it will be "home made".
------------- Like them all, but love the "B"s.
|
Posted By: dfwallis
Date Posted: 18 Mar 2023 at 9:27pm
TomC wrote:
I think what your looking at and what I have are two entirely different 3 point hitches,both my lower arms swing and are adjustable,it works fine with all the 3 point implements I have here and is very stoutly built.Good luck with it. |
Well, darn, this is the only Cross I've seen that has a CA non-snap-coupler option: https://oktractor.com/zen/index.php?main_page=product_info&cPath=1_13_195&products_id=204&zenid=r6hptdv2h5ihrrccehhp5nluv3" rel="nofollow - https://oktractor.com/zen/index.php?main_page=product_info&cPath=1_13_195&products_id=204&zenid=r6hptdv2h5ihrrccehhp5nluv3
I went to the Cross website itself and found no hitches at all.
|
Posted By: dfwallis
Date Posted: 18 Mar 2023 at 9:29pm
steve(ill) wrote:
there are basically two different types of AFTERMARKET 3 points you can buy... This one you must remove your drawbar from the snap coupler ( or pin hitch)... and install this in its place ... The two arms are adjustable on width and one is pinned and swings outward. .......... this is made for the snap coupler, but could be MODIFIED to the pin hitch.
|
OK Tractor has this one with an option premade for non-snap-coupler (that I missed before). Like I said, didn't like the design of it, but when time comes I might choose the easy out.
|
Posted By: steve(ill)
Date Posted: 18 Mar 2023 at 9:35pm
that one eliminates the drawbar... if 90% of your work is with the 3 point, then you can buy an adaptor that gives you the ability to use a drawbar , ball hitch, etc.
------------- Like them all, but love the "B"s.
|
Posted By: dfwallis
Date Posted: 19 Mar 2023 at 10:48am
dfwallis wrote:
steve(ill) wrote:
there are basically two different types of AFTERMARKET 3 points you can buy... This one you must remove your drawbar from the snap coupler ( or pin hitch)... and install this in its place ... The two arms are adjustable on width and one is pinned and swings outward. .......... this is made for the snap coupler, but could be MODIFIED to the pin hitch.
|
OK Tractor has this one with an option premade for non-snap-coupler (that I missed before). Like I said, didn't like the design of it, but when time comes I might choose the easy out. |
I'll add that OK Tractor seems to have this one for about half the price of Steiner...
|
Posted By: JimD
Date Posted: 21 Mar 2023 at 11:58pm
Yes, we are significantly less than steiner on most parts. I was just at the factory a week ago. Ill be happy to answer any additional questions.
------------- Owner of http://www.OKtractor.com" rel="nofollow - OKtractor.com PM for an instant response on parts. Open M-F 9-6 Central.
We have new and used parts. 877-378-6543
|
Posted By: dfwallis
Date Posted: 22 Mar 2023 at 10:41am
JimD wrote:
Yes, we are significantly less than steiner on most parts. I was just at the factory a week ago. Ill be happy to answer any additional questions. |
One of dislikes about the design is that I would prefer that both arms pivot separately. In the snap coupler design, pivot of the fixed arm is relative to the moveable snap coupler tongue. In the non-snap coupler design, it has a pipe welded across the tongue. Unless there is a lot of slop in the size of the hole, there would not be proper pivoting of the "fixed" arm. And I don't think you want a lot of slop in the hole for the pin hitch.
|
Posted By: DrAllis
Date Posted: 22 Mar 2023 at 10:58am
Most of the time, each lift/draft arm ball would be at the same height. Moldboard plowing the right side is always an inch or more higher. That whole frame pivots in the snap-coupler bell when you want one lift/draft arm ball at a different height that the other lift/draft arm by changing the lift link length. I don't see a problem as long as it is a snap-coupler bell version.
|
Posted By: dfwallis
Date Posted: 22 Mar 2023 at 11:02am
DrAllis wrote:
Most of the time, each lift/draft arm ball would be at the same height. Moldboard plowing the right side is always an inch or more higher. That whole frame pivots in the snap-coupler bell when you want one lift/draft arm ball at a different height that the other lift/draft arm by changing the lift link length. I don't see a problem as long as it is a snap-coupler bell version.
|
Yes, but this would be the non-snap coupler version with a weld on mod which would prevent left to right swing as well as rotational swing.
|
Posted By: dfwallis
Date Posted: 22 Mar 2023 at 1:11pm
dfwallis wrote:
DrAllis wrote:
Most of the time, each lift/draft arm ball would be at the same height. Moldboard plowing the right side is always an inch or more higher. That whole frame pivots in the snap-coupler bell when you want one lift/draft arm ball at a different height that the other lift/draft arm by changing the lift link length. I don't see a problem as long as it is a snap-coupler bell version.
|
Yes, but this would be the non-snap coupler version with a weld on mod which would prevent left to right swing as well as rotational swing.
|
I'm up against my spending limit for this year, but when I do this, provided I can devise a suitable drawbar mount modification (keeping the existing 1952 drawbar as is if possible), I'm leaning towards a drawbar mount version for the WD45, perhaps without the sway block (my drawbar mod might suffice for sway block). I tried sourcing the individual parts (arms, drawbar mount), but that cost was way higher than getting the equivalent kit and throwing away unneeded parts :(
|
Posted By: steve(ill)
Date Posted: 22 Mar 2023 at 1:13pm
I see your point Gary... A Pin thru a steel bushing would not appear to have much "movement".. unless your "PIN HOLE" brackets are egg shaped for L-R swing.... Maybe Jim can explain more as he sells them.. Personally i would be temped to use the snap coupler version and make a "trailer hitch" type fitting on my crossbar under the tractor, then PIN thru the coupler loop.. That would give you movement L-R and Up- Down... but would take a little modification to your present hitch bar.
possible hitch design for snap coupler loop.
------------- Like them all, but love the "B"s.
|
Posted By: dfwallis
Date Posted: 22 Mar 2023 at 1:25pm
steve(ill) wrote:
I see your point Gary... A Pin thru a steel bushing would not appear to have much "movement".. unless your "PIN HOLE" brackets are egg shaped for L-R swing.... Maybe Jim can explain more as he sells them.. Personally i would be temped to use the snap coupler version and make a "trailer hitch" type fitting on my crossbar under the tractor, then PIN thru the coupler loop.. That would give you movement L-R and Up- Down... but would take a little modification to your present hitch bar.
|
Yes. A slightly better design might be an add-on bracket that sandwiches the snap coupler tongue (top bracket and bottom bracket, with perhaps loose fitting bolts, one right in the inside circular bend of the tongue, one at the rear. Then the pin sleeve would be welded onto either bracket. That would preserve the integrity of the tongue as well. Being loose fitting, it could give you enough range of motion at least side to side.
|
Posted By: steve(ill)
Date Posted: 22 Mar 2023 at 1:29pm
yea... a added a drawing above that might be even easier.. use the BAR on the tractor to help limit movement fore- aft.
------------- Like them all, but love the "B"s.
|
Posted By: dfwallis
Date Posted: 26 Mar 2023 at 8:27pm
De-brushed...baby steps. Several days soaking in atf, still locked tite.
|
Posted By: steve(ill)
Date Posted: 26 Mar 2023 at 9:04pm
i dont know how your trying to ROTATE the motor ( bar/ crank).... but one good method is to jack on of the rear tires 2 inches off the ground and block under the drawbar or axle housing... put the transmission in gear, then try to ROCK the tire back and forth every couple days ( with the cylinders filled full of penetrant).
make sure when in Neutral that the tire will move.. That tells you the transmission is not locked up also..
------------- Like them all, but love the "B"s.
|
Posted By: dfwallis
Date Posted: 05 Apr 2023 at 5:51pm
Baby steps...new 13.6 tires on 12 inch rims :)Probably not much more activity before May.
|
Posted By: dfwallis
Date Posted: 28 May 2023 at 6:55pm
Some selected progress pics. New front and rear tires. New 12 inch rims on back with 13.6 Titans. New tires on front. Rims and front pedestal were sand blasted as was rear hubs and final drive near the wheels. One front rim was welded by dad in the mid 1960s. It's amazing that there's been almost no major deterioration since then. Only a few tiny pin holes near the original welds. The rear hubs and locks cleaned up very nicely. Only one of the lock bearing surfaces was slightly pock marked. All were very usable. All reassembled with anti-seize lube. The locks locked up tight. I was amazed how smoothly they operated. I stumbled upon the lock/lug wrench in the garage, and also the associated 5/8 inch lever bar. I painted them orange so I can remember them :) Everything was sand blasted primed and painted. Some key areas like inside the front rims have approximately 10 coats rust reformer and of paint in total. The inside of the front rims were a bit flakey (rust) but with angle grinder, wire brush, and sand blaster, they came out decent and smooth. Tire guy had no qualms with them. I may eventually replace the front rims, or maybe just the welded one which doesn't look as nice. The tractor has been moved to a garage for engine assessment. It will get rebuilt regardless, but there may need to be a section of the block re-welded. Dad welded it in the early 70's (or thereabouts) but did not have the right welding equipment on-site at the time so it continued to have a slow coolant leak. Believe the weld is intact though.
The starter motor was removed for unknown reason, but I tested it and it is fine with not a single issue with the gear teeth or throwout. Was inside the garage for 40 years. The original generator is another story. Was in pieces with coils toasted and loose. Believe I can get it rewound locally. I inspected part of the flywheel which seems fine where I could view. I think the transmission is ok but could only get it into reverse for the trailer ride. One brake seems functional, sort of, the other seems to be rubbing full time but not forcefully and the pedal won't depress beyond an inch or so. I can see a broken spring which may be wedged in the way. Steering play seems no worse than I remember it. I remember that the front rim welds were heavy enough to cause a little wobble at full speed. I found the ammeter and control panel. The control panel cleaned up nicely, but all switches and ammeter were toast so I'll be rebuilding that, cleaning up the starter (maybe more if needed), and the generator if I can. I'll probably use stainless fasteners in key exposed places. Nearly all electrical wiring seems haphazard. It seems to have had a regulator installed at some point, but no reference in my service manual so I'll have to research that further.
|
Posted By: dfwallis
Date Posted: 28 May 2023 at 6:58pm
I should have repacked the front bearings. One was fine but the other had slight end play. They both rotate smoothly. Was running out of time this trip. Needed to get some other things in besides the tractor. I painted the backside of the fenders to retard rust, but they'll need some straightening work at some point. They seem salvageable with only straightening required as far as I've seen so far.
|
Posted By: wjohn
Date Posted: 28 May 2023 at 11:03pm
Looks like good progress. Are the cultivators still hanging around somewhere?
------------- 1939 B, 1940 B, 1941 WC, 1951 WD, 1952 CA, 1956 WD-45
|
Posted By: IBWD MIke
Date Posted: 29 May 2023 at 6:28am
Looks good! I need to get to work on both of my CA's.
|
Posted By: steve(ill)
Date Posted: 29 May 2023 at 8:59am
the original battery was 6 volt and just had a CUT OUT SWITCH box mounted to the generator.. No voltage regulator.. The LIGHT SWITCH had a resistor on it that grounded the "F" wire from the generator to give a low amp charge.. When the switch was ON, the "F" was grounded around the resistor to get a GOOD GROUND and MORE AMP charge..
It was not uncommon to remove the light switch and put a 6 volt regulator near the generator and let it do the job.... If the battery was changed to 12v, then yes, you need a regulator to handle the job.
------------- Like them all, but love the "B"s.
|
Posted By: dfwallis
Date Posted: 29 May 2023 at 9:48am
wjohn wrote:
Looks like good progress. Are the cultivators still hanging around somewhere? |
I found front and rear cultivators, disc, plow, and planter. The cultivators are in the worst shape probably. Lots of trees growing through it. One of the sweeps is exactly in the middle of a 1.5 foot diameter scotch pine tree at ground level. It seems to be sideways. Couldnt see enough to see if its twisted or just on its side. It didn't quite logically compute.
|
Posted By: dfwallis
Date Posted: 29 May 2023 at 9:53am
steve(ill) wrote:
the original battery was 6 volt and just had a CUT OUT SWITCH box mounted to the generator.. No voltage regulator.. The LIGHT SWITCH had a resistor on it that grounded the "F" wire from the generator to give a low amp charge.. When the switch was ON, the "F" was grounded around the resistor to get a GOOD GROUND and MORE AMP charge..
It was not uncommon to remove the light switch and put a 6 volt regulator near the generator and let it do the job.... If the battery was changed to 12v, then yes, you need a regulator to handle the job.
|
It's 6 volt. Plan to keep it that way. The regulator was mounted just behind the starter motor. I don't remember it at all, so maybe my uncle added it in the 70s.
|
Posted By: dfwallis
Date Posted: 19 Jun 2023 at 8:41pm
Got a fairly good look at the engine block. The block was welded in several spots 50 years ago. Looks pristine, welds held, finished flat, good head gasket seals. I think it's going to be ok.
|
Posted By: Steve in NJ
Date Posted: 20 Jun 2023 at 5:34pm
if you need a new wiring system for that project, visit our website. We do everything electrical and touch on each area of the Tractor. I do Carb, Generator, Alternator, 3 position switch and Starter rebuilding. Be happy to help you out with anything....
Steve@B&B bb-customcircuits.com
------------- 39'RC, 43'WC, 48'B, 49'G, 50'WF, 65 Big 10, 67'B-110, 75'716H, 2-620's, & a Motorhead wife
|
Posted By: dfwallis
Date Posted: 20 Jun 2023 at 7:15pm
Steve in NJ wrote:
if you need a new wiring system for that project, visit our website. We do everything electrical and touch on each area of the Tractor. I do Carb, Generator, Alternator, 3 position switch and Starter rebuilding. Be happy to help you out with anything....
Steve@B&B bb-customcircuits.com
|
Already bought one of your rebuilt switches. Generator was toast, being completely rebuilt and converted to regulator style operation. Starter was in very good condition, but I opted to have him recondition it as well. Fort Worth Starter and Generator. I'll be doing the new wiring harness myself. Already have it.
|
Posted By: dfwallis
Date Posted: 24 Sep 2023 at 7:24pm
Progress pics 9/24/2023:
While engine block was out to the machine shop, I prepared the front half. Sheet metal was taken to a body shop for some rip and dent repairs. Installed a new throwout bearing although the old one wasnt really very bad. Clutch plate was relatively new. Also ran a new wiring harness.

Since the engine work is taking a little longer, I stored the parts along the roofline by the H. I cleaned and painted EVERYTHING. New bolts and studs where needed.
Crankshaft had some minor pitting but overall wasnt that bad. Machined everywhere needed. Had too much end play when we got it back so we sent it back out for more work. Originally, the machine shop documented the wrong specs on the work tag so we ordered the wrong bearings and had to do that over as well. Those issues were the source of most of the delay in getting the engine going. I had high hopes, but it didn't happen. Work is ongoing as time permits. No the M doesn't run either :(

After I got most of the front half ready for the engine install (minus sheet metal), I replaced the brake pads. This is the "good" one. The left one was rusted in two at the hinge. Kind of a chore to get all the rat and mud dauber nests out through those cubby holes. Must have pulled 2 gallons of junk out of there. The drums should probably be worked on but I think they'll be fine besides wearing the pads out a little faster. There was plenty of metal left. Probably because it hasn't had properly adjusted brakes since the 60s (i.e. little contact).
I was able to get the plow up out of the dirt and on some temporary blocks (I ran out of time and just used whatever I could find). The frame looks like it will clean up ok. The plowshare/moldboards are broken. The pieces seem to be lying around in the garage, could probably be welded up (or replaced).
Here's the cultivator previously mentioned as having a tree growing around it. That will be fun to remove.
And the disk. Didn't get a picture of the planter (forgot when I decided to de-tree the bulldozer).
|
Posted By: IBWD MIke
Date Posted: 25 Sep 2023 at 5:28am
That paint is looking pretty spiffy!
|
Posted By: ACinSC
Date Posted: 25 Sep 2023 at 6:18am
Looking good! Thanks for sharing
|
Posted By: dfwallis
Date Posted: 25 Sep 2023 at 8:32am
IBWD MIke wrote:
That paint is looking pretty spiffy!
|
3 coats of primer and 3 coats of orange. 4 and more coats of primer or orange in strategic areas.
|
Posted By: dfwallis
Date Posted: 16 Oct 2023 at 11:28am
10/16/2023 Update: Further engine work. Engine rebuild internals complete. Everything to spec except liner protrusion. Two slightly exceed the 0.005 max with light torque, but improve when fully torqued. Basically, they don't sit perfectly flat with the block surface. Pretty sure it will be fine.
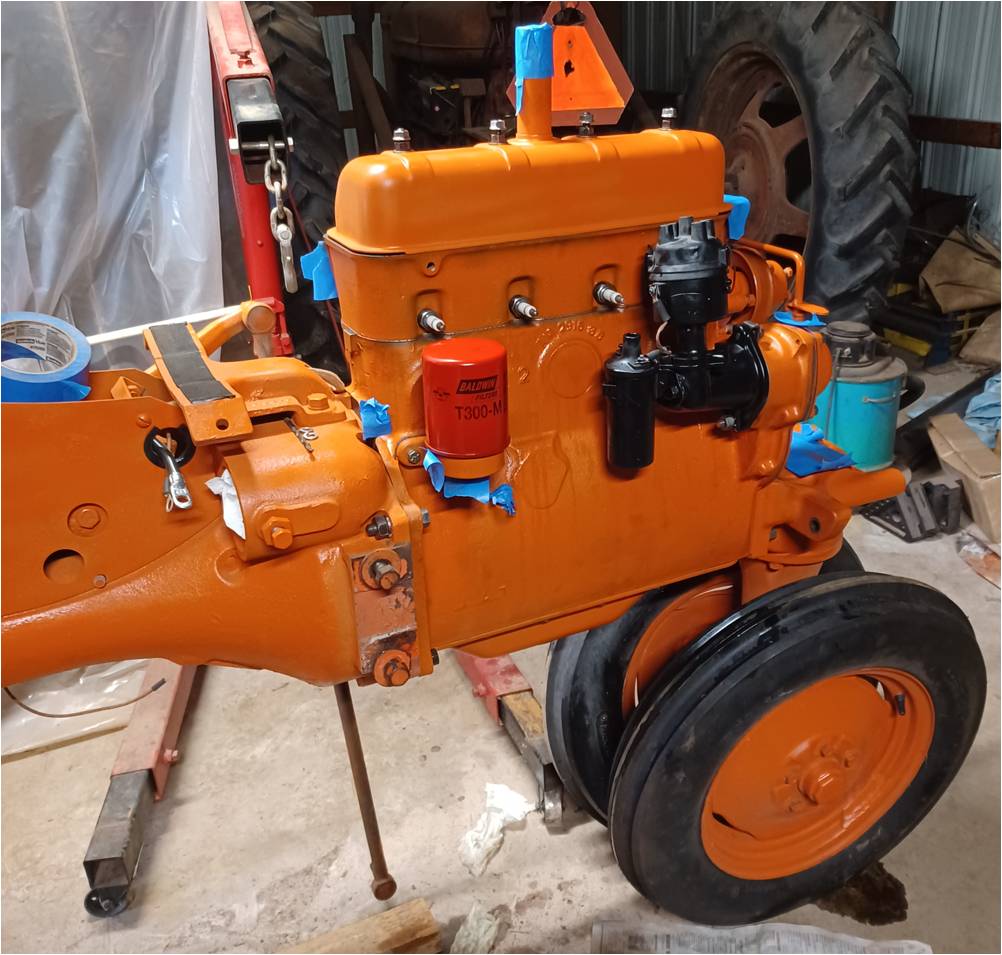
A better view of the improved rocker arm alignment. This is a massive improvement of horizontal alignment. Some were in contact with less than half of the valve stem previously. It's actually better than it looks in this pic due to parallax.
|
Posted By: JK in Pa
Date Posted: 16 Oct 2023 at 3:23pm
I believe I see valve rotators on the exhaust valves. I always thought valve rotators required offset rockers.
|
Posted By: dfwallis
Date Posted: 16 Oct 2023 at 6:45pm
JK in Pa wrote:
I believe I see valve rotators on the exhaust valves. I always thought valve rotators required offset rockers. |
Offsetting was sometimes used in small engines when no valve rotation device was present to achieve rotation. Offsetting is not supposed to be needed with a valve rotation device. It certainly should not be so far off that it's barely contacting the valve stem and leaving giant divots because of force being limited to a tiny contact area.
|
Posted By: 1955CA
Date Posted: 18 Oct 2023 at 10:45am
Any update pics DFWallis? That looks wicked with the big tires. I just went stock size on my rear replacements. Can't wait to see it all put back together after you had the body parts painted.
I just came in from my morning fall ride on mine. Took the dog for a walk, so figured I'd give Allis a run too. 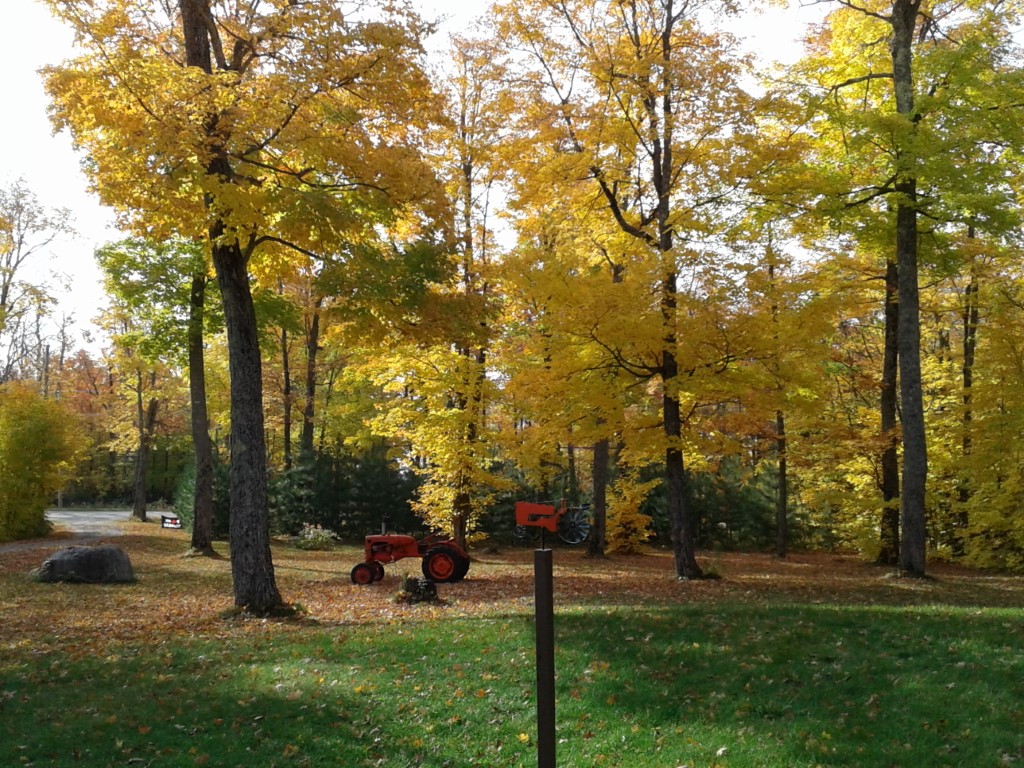
|
Posted By: dfwallis
Date Posted: 18 Oct 2023 at 5:56pm
1955CA wrote:
Any update pics DFWallis? That looks wicked with the big tires. I just went stock size on my rear replacements. Can't wait to see it all put back together after you had the body parts painted.
I just came in from my morning fall ride on mine. Took the dog for a walk, so figured I'd give Allis a run too. 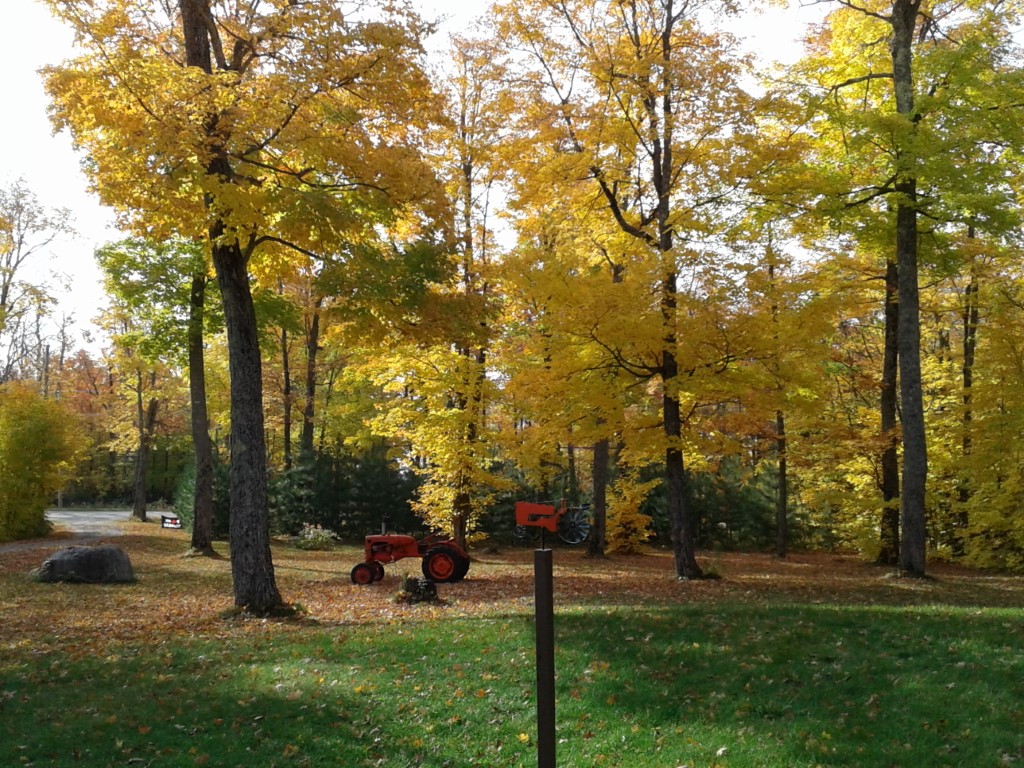 |
I just posted updates a few days ago. It's not back together yet but mostly finished the engine rebuild internals. I'm working on some hydraulic system mods at the moment. I'm creating a pedestal out of a trailer pintle hitch and a hitch extension to get me the required height above the tires. I've got the base complete except for painting. I'll start on the platform for mounting the spools tomorrow when a connector arrives and i can determine the width of the side by side spool sets/valves. I don't expect any significant progress before the spring. I hate working in the cold :(
|
Posted By: 1955CA
Date Posted: 18 Oct 2023 at 7:48pm
dfwallis wrote:
1955CA wrote:
Any update pics DFWallis? That looks wicked with the big tires. I just went stock size on my rear replacements. Can't wait to see it all put back together after you had the body parts painted.
I just came in from my morning fall ride on mine. Took the dog for a walk, so figured I'd give Allis a run too. 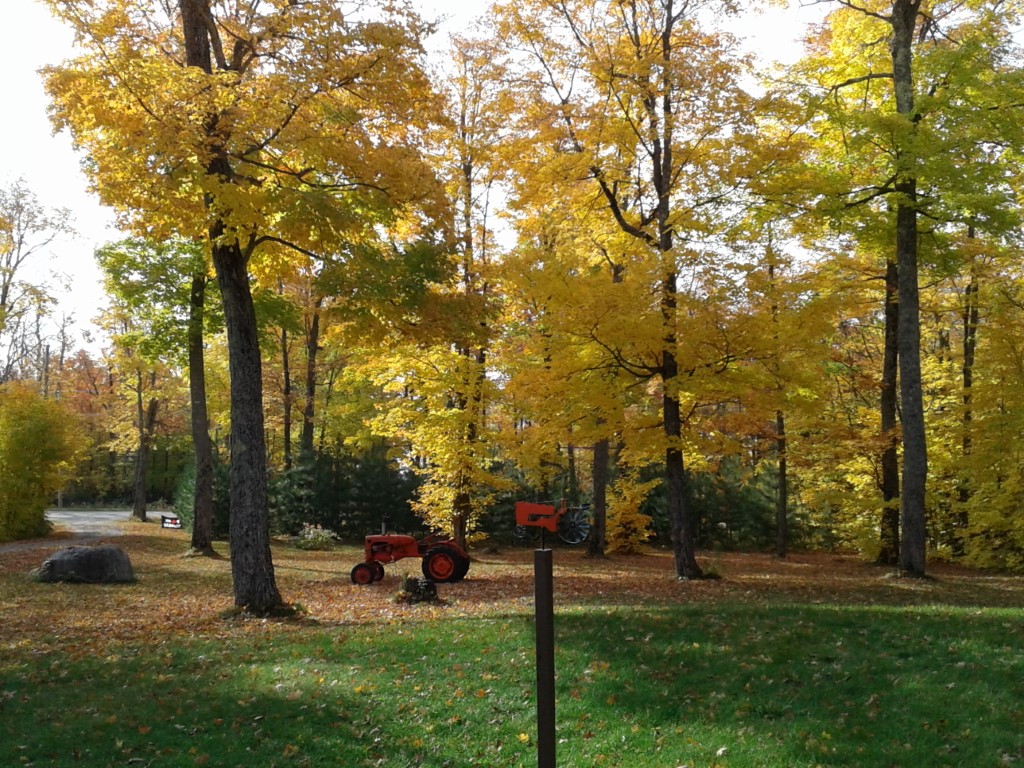 |
I just posted updates a few days ago. It's not back together yet but mostly finished the engine rebuild internals. I'm working on some hydraulic system mods at the moment. I'm creating a pedestal out of a trailer pintle hitch and a hitch extension to get me the required height above the tires. I've got the base complete except for painting. I'll start on the platform for mounting the spools tomorrow when a connector arrives and i can determine the width of the side by side spool sets/valves. I don't expect any significant progress before the spring. I hate working in the cold :( |
Awesome! I'll be watching for your future updates. You might teach me a few tricks to do to my CA.
|
Posted By: dfwallis
Date Posted: 30 Oct 2023 at 9:25pm
Progress 10/30/2023: Designing a removable hydraulic console intended to bolt to the left side fender. The console consists of a pintle hitch, and a hitch extender mounted vertically with a custom tray resting on top of the extension which is removable. Two single acting valves mount to the side, a 4 spool valve set on the top. It sticks out over the tractor tire for space reasons. It may or may not fit exactly where I designed it to sit (may be too close to the seat), but I can move it forward or backward if needed. The tray itself is designed to slide left or right. I still have some plumbing work to go for the return. Perhaps a little goofy, but fun anyway (I'm retired, I got time) :) It weighs a ton...
The back view showing the mechanism for sliding the tray left or right.
It includes optional hose supports that can be added or removed when the dual acting spool valves on top are used.
Closeup of a hose support. Since the dual acting valve hoses will come off straight up, this supports them at about 16 inches (can be lowered) to prevent sharp bends.
|
Posted By: steve(ill)
Date Posted: 31 Oct 2023 at 8:15am
so the vertical hitch is just a way to mount it to the tractor , so you can easily remove it when not needed ? .... Instead of bolts ? .... I see the threaded rod which allows you to adjust it in that direction.
------------- Like them all, but love the "B"s.
|
Posted By: dfwallis
Date Posted: 31 Oct 2023 at 11:31am
steve(ill) wrote:
so the vertical hitch is just a way to mount it to the tractor , so you can easily remove it when not needed ? .... Instead of bolts ? .... I see the threaded rod which allows you to adjust it in that direction. |
The bottom (pintle mount) section will be bolted to the fender wall. I haven't drilled those holes (in the pintle bracket) yet so I can determine the best position. I measured it and know very close where the holes will go but I made the bracket a little longer in case I need to adjust it right or left. The top section is the removable part via the hitch pin. I'm trying not to physically modify the tractor, just using existing bolt patterns as much as possible. The threaded rod is designed to allow the tray to slide left or right (it is then tightened in that left or right position). I was thinking ahead to deconflict it with my idea for a roll bar/canopy mount that mounts to the axle but will rise just outside the fender wall (so the wheels will have to be slightly spun out). When that roll bar/canopy is installed, the tray will have to be slid right/forward to deconflict (since it sticks out over the tire). The pintle hitch is mounted to a piece of 4 inch x 4 inch angle iron that I cut out the left and right floor sections. The right section had to be cut to deconflict with the brake lever. The left side was only cut for symmetry. The forward fender bolt is around 4 inches from hole to back of brake lever. The other fender bolt is 11 inches behind the forward fender bolt. I have about an inch of play to adjust the position to deconflict with the brake lever and the seat.
The console is fairly well balanced. There is little stress on the mount when you operate the spool levers which have quite strong springs. That was one worry with only having two mounting bolts. I can add a horizontal support later if needed.
|
Posted By: 1955CA
Date Posted: 01 Nov 2023 at 5:35am
Posted By: dfwallis
Date Posted: 25 Jan 2024 at 3:14pm
My first draft of the hydraulic return for a CA. I will first attempt return via filler cap as in below. If that doesn't work well, I have a better idea, but I think this will be ok if the flow is sufficient. Since the pump will be pulling out as fast as it's going back in, I don't anticipate problems, but I'll find out I guess. It's likely I'll have to reduce the size of the brass nut a little, but that's pretty easy. I may also need an o-ring. I had to bore the hole in the stainless fitting out to 3/8 inch (my poor drill bits). It was a 3/8 inch fitting with a 1/4" hole :( Was designed for super high pressure but not needed on the return line.
------------- 1952 CA13092
|
Posted By: dfwallis
Date Posted: 03 May 2024 at 12:12pm
Traveling this weekend to resume work. I probably won't post real time due to lack of cell service, but expect a few progress pics late May or early June :) In order, finish engine work (rebuilt last fall), front tin work (partly complete, blast and paint, hopefully the de-dented gas tank is ready from the body work guy, you'd think 8 months would be enough time), rewire (partly complete), first start, then move on to the rear half (shifter back), finish steering wheel resurface (mostly complete), hand clutch rebuild, weld up and seal final drive oil pans, sand blast and paint rear half, complete custom 3pt mods and custom hydraulic mods last (well some will have to be done before I reinstall the platform). At some point I need to rework the front wheel bearings, but that can wait.
------------- 1952 CA13092
|
Posted By: dfwallis
Date Posted: 26 May 2024 at 11:05am
Update 05/26/2024:
Quite a bit of trouble getting the severely dented gas tank fixed (someone felled a tree on it). First took it to a large body shop. They had it for a few weeks and decided they couldn't fix it (welded pins method). The metal was too thick and the pins detached. Then took it to a tractor renovation place and left it for 8 months (apparently out in the weather, I had to repeat the derust process). They assured me repeatedly they'd have it ready but when I finally arrived they had not been able to find anyone to work it. So I started driving from shop to shop and finally found a semi-retired guy to fix it (for a very reasonable price). He did a pretty good job given the condition (yes I could have replaced it). Needless to say, this caused quite a bit of delay/progress hindrance. It came out looking pretty good. The paint doesn't look quite as good as I'd like. Really bad conditions: 1) Indiana is pretty darn wet and humid in May and I just could not get the water down in the line. 2) Bugs galore. Wet paint seems like a bug magnet. 3) Sandable primer (600 grit) just never got smooth enough. 4) Oil based enamel paint takes weeks to dry and gets lots of dings if you're in a hurry. Doing it over I'd use a faster drying paint. The primer I used dries in minutes and is hard as a rock.
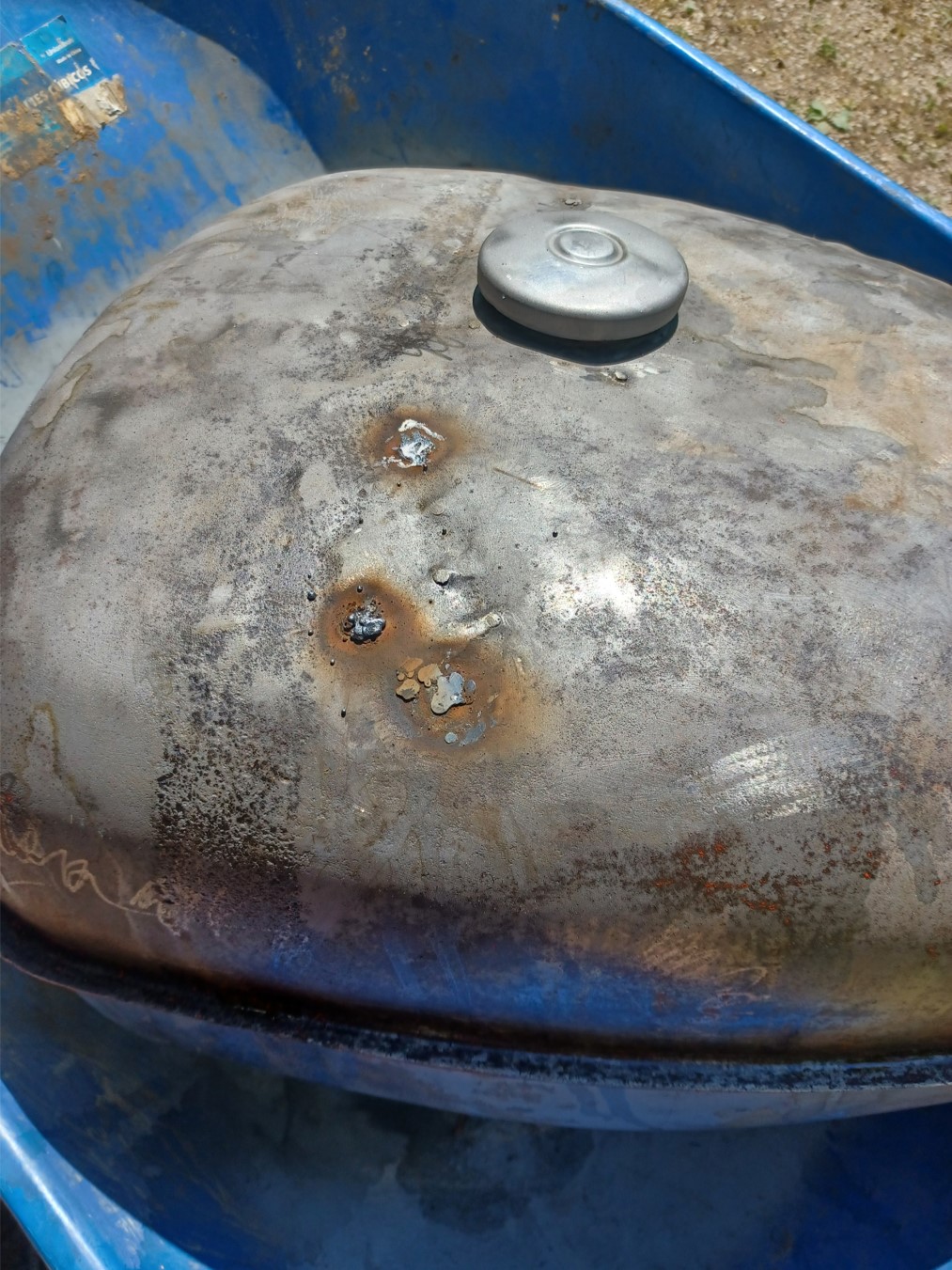
There were a few leaks in the top left over from the welded pins which I had to weld up. Then I used epoxy as the major filler and finished with a skim coat of bondo (no picture, I kept forgetting to take pictures).
Fit check. I should not have put the strap on yet. The paint was still too wet although dry to the touch. The strap goes on over the tin not the tank. Had to make a small paint repair to the tank but it will be hidden under the tin. I had used a rubber strip on the strap rather than a nylon strap material (fixed later). The rubber was really sticky and welded itself to the paint :( The tank was also internally derusted (6 or 7 times) and POR 15 gas tank sealer applied. That stuff seems pretty good. Hard as a rock, coated very well.
I worked on the steering wheel off and on between paint coats and maximized multitasking as much as possible. The original was in really bad shape with most of the bakelight near each spoke all or nearly all missing. That was a lot of small batch mixing. Yes I could have bought 2 of them for the price of the epoxy (not to mention my time). I could have spent a bit more time glazing. Epoxy isn't very well suited to that.
Sand blasted and made some minor repairs to the original shutters. They were in really good shape except for one torn hinge.
Installed. This pic also shows the aftermarket radiator overflow tube. The nipple sticks out way too far and the hose gets crushed by the cowling. I shortened it and routed a smaller diameter tube differently. I'm not quite happy with it and will probably improve it later. The original radiator has a deep recess in the top for the tubing. Again the aftermarket radiator shutter mounting holes didn't line up but was a simple hole size increase to fix adequately.
2000f paint on the new manifold.
Manifold and muffler installed:
Rebuilt original generator with regulator and rebuilt carb installed:
The mounting holes in the aftermarket radiator (made in Turkey) for the cowling didn't match up. I had to increase the hole sizes for the bottom 2 holes (were 1/4 inch holes) to 3/8 inches and then had to slot the bottom holes because they still would not line up by 3/8 or so.
After reversing the radiator mounting plate to position the "hole reinforcement" towards the engine, the radiator fit properly. This is after I rewired and installed the lights and battery. I also had to clean up the threads on the large steering linkage on the lefthand side of the tractor. I then installed two new castle nuts.
Likewise, the hood was pretty beat up. I worked for hours trying to get it straight enough to avoid bondo, but failed. I don't have the nice body metal working tools there that I have at home. But I was running out of time so I'll consider further improvements in the future. The hood and radiator cowling were also welded up by a body shop due to various rips and tears around the mounting holes and the oil filler hole. The headlights were basically decapitated at some point. One could have been easily renovated but the second one would have taken quite a bit of effort (still doable), but I elected to get new ones.
I was running out of time so I elected to do a good enough for now effort on the tin. I can easily address that later. There is more functional work to be done first.
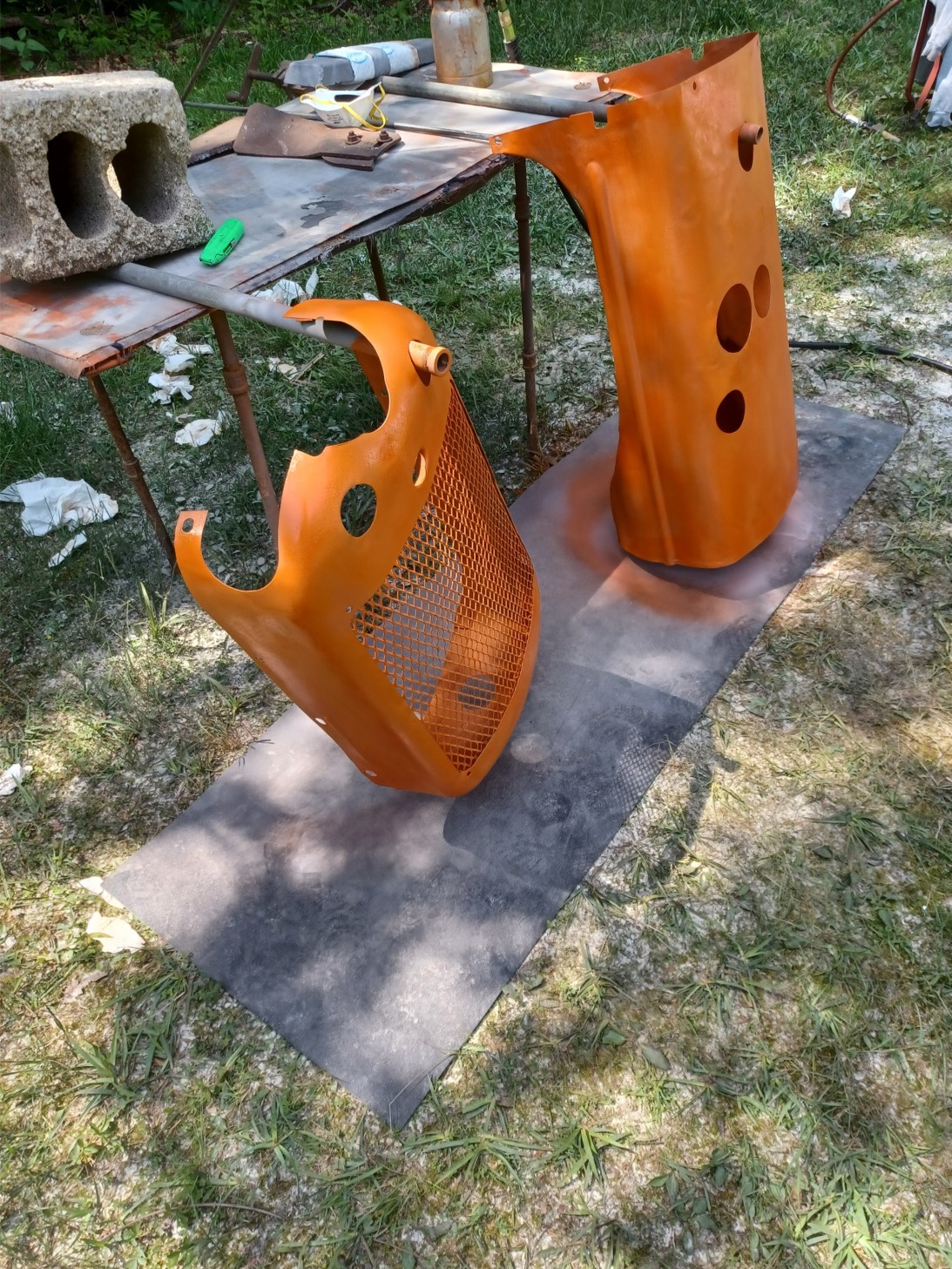
We were able to get the engine to fire and briefly run. It sounded really good, all 4 cylinders fired. However, there seems to be a fuel problem. I suspect my carb rebuild went astray somewhere. There was one jet I was unable to remove and replace, but it was nice and clean. Also, the new battery I installed was discharged when I bought it and self discharged overnight (I checked for leakage and didn't measure any). The behavior is kind of strange with the charger, but it is one of those "automatic" chargers. I just want a switch to select 6V and an ammeter to tell whether it's sending current in. Basically, at 100% charge it turns the engine over really well...for 2 revolutions then it can barely turn it to the next compression stroke. Charge it back up, you get 2 good revolutions then the same behavior. Put it on a load tester, shows good though. I don't trust the load tester. The guy at OReilly told me he's never sold a 6V battery before. I suspect it was in the back uncharged for years. After a full charge (100%), if I disconnect the charger, wait 30 seconds and restart the charging, it behaves as if self discharged. One time the charge indicated it started over at 13%, the next time at 70%. I don't trust the battery or the charger :(
I also had an issue with an aftermarket fuel bowl. It absolutely would not screw into the gas tank. Any of several 3/8 pipe fittings I had laying around worked fine and easily screwed in. I ended up having to buy a die and "fix" the threads. Even then, it wasn't really happy screwing in straight. But I finally got it to go in properly. I fear though next time I remove it to clean/replace the screen, I may not be able to get it back in straight.
So, in working on the timing, we found the FIRE mark on the flywheel. Then we found a CENter mark just after the fire mark...then we found a second CENter mark. Are there two center marks??
------------- 1952 CA13092
|
Posted By: dfwallis
Date Posted: 01 Jun 2024 at 11:19am
I discovered that the paint I've been using (Tallman's) is actually made by Van Sickle. My substandard results are mostly my deficient painting environment and failure to add the hardener recommended. They also have a hard clear coat to add some more gloss. The paint itself isn't extremely glossy. The spray can version also refers to "flat" paint, but it clearly isn't flat. I've also been rushing it a bit to try to squeeze a huge amount of work in my short trips. I'm clearly not a painting expert, sadly.
------------- 1952 CA13092
|
Posted By: dfwallis
Date Posted: 30 Jun 2024 at 10:15am
6/30/2024 Update: I removed the right rear axle to inspect the hand clutch and found it to be a basket case. Springs were loose and rolling around, 3 seats of some sort had fallen out (looks to be ball bearing seats but didn't check closely). My attempts to remove the clutch were not progressing using the pry bar method and unable to locate a puller with a 11.4 inch+ reach and rapidly running out of time, I elected to take it to the former AGCO dealer (successor to where it was purchased) and let them work on the clutch while I resumed prep of rear end parts for painting. A few days after I delivered it I actually did find a suitable puller, but the cost was a good chunk of what it will cost to have it repaired. I did make a homemade puller to try to add pressure while I used the pry bar, but the mild steel was bending under the strain.
The throw-out hub and bearing were both completely locked up, but they cleaned up nicely. The bearing was in excellent shape (given that it was probably not in contact with the clutch housing for 40 years). The adjusting hub/housing looked near new after I cleaned it up. I did need to clean up the threads to stop some binding, but nothing major. I think that the last time the clutch was worked on they just bolted the clutch plates together, but not verified...it may just be rusted fast.
I did get the engine running fairly well. The main issue initially was the throttle control wasn't applying enough force against the wrong carb throttle linkage spring (new one hadn't arrived yet) and it was just idling too slow to continue running. I also had to fix a weeping leak in the carb float bowl. The only remaining leak appears to be the oil drain plug.
Also, initially there was no oil pressure. This caused fear and dread :(, but I was able to prime the pump and got "good" pressure of 10psi at idle and up to 12psi at a slight rev.
I improved the battery cable ground connection. It appears I only THOUGHT about cleaning the paint off the connection (grounding was through the bolt head, but may as well get full surface contact). There's not much evidence that this improved the battery performance, but I think after the engine loosens up and I get it timed properly it will be fine.
I also verified that the new regulator was properly polarized and at the correct voltage before connecting.
Not wanting to fire up the compressor, I elected to use the drudgery method of wire brush and Dremel to clean up the seat spring and shock absorber. They cleaned up well and I got them primed but not painted. The shock absorber was still working reasonably well (pretty sure it's the original). I also removed and cleaned up the small, curved bracket on the seat mount arm.
I prepared the rockshaft and several other linkage parts and the tractor rear end housings for sand blasting. It appears that the poor tractor had been buried in mud up to the seat spring at some point. Caked on thick. Some of it didn't want to succumb to a chisel.
I welded up the right rear final drive oil pan and sealed it with epoxy and POR15 gas tank sealer. Primed and painted, ready to install. I then cleaned up the new rim and tire of all the leaked oil and sand blasting grime that got stuck in the oil.
I welded up the seat. This was a bit difficult because the metal was so thin. Kept burning new holes but I did get all of the cracked areas attached back together and then smoothed by grinding and epoxy. I had to grind off all around the edge. It was jagged and sharp. It's now less jagged and less sharp (but substantially all there).
I applied the bed liner material to the steering wheel. I didn't think the prior new paint finish would hold up very well. It turned out awesome. It looks great, nearly as good as a new one. I forgot to take pics this time, too busy trying to cram as much as possible into a week.
I installed a new 4 stage compressor air dryer on the wall and got it ready for use next trip. This makes 5 stages given the one just after the compressor. If it's still spitting a stream of water out after this, I'm gonna be upset :(
I was able to return the power director hitch-to-hydraulic pump control rod to its plunger hole. Hard to imagine how it got knocked out without doing any damage at all.
I installed a solar trickle charger to the front of the barn and soldered an extension cable to the too short solar panel cable and ran it across the rafters to drop down at the tractor. I bought another one for the garage for dad's 57 Thunderbird, but didn't get it installed yet.
I picked up my new suitcase weights from Fastenal. Four 70 lb weights. I think that will suffice for nearly anything I might want to do. I also got 2 front wheel weights.
Helped my brother unload the new 6-foot finish mower and tarped it.
Took measurements for my new tach sensor design. I'm thinking it will install at the bottom bell housing inspection hole and mount to that drop down loop just in front of it. Since that's probably intended as a "weep" hole, I'll need to consider that.
------------- 1952 CA13092
|
Posted By: steve(ill)
Date Posted: 30 Jun 2024 at 1:28pm
lots of work in the last 2-3 weeks !! Hope you got pictures so you can post when time permits !!
------------- Like them all, but love the "B"s.
|
Posted By: dfwallis
Date Posted: 30 Jun 2024 at 6:00pm
steve(ill) wrote:
lots of work in the last 2-3 weeks !! Hope you got pictures so you can post when time permits !!
|
Didn't get pics this week. It was mostly me getting filthy removing rust and grease and mud from various parts in prep for sand blasting. Saves a huge amount of blasting media if you get the 1/2" thick encrusted sections knocked off first. I got a brief first start and run clip I may put up, but even it is only about 1 second long.
------------- 1952 CA13092
|
Posted By: steve(ill)
Date Posted: 30 Jun 2024 at 8:00pm
I scrape the GUNK and dirt off first.. Sometimes pressure wash if needed for non flat areas.. Washer also takes off the green crud / alge stuff...... After that i needle gun as needed to get 50% of the rust off... Small parts go in the sand blaster after that.. I have not tried the " open air sand blast " method yet.. but do have a tank ready.
------------- Like them all, but love the "B"s.
|
Posted By: HudCo
Date Posted: 30 Jun 2024 at 10:54pm
Posted By: dfwallis
Date Posted: 01 Jul 2024 at 11:21am
Not very interesting but here's 2 seconds of first start and run:
https://www.youtube.com/shorts/-eZ2IIsBJSQ" rel="nofollow - https://www.youtube.com/shorts/-eZ2IIsBJSQ
------------- 1952 CA13092
|
Posted By: Sugarmaker
Date Posted: 04 Jul 2024 at 9:03pm
dfwallis,Your doing a awesome job. Maybe I will get some inspiration to work on our CA too. Regards, Chris and Cheryl
------------- D17 1958 (NFE), WD45 1954 (NFE), WD 1952 (NFE), WD 1950 (WFE), Allis F-40 forklift, Allis CA, Allis D14, Ford Jubilee, Many IH Cub Cadets, 32 Ford Dump, 65 Comet.
|
Posted By: dfwallis
Date Posted: 04 Jul 2024 at 9:25pm
Sugarmaker wrote:
dfwallis,Your doing a awesome job. Maybe I will get some inspiration to work on our CA too. Regards, Chris and Cheryl |
Thanks :) It's a bit challenging for me. I'm doing it by traveling a week here and a week there and cramming as much as I can fit in while I'm there. If AGCO gets the clutch rebuilt within a month or so, it looks good for having it working by the end of the year. I expect hydraulic pump issues, but not going to try it until I can get all the fluid changed out (already largely drained with some water present).
------------- 1952 CA13092
|
Posted By: dfwallis
Date Posted: 05 Jul 2024 at 3:24pm
I had thought I had an extra Arduino Nano to use for the tachometer display project but it appears to be dead. It runs but won't communicate via the USB port. I discovered in testing that it doesn't have enough memory to operate the TFT display though, so I bought a new Nano ESP32 ($22). It's much faster (240Mhz vs 16Mhz) and has lots more memory. It also isn't so picky about the USB cable length. Another "advantage" is that it's 3.3V logic so I don't have to use voltage dividers to attach the display signals. I may have the software mostly done in a few hours. The hard part will be selecting the enclosures and connectors/wiring. I've a reasonably good design for the sensor attachment. I believe a simple plumbing T with short pipe insert(s) will work perfectly with a through-bolt end to end to mount it to the "loop" on the bottom of the bell housing. Then coat the flywheel edge flat black and a single white strip for the IR sensor signal.
------------- 1952 CA13092
|
Posted By: dfwallis
Date Posted: 13 Jul 2024 at 3:14pm
Tachometer project status 7/13/2024:
Code appears to be working. Took roughly a day. Most of the trouble was getting the Nano ESP32 pin references right. With the original nano, referencing the pin number directly worked fine. With the new ESP32, it seems to reference GPIO (internal processor) signals (sometimes). Resorting to using the pin variable names (e.g. D13 for pin 13) seemed to work in all cases. There is a setting in the IDE to change the pin reference to GPIO or PCB but I think there may be a bug somewhere for the Nano ESP32.
It doesn't really amount to much, just counts IR sensor pulses in a given time span and displays the results. All of the conversion factors are based on tractordata.com data so may or may not be accurate in every case.
As designed, it contains code for B, C, CA, WC, WD, WD45, WF, UC. The default is CA if none of the open/ground pins are grounded (4 pins to represent 4 bits so there is a little room for growth). I may or may not include a DIP switch to change the setting in the first one. Verified that it works ok on 6V and per the chip spec, down to 5.5V (of course all the logic is 3.3V).
I need to research whether I can control the TFT brightness. I think it's not controllable on this particular display (off or full brightness). I may program it to go to sleep after 10 seconds or so and wake up if the RPM value changes by some tolerance. I'd kind of like to avoid connecting the touch screen, but it may be necessary as an alternate "wake-up" signal. The ribbon cable for the TFT is on order.
I mostly completed the IR sensor to bell housing mount. I need to adjust the IR sensor sensitivity. New ones seem to be set to minimum which is about an inch from the sensor. That may be just a hair too short for the mounting position.
Of course, I still need to test the pulse count accuracy. It seems like the detection is very fast
I could also add a battery voltage sensor (have one already but it's 5V instead of 3.3V so I'd have to level shift and scale it). That might be handy. Edit: It's a simple voltage divider so I just limit the max input voltage (sense no more than 16.5V) and add a zener to clamp the output at 3.3V so as to try to not damage the Nano input if it exceeds the max sense for some reason.
After all that, then decide on (weatherproof) enclosure and faceplate. It will have an on/off switch as well. The cable will include a weatherproof disconnect at the sensor and at the CPU enclosure so they can be worked on independently. I'm thinking it will mount on the steering column but haven't decided.
The RPM below is how fast I waved a white ink pin in front of the sensor. I verified that a black ink pin doesn't cause a signal. I need to multiply it by 60 in this case (code fixed). I haven't decided on the best sampling method/time span, but I think a 1 second update rate will be ok.
------------- 1952 CA13092
|
Posted By: Dakota Dave
Date Posted: 13 Jul 2024 at 6:26pm
I have a wish bone one that was on my pin hitch CA. It's now on my WD 45. It looks just like the snap coupler wishbone that has a tube welded to the snap coupler en's. To use on a snap coupler I pull the bell off and pin it in place. I got it from either Tony's tractor or OK tractor. I don't rember. It's a class 2 so it's heavy for the CA. But it works well. You just drop the pin hitch drawbar. Un pin the lift cylinders rotate the lift arms up and repin the cylinders. Put the same pin that held the hitch back in with the wishbone end in it's place. It'll lift way more than a CA should. Even with a loader on with the pallet forks and far too much wieght it would lift the front end off the ground
|
Posted By: dfwallis
Date Posted: 13 Jul 2024 at 7:02pm
Dakota Dave wrote:
I have a wish bone one that was on my pin hitch CA. It's now on my WD 45. It looks just like the snap coupler wishbone that has a tube welded to the snap coupler en's. To use on a snap coupler I pull the bell off and pin it in place. I got it from either Tony's tractor or OK tractor. I don't rember. It's a class 2 so it's heavy for the CA. But it works well. You just drop the pin hitch drawbar. Un pin the lift cylinders rotate the lift arms up and repin the cylinders. Put the same pin that held the hitch back in with the wishbone end in it's place. It'll lift way more than a CA should. Even with a loader on with the pallet forks and far too much wieght it would lift the front end off the ground |
Didn't like the design of any I could find. Making my own out of a WD45 one.
------------- 1952 CA13092
|
Posted By: dfwallis
Date Posted: 14 Jul 2024 at 8:06pm
Tachometer project status 7/14/2024:
I modified the pulse measurement approach slightly. Instead of counting pulses, I decided to just measure the time from leading edge to leading edge. I then sample 5 sets in a row and average those to reduce noise. This has the added benefit of being able to handle much higher pulse rates since it drops out of the loop as soon as a pulse transition occurs, ready for the next test. I tested with a 4800 rpm 1.5VDC motor and it appeared fairly accurate (as well as reading a 3x value when it detected each of the 3 fan blades...was surprised it was that fast). I may need to set up a more realistic test though to determine if 5 readings is enough to keep the noise down.
I also added the code for the battery voltage sensor, but I'm unable to find the one I thought I had so a new one is on order for tomorrow (another $5 down the drain). So I may have to tweak the resolution multiplier (changes one number) once I get the details/test of the one I ordered. Next task is to decide if I can dim or blank the display after a period of steady state operation and how/when to "wake up". That's the last software task that I plan, I think.
Edit: Researching the TFT display, it appears that the brightness can be controlled via an analog signal. Others require a PWM signal, some are not controllable. This doesn't necessarily change my approach, but I COULD fairly easily add a brightness control interface rather than just on/off.
------------- 1952 CA13092
|
Posted By: dfwallis
Date Posted: 15 Jul 2024 at 1:38pm
Tachometer project status 7/15/2024: Code for LCD brightness control is complete. Turned out that it is controllable via PWM (not raw analog) which was a simple analog write to the discrete IO port. At present, it dims after 10 seconds and any RPM change of at least 100RPM will set it back to full brightness. I'll finish up the voltage sensor code later today when I receive the sensor (maybe no change).
------------- 1952 CA13092
|
Posted By: dfwallis
Date Posted: 15 Jul 2024 at 8:09pm
Tachometer project status update 7/15/2024: Well, the best laid plans...looks like I'll have to make my own mounting bezel for the LCD. I can't find one the right size. Surely they make one. I've found a few that look close, but can't get the precise dimensions and some measure the size diagonally and some by active area. Not really a big deal, just a temporary road block.
Edit: Added benefit to making my own is that I can make it waterproof. I now have the enclosure, aluminum, and acrylic sheets for the faceplate...my goal for 7/17. I also decided to order a different PCB project board that fits the enclosure a little better than the one I have.
Edit: I decided that the plastic enclosure was not going to be adequately sturdy. Waiting on a metal enclosure. Additionally, the plastic enclosure was a bit bigger than desired. Plastic size choices are limited, but the metal one is much closer to the desired size. Should arrive by 7/24. I can reuse the faceplate as-is with the new enclosure.
------------- 1952 CA13092
|
Posted By: dfwallis
Date Posted: 25 Jul 2024 at 4:52pm
Tachometer project status update 7/25/2024:
Not a huge amount of (mechanical) progress but I have the TFT mounted in the enclosure faceplate. I either need to cut a gasket for underneath the acrylic window or I need to seal it around the edge. Because the faceplate is too flexible, it probably won't seal in the middle with a gasket, so I'm leaning towards black silicon seal around the edge. I guess I could add two more mounting screws in the center.
Mostly waiting on electrical parts which should arrive today and tomorrow. I need the PCB arrangement decided before I drill holes for switch, cables, and mount. The enclosure is an odd size. I didn't find any PCBs off the shelf designed to fit the mounting slides, but I found one that should be very close. I can always make a mounting tray though, no big deal if they don't fit quite right.
I did change the software display brightness dimmer timer to 20 seconds from 10 seconds. Ten seconds was a bit too annoying.
I also researched adding a hydraulic pressure sensor, but the sensor cost more than the entire project so far. Besides I already have a mechanical gauge.
My next trip is set for mid August. I enquired the (ex) AGCO dealer progress on my hand clutch rebuild. There was zero progress, hadn't even looked at it after 3 weeks (told me he'd look at it the following week after I left it). I'm getting the impression there's a lack of interest although he seemed fine and interested when I left it.
The black tape is a kludge to prevent the (metal) TFT sides from contacting the metal enclosure. I also applied some insulating glue. With a positive ground system and a negative ground TFT, who knows what might happen, maybe WWIII :(
Edit: just received the PCB and they fit perfectly so tomorrow I can decide on the internal arrangement and start wiring.
------------- 1952 CA13092
|
Posted By: dfwallis
Date Posted: 26 Jul 2024 at 4:43pm
Tachometer project status update 7/26/2024:
I've completed the enclosure parts arrangement design and drilled mounting, cabling, and switch holes. I believe I can get by with a single PCB by dispensing with the dedicated screw terminals for power and RPM sensor (they'll go to a screw terminal anyway on the Arduino breakout PCB).
The clamp should nicely fit the steering column (I have different rubber insert sizes to try but I believe this is the correct one). Since the steering column is at an angle, the mount can be locked at any angle as well, but the detents are at 90 and 45 degrees. There will be a push button on/off switch (with blue illuminating ring), and there are two waterproof cable clamps. The large fender washers are to distribute the strain to a wider area. I was afraid the ABS enclosure wouldn't stand up to this mounting arrangement, so opted for a metal enclosure instead. It should meet IP6x weatherproofing requirements (resistant but not submersible). I'll probably need to seal the switch better, it seems substandard as-is, although claims IP6 rating. I'll probably include a silica packet inside as well.
------------- 1952 CA13092
|
Posted By: dfwallis
Date Posted: 31 Jul 2024 at 5:05pm
Tachometer project status update 7/31/2024:
PCB wiring is complete barring test issues. Took quite a while to get all the parts. I made a last minute change to add an inline fuse. Not quite happy with the cable mess that resulted. I may improve that tomorrow. It was necessary for me to buy a heavy duty magnifying headset to finish the PCB. I just can't see anymore. Works really well, but the lenses are acrylic. Better not splash any parts cleaner fluids :( Only thing left before I ship it to dad's is to make the header connectors for the sensor itself. I'll make one end of the external cables (plug/sockets) but the other ends will depend on the routing (length) I decide when I install it, so I'll make those ends there.
Two header connectors on the PCB are for the TFT and the on/off switch. The external inputs (power and sensor) attach via the screw terminals on the bottom. This may not be the best mechanical approach, but I was trying to use on-hand parts as much as possible. I may make additional labeling improvements.
------------- 1952 CA13092
|
Posted By: dfwallis
Date Posted: 05 Aug 2024 at 6:05pm
Tachometer project status update 8/5/2024:
First power-up of the PCB was successful (nothing blew up). I do have a few issues to address. 1) The bezel is covering part of the display (thought I was careful, but apparently not careful enough). 2) The scaling for the battery voltage sensor is off. I had set it for a particular prototype resistor value and that resistor disappeared into a black hole. New resistor is a slightly different value (they have a fairly wide tolerance) plus I added a new zener clamp circuit to prevent the input from going over 3.3V (which should give a measurement range up to 16.5V power input)...slow progress in between yard work, pool work, etc.
------------- 1952 CA13092
|
Posted By: dfwallis
Date Posted: 08 Aug 2024 at 4:41pm
Tachometer project status update 8/8/2024:
This is the "final" tach version (depending on how well it works installed). I still need to make the "power" harness (both harnesses will be cut to length on site). For this to work properly, the flywheel outer edge must be coated flat black and a single IR reflective strip will be applied. The reflective surface must be completely smooth to prevent spurious impulses. Depending on whether I can mount it close enough (< 2 inches) a plain white strip of tape or mylar will work. In testing, silver mylar worked slightly better, giving increased range and a stronger more consistent return. The width of the marker is to be determined. I'll start with 1 inch to provide a reasonable duration and reduce likelihood of missed pulses.
I also added a nice foam rubber gasket to the faceplate bezel and cleaned up the surround that was blocking some of the display pixels.
A view inside:
Reading the sensor through a 25 foot cable. Seems reasonably noise immune. Battery voltage is a tiny bit flaky. I tried to suppress noise but I should have probably tried a different noise suppression circuit design.
A side view of the sensor that will mount to the bottom of the bell housing through the loop in front of it (may need modifications on site).
A view of the mounted IR sensor inside the fitting.
A profile view.
A back view of the mount (repeat).
A view looking down at the back.
------------- 1952 CA13092
|
Posted By: dfwallis
Date Posted: 18 Aug 2024 at 10:41am
Here is a closeup view of the bed liner coating on the steering wheel.
Here is a full view. This coating is much tougher than the paint. I had used a very tough/hard paint, but I was worried it wouldn't hold up well. I think this will hold very well and has a good feel to it.
------------- 1952 CA13092
|
Posted By: dfwallis
Date Posted: 18 Aug 2024 at 11:03am
The hand clutch release mechanism cleaned up and painted. The bearing and the throwout adjustment were both completely locked up. I had to use a large pipe wrench to loosen them up. The bearing was cleaned and greased and seems to function perfectly, although it does tend to settle outward a bit when not under load. In order to set the clearance, I had to use a screwdriver to force it together to get the gap tool inserted. I made two new lock screws (ground the tips to fit in the adjustment wheel grooves) and adjusted to just the right length to be able to lock them down.
I was running out of time last trip so I decided to take the axle to the local (former) AGCO dealer for hand clutch repair. I was a little concerned because he did the repair (including religning and new springs/ball bearings) without removing the brake drum section from the axle. I bet that was difficult. In any case, there was little chance of actually testing/gauging the correct tolerances that way. After I got it back, I wanted to test it before I put everything back together. I had to put just enough structure together to operate the tractor (i.e. rails, brakes, seat). Initially it did not seem to be releasing. One thing that was concerning is that on at least 2 occasions, in attempting to release the clutch, a large cracking noise was heard, like a spring/ball seat popping into (or out of) place. This happened two times. After a final clearance adjustment, then the clutch started operating "correctly". It still has a slightly "off" feel to it, but my memories of using it are 50 years old. It does seem to be working correctly though as far as I can tell.
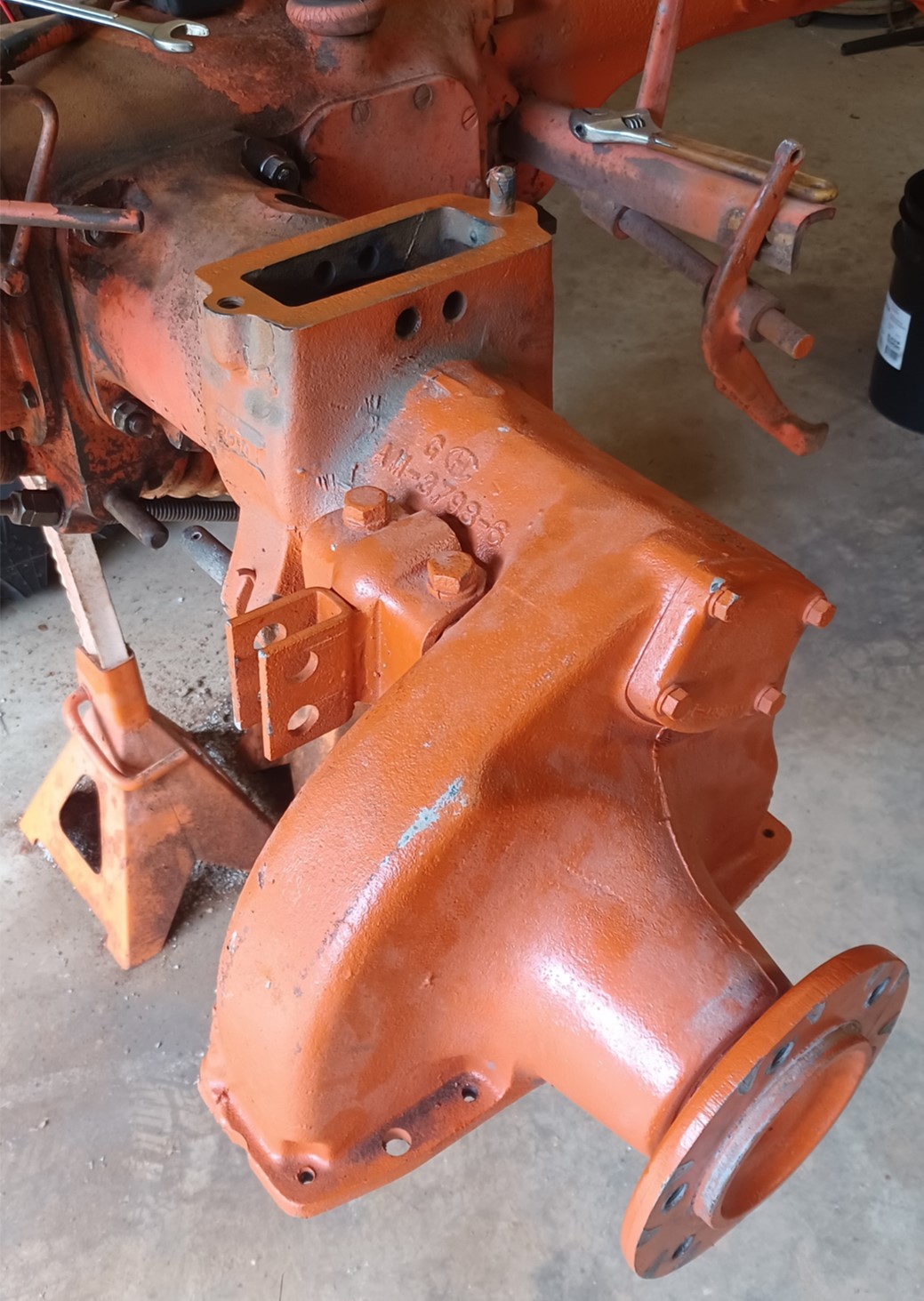
Installed the welded and POR15 sealed final drive oil pan. Added .75qt 80W90 gear oil...no leaks (yay). I will give the other (left side) one the same treatment later (not leaking but I bet it has some water in it like this one did). The rust pattern was weird...just needle sized pin holes with no rust surrounding the pin holes. How is that possible??
------------- 1952 CA13092
|
Posted By: dfwallis
Date Posted: 18 Aug 2024 at 11:24am
I spent days reworking the hood. It was severely damaged in a logging accident plus several hail events. I spent quite a lot of effort my prior trip but just wasn't getting the results I wanted, especially on the sides where the decals go. That was going to look awful. So I bought some body work tools and began pounding the heck out of it. Then I started bondo-ing the worst areas. I would have had to skim the entire surface to get it right. What a mess (not to mention the numerous rips and tears I welded). A sane person would have probably got new tin.
More bondo. Not clearly visible are the severe rust pits all over. Like the seat, some of the rust pits LOOK like they're deeper than the metal is thick :(
After 5000 coats of primer and days of sanding, I'd had enough (red deep fill primer). Good as it's gonna get.
Not really clear but the paint looks MUCH better this time. I had several issues previously:
1) Compressor was spitting out huge amount of water. To resolve, I purchased a 4 stage air dryer (which makes 5 stages given the one at the compressor). This made a massive difference for both painting and sand blasting. After i got the sand blaster cleaned out of all the hard chunks/flakes of sand, it was greatly improved in performance.
2) Massive bugs and tree residue (in May), plus a lot of rain adding to the compressor moisture issues.
3) I was following the directions on the Tallman's paint can previously. This time, I used the advice of "random internet guy" and mixed hardener and naphtha thinner in a 4-1-1 ratio. This massively improved the paint drying time, hardness, and gloss.
------------- 1952 CA13092
|
Posted By: dfwallis
Date Posted: 18 Aug 2024 at 11:38am
A view of the rear end sand blasted and painted. It has 3 coats of primer and 3 coats of color. I bought a nice black seat cushion to cover up the crusty seat :) If I had had another few hours this trip I might have installed the rest, but paint recommends waiting 7-10 days to let the paint cure. Here I just installed what was necessary to test the hand clutch. I also drained and put new gear oil in the tranny. Overall, given that the hand clutch SEEMs to be working, I'm happy with my progress this trip. A lot of progress in 6 days. Even spent some time with my brother trying to get the M running :) One problem I still have is that the governor seems to only bring the speed up to 1/4 throttle. The throttle rod was "straightened" to just one bend just behind the starter and now gets me full range of the control mechanism minus 1 notch (was 4 notches short before...it starts bending the rod at the last notch now). I can probably work the bending of the rod a little more and get the full range of the control correct.
I'm guessing that the governor spring is weak, but it doesn't look to be stretched.
The hydraulic hoses are split and frayed, I guess I'll try to replace those (hopefully I can find some swivel fittings that don't leak, I don't like the way they have to be twisted as-is).
I also cleaned up and removed some large dents in the belt pulley last fall and just installed it.
Edit: An interesting note is that both of the hydraulic cylinders were originally rusted solid in place (in the drawbar pin position). I could actually stand on them and jump up and down and they absolutely would not budge up or down. It took weeks of soaking and prying to get them loose.
Edit: I've decided that I have the throttle "surge" spring installed incorrectly and that is the likely cause of the throttle control issues.
------------- 1952 CA13092
|
Posted By: dfwallis
Date Posted: 18 Aug 2024 at 11:43am
Tachometer project status update 8/18/2024:
As expected, I need to make two tiny mods.
1) The sensor housing itself (plumbing T) was cut to the correct dimensions. But this will require me to mount the sensor on the opposite (rear) side and change the entry point of the cable (no big deal).
2) The display housing needs about 1 inch more clearance to deconflict with the throttle and starter control rods (expected). (also need thinner rubber clamp mounts since the steering column diameter is larger than I remembered).
------------- 1952 CA13092
|
Posted By: dfwallis
Date Posted: 18 Aug 2024 at 2:09pm
Showing where the seat was rusted through and welded and epoxy skim coated. I originally didn't plan on fixing the hole, but decided to go ahead. It came out nice and round-ish. It was sand blasted further before painting but I didn't get a good post paint pic (but you can probably imagine painted rust pits well enough).
Those are some DEEP rust pits.
------------- 1952 CA13092
|
Posted By: CA13414
Date Posted: 18 Aug 2024 at 8:55pm
Your painting looks awesome. You are definitely more OCD than me in that regard. I was like.... one coat of primer is enought.... lets paint!!
Your work is looking awesome!
------------- Helping the aged survive and thrive! 1953 CA
|
Posted By: dfwallis
Date Posted: 22 Aug 2024 at 10:50am
Tachometer project status update 8/22/2024:
Installation clearance modifications:
The tube clamp actually came with a slightly longer extension that I didn't remember. If that one isn't long enough, I've made one that gives me much more flexibility. I added a continuous groove for the pointed set screws to sit in to reduce the chance of accidentally pulling out. There will be lock washers in addition to the jam nuts.
The original clamp extensions only came with fixed set-screw positions. If needed, I can similarly groove it given that it's unlikely that the fixed positions will give the correct angle for the display.
The sensor itself had to be cut to fit the opening at the bottom of the bell housing and the mounting ring just in front. This required me to add an extension on the back side in order to provide enough clearance for the wiring harness. The pipe nipple was grooved on the end to allow the PCB screw to mount correctly. The nipple also decreased the clearance between the through bolt and the PCB so I ground a clearance in the middle of the through-bolt and covered it in shrink wrap tubing. There should be enough clearance, this was just a precaution.
There will be a shortened nipple protruding upward into the bell housing hole to prevent rotation. The exact rubber sealing arrangement is tbd. I intended to use gloss paint, but my last can of gloss black stopped spraying properly before it ran out of paint (broken button receptacle in the can)...:(
------------- 1952 CA13092
|
|