DIY B rear hub socket
Printed From: Unofficial Allis
Category: Allis Chalmers
Forum Name: Farm Equipment
Forum Description: everything about Allis-Chalmers farm equipment
URL: https://www.allischalmers.com/forum/forum_posts.asp?TID=193627
Printed Date: 18 Apr 2025 at 9:23am Software Version: Web Wiz Forums 11.10 - http://www.webwizforums.com
Topic: DIY B rear hub socket
Posted By: KMAG
Subject: DIY B rear hub socket
Date Posted: 20 Feb 2023 at 2:08pm
I gouged up hub nuts tearing B finals apart on parts tractors using a big pipe wrench. Needed something better.
Ta da....
Pipe with flat sections added. I welded in an old 4x4 truck socket inside the pipe for a 1/2" drive. No more damaging axle nuts:)
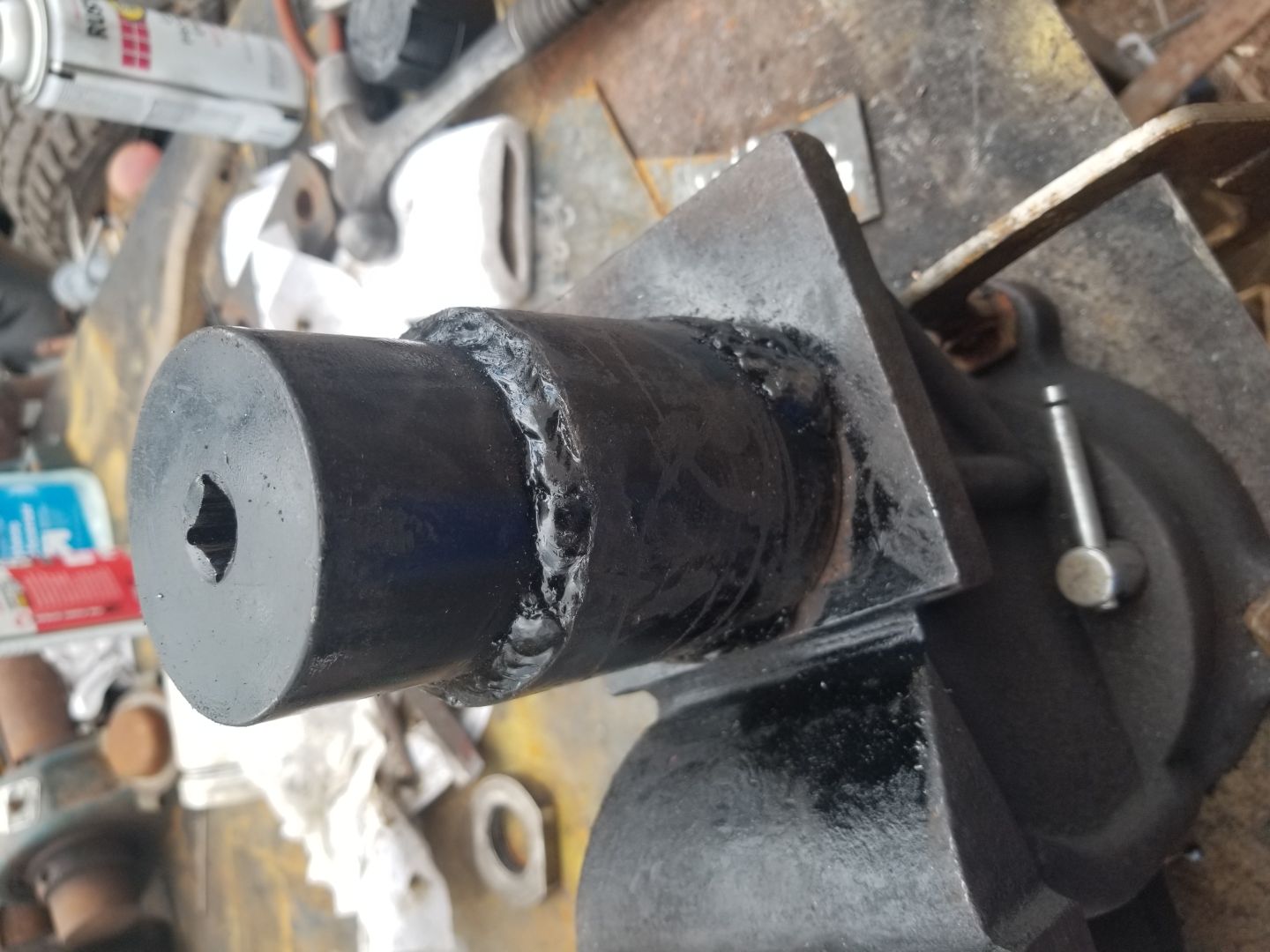 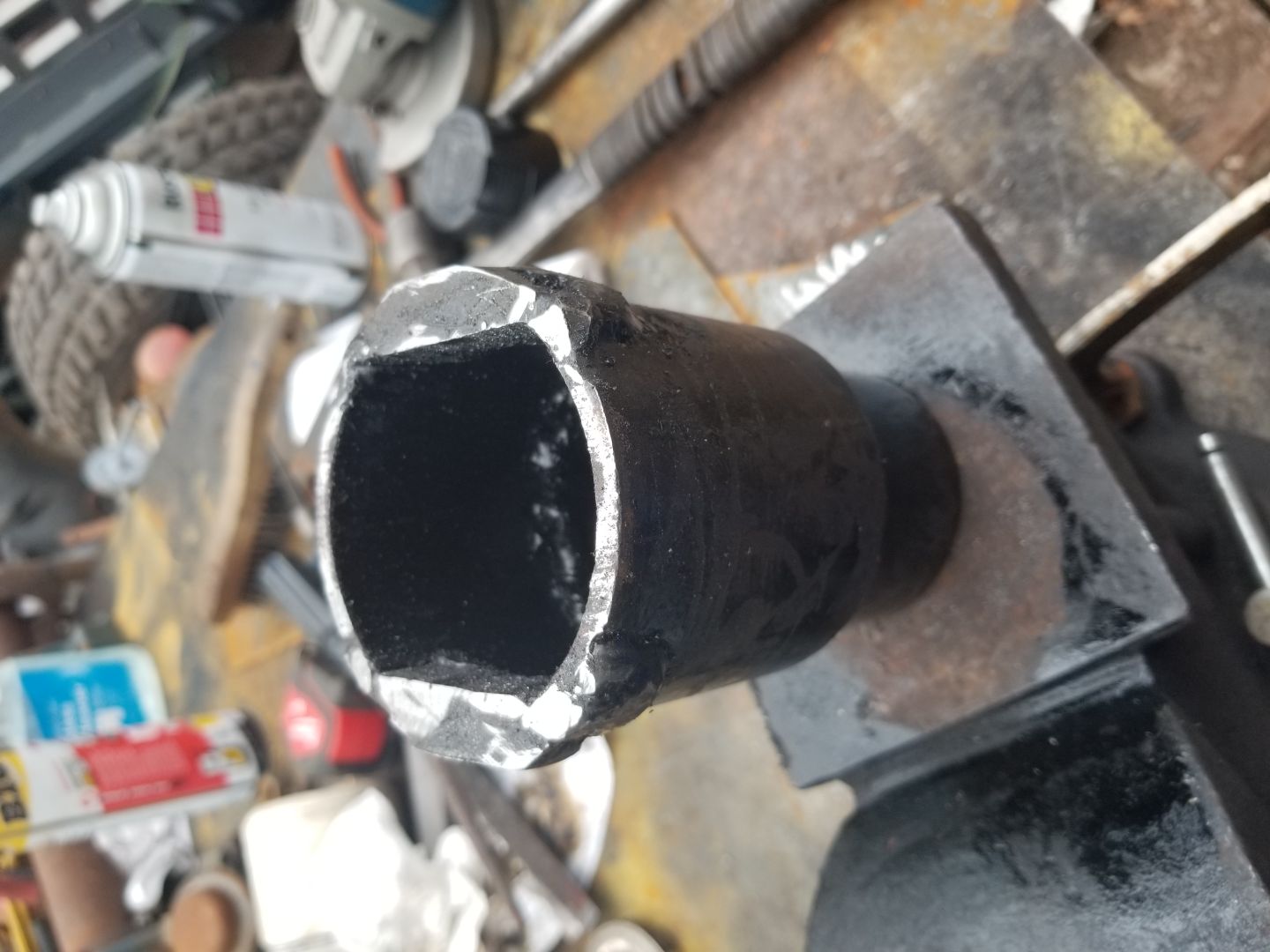
|
Replies:
Posted By: plummerscarin
Date Posted: 20 Feb 2023 at 2:46pm
Looks like that otta work.
|
Posted By: Eric B
Date Posted: 20 Feb 2023 at 3:14pm
Good plan, good socket! I still can't figure out why conventional nuts were not installed from the factory??
------------- Currently- WD,WC,3WF's,2 D14's B. Previously- I 600,TL745,200,FL9,FR12,H3,816 LBH. Earth has no sorrow that Heaven cannot heal!
|
Posted By: steve(ill)
Date Posted: 20 Feb 2023 at 3:31pm
Andy... them nuts are suppose to be in the 500- 600 ft pound torque range.. make sure you use a GOOD bar if your using a 1/2 inch drive... I made a similar socket, but welded to a 2 inch pipe about 4 ft long that i can SIT on the end if it !
------------- Like them all, but love the "B"s.
|
Posted By: B26240
Date Posted: 20 Feb 2023 at 4:10pm
A proper socket like you made makes the job easier nice job!!
|
Posted By: KMAG
Date Posted: 21 Feb 2023 at 5:46pm
Good advice. I added weld to edge of socket opening for more strength, inserted 1/2" drive extension to top socket to center Budd rim lug nut (1.125" o.d.), welded extra chamfered lug nut to top of socket, and welded 1/2" drive extension to top of lug nut. Ugly? Definitely. It should hold up for 1 more tractor assembly and get donated to AC club to share/abuse.
|
Posted By: Gary
Date Posted: 21 Feb 2023 at 6:08pm
A 1/2" Drive Torque Wrench maxes out at 250 ft.lbs.
A 3/4" Drive Torque Wrench maxes out at 500 to 600 ft.lbs.
Per Steve you 'tighten' the nut 500 to 600 ft.lbs.
Loosening a Nut that has been rusting in place over 50 years will be a whole nother story.
Probably need double the Torque - up to 1200 ft.lbs.
Your 1/2" Drive connection will probably twist off before you even get to 600 lbs.
If it were me, I would weld about a 2" nut or greater to your 'special shaped' Tool to fit the B Axle Nut.
Then use a 3/4" Drive Socket to fit the welded nut.
Gary
|
Posted By: KMAG
Date Posted: 21 Feb 2023 at 6:43pm
Gary - I usually use a blue wrench on removals. Torque numbers are greatly reduced:) I am replacing axles with worn splines/hubs and/or seals anyway so heat is not an issue.
BTW: 1/2" drive extension centered the nut for welding to socket, not much for strength - just adds a litle.
|
Posted By: Gary
Date Posted: 21 Feb 2023 at 6:49pm
Yes the 'blue wrench' would definetely help in the 'loosening'.
How about the 600 lb. tightening torque?
G
|
Posted By: KMAG
Date Posted: 21 Feb 2023 at 6:55pm
It'll be weld testing time:) I have 3/4" drive tools (impact/ratchets/bars) - and Budd truck lug sockets with breaker bars. Adding force to tighten will not be a problem.
Problem will be knowing how much torque is being applied. My torque wrenches top out around 200 'lbs.
Suggestions? My impact tops out around 600lbs tightening. Maxing it out is my plan.
|
Posted By: steve(ill)
Date Posted: 21 Feb 2023 at 7:01pm
Andy.... you can GUESS at the torque... 600 ft pounds is 150 pounds of force on a 4 ft long bar...... 100 pounds force on a 6 ft bar.... just use your breaker bar with a 2 inch pipe over it... 
------------- Like them all, but love the "B"s.
|
|