Just purchased a HD4.
Printed From: Unofficial Allis
Category: Allis Chalmers
Forum Name: Construction and other equipment
Forum Description: everything else with orange (or yellow) paint
URL: https://www.allischalmers.com/forum/forum_posts.asp?TID=187943
Printed Date: 04 Sep 2025 at 1:13am Software Version: Web Wiz Forums 11.10 - http://www.webwizforums.com
Topic: Just purchased a HD4.
Posted By: Vetter
Subject: Just purchased a HD4.
Date Posted: 29 Apr 2022 at 4:00pm
Hi everyone, I just purchased a HD4 crawler, believe to be a 71 or 72. I need to do alot of work to the track, the right side came off yesterday. I got it on today but found alot of looseness which I will have to address. I think the PO had the track too tight which caused alot of binding. One odd thing is I can't find any grease fittings for the track rollers, the manual I have with it says there's button head fittings on the pins, but nothing is there. I didn't think these early models would of came with sealed rollers, or could someone of modified these?
|
Replies:
Posted By: DMiller
Date Posted: 29 Apr 2022 at 4:37pm
Rails have no lube, Rollers under MAY have had when new, replacements not so much. Rails for these are unobtainable.
|
Posted By: Vetter
Date Posted: 29 Apr 2022 at 5:34pm
DMiller wrote:
Rails have no lube, Rollers under MAY have had when new, replacements not so much. Rails for these are unobtainable. |
Yes, the rail pins wouldn't. I think the rails look pretty good, there seems to be alot of material remaining. The tensioner and front shims for the idler pulley has a few loose and missing bolts. Good to know about the roller pins, thanks for the information.
|
Posted By: Ray54
Date Posted: 30 Apr 2022 at 12:59pm
AC used sealed only grease every 1000 rollers rollers back as far as the 1950's. So I would not have expected them to do any less on your little guy.
|
Posted By: Vetter
Date Posted: 30 Apr 2022 at 2:39pm
Ray54 wrote:
AC used sealed only grease every 1000 rollers rollers back as far as the 1950's. So I would not have expected them to do any less on your little guy. |
That's good to know. But the only reason I ask is the Operation manual and shop manual both say they are greaseable and need to be done every 100 hours? So I'm assuming if they are sealed they need to be removed then dismantled every 1000 hours?
|
Posted By: Ray54
Date Posted: 01 May 2022 at 7:18pm
Back in the 60 and 70 a white grease was what was used on the AC rollers. Pull the plug shove nozzle in, which put new grease in the back. You pumped until new clean grease was coming out around the pipe nozzle, put the plug in and you had it grease for the year.
When I ran out of the last bucket of the white in the 90;s just used what ever roller grease I had for Cat 100 hour rollers.
Well if the manual says a 100 hours, grease is cheap compared to parts, and labor to change parts. On Cat 100 hour rollers you have be careful if you use a normal grease gun and not a low pressure volume bucket pump made to grease track roller. The grease gun puts out a lot more pressure and you can blow the rear seal out and not know it.
|
Posted By: Vetter
Date Posted: 02 May 2022 at 5:13am
Ray54 wrote:
Back in the 60 and 70 a white grease was what was used on the AC rollers. Pull the plug shove nozzle in, which put new grease in the back. You pumped until new clean grease was coming out around the pipe nozzle, put the plug in and you had it grease for the year.
When I ran out of the last bucket of the white in the 90;s just used what ever roller grease I had for Cat 100 hour rollers.
Well if the manual says a 100 hours, grease is cheap compared to parts, and labor to change parts. On Cat 100 hour rollers you have be careful if you use a normal grease gun and not a low pressure volume bucket pump made to grease track roller. The grease gun puts out a lot more pressure and you can blow the rear seal out and not know it. |
I just sold a JD40 which I used cornhead grease (90 wt and grease mixture) on the rollers, and it was the same way, you had to be careful not to pump the rollers with too much pressure or the seals would give out. I would use this grease on the AC rollers because the manual says to use 90 wt, but there is no way to grease them that I can find. The manual says there should be button head grease fittings but there is nothing there? So how do you service sealed rollers? If they aren't supposed to be serviced, can they be taken apart to be cleaned and greased? I dought I'd be able to find replacements for this HD4.
|
Posted By: Ray54
Date Posted: 02 May 2022 at 2:36pm
I have had some Cat sealed for life rollers. The first one I saw a leak on lasted only a day or two. So the next one I made a grease fitting and pumped it full. Found a plug that screwed in and drilled it for a fitting. It has lasted at least a 1000 hours. I checked it several times and had a lot of grease and was not leaking so you could see it. Still good I hope but tractor is rusting away awaiting other work I may never get to. For a time every time something happened to one old D6 another was calling my name to put a offer on it out there.I lost track but pieces of 8 I think. The Cat ones look like they are filled with ATF or something equally thin. So I would fill any of them with cornhead grease.
|
Posted By: Vetter
Date Posted: 02 May 2022 at 6:09pm
Ray54 wrote:
I have had some Cat sealed for life rollers. The first one I saw a leak on lasted only a day or two. So the next one I made a grease fitting and pumped it full. Found a plug that screwed in and drilled it for a fitting. It has lasted at least a 1000 hours. I checked it several times and had a lot of grease and was not leaking so you could see it. Still good I hope but tractor is rusting away awaiting other work I may never get to. For a time every time something happened to one old D6 another was calling my name to put a offer on it out there.I lost track but pieces of 8 I think. The Cat ones look like they are filled with ATF or something equally thin. So I would fill any of them with cornhead grease. |
Thank you for all the info. After doing some adjustments to the brakes and clutches, I was able to find out someone just put a new steering clutch and brake band on the right side. But I'm going to have to put a new steering clutch and brake band on the left side, I'm hoping it will work for the summer. Surprising they only replaced one side, if they had the whole thing apart? I also found out the track adjusters are all the way out, they are only grabbing on the lock plate, probably why I threw a track, looking on the brite side I was able to get all the bolts loosened with nothing breaking. So looking things over I decided I'm going to remove a track link on each side, for what I'm going to use this dozer for, I think that would be the best option. Does anyone know where I could get a couple master pins for this? The links are Berco MH228 if that helps.
|
Posted By: Coke-in-MN
Date Posted: 02 May 2022 at 6:22pm
Removing a link will place roller to sprocket contact point in wrong place which will strain the machine -especially the rear outboard sprocket bearings - After rebuilding both rear cases with new bearing holding machined parts welded into cases and at a $$$ cost it's not something i would do . Find out if track can be turned on pins and bushings before going the extreme you mention
------------- Life lesson: If you’re being chased by a lion, you’re on a horse, to the left of you is a giraffe and on the right is a unicorn, what do you do? You stop drinking and get off the carousel.
|
Posted By: pinball
Date Posted: 02 May 2022 at 7:02pm
my h has one roller on each side that has the buttonhole, i don't have that fitting to grease them. the others have grease zerts, probably been replaced at some time or another. the best advice i can give you is to make sure your final drives have oil in them. hopefully you won't but some parts are very hard to find and expensive for sure. the track is suppose to have 1 1/2 inch slop in it but one of the biggest reasons those tracks try to come off is the front idler. keep it full of grease will help. if those pins wear it causes the idler to wobble some. ive had mine for over 10 years. im in no hurry so it serves me well. mine is a 2200 gas. yours is a 2200 diesel. tae care of it, fix it right when needed and enjoy it,
|
Posted By: Vetter
Date Posted: 03 May 2022 at 5:27am
Coke-in-MN wrote:
Removing a link will place roller to sprocket contact point in wrong place which will strain the machine -especially the rear outboard sprocket bearings - After rebuilding both rear cases with new bearing holding machined parts welded into cases and at a $$$ cost it's not something i would do . Find out if track can be turned on pins and bushings before going the extreme you mention
|
For the life of me I can't see how removing a track link can change the contact points on the sprocket, not saying it doesn't happen, I just can't see how? I understand the wear has changed things, but that has already been done and I look at it as the sprocket and links have wore together. Like removing a link from a motorcycle chain, it shortens it, but doesn't change its geometry? I know that's is over simplifying it. I'll look into flipping the bushings and pins, but I'm not sure that would be enough to remove enough slop for the tensioners to thread into the yokes properly.
|
Posted By: Vetter
Date Posted: 03 May 2022 at 5:38am
pinball wrote:
my h has one roller on each side that has the buttonhole, i don't have that fitting to grease them. the others have grease zerts, probably been replaced at some time or another. the best advice i can give you is to make sure your final drives have oil in them. hopefully you won't but some parts are very hard to find and expensive for sure. the track is suppose to have 1 1/2 inch slop in it but one of the biggest reasons those tracks try to come off is the front idler. keep it full of grease will help. if those pins wear it causes the idler to wobble some. ive had mine for over 10 years. im in no hurry so it serves me well. mine is a 2200 gas. yours is a 2200 diesel. tae care of it, fix it right when needed and enjoy it, |
I checked the final drive oil and it looks new, so someone must of just changed it. I hope that is a good thing, and some serious issues didn't caused it to be pulled apart? But it all seems fine. I'm a little concerned about the torque converter, something is slipping but it may of just been the steering clutches not adjusted correctly. What RPM do you run your machine to get a good forward power? When I adjust the tracks to the proper spec of 1 1/2" to 3" following the maintenance manual I received, the track tensioner is completely out of the yoke and only threaded into the lock plate. Which causes the yoke and idler wheel to have alot of slop up and down and side to side. Someone even removed the front bolts on the spacers for the idler wheel so it could be adjusted farther forward. I'm wondering if even these tracks and links are not original AC.
|
Posted By: Codger
Date Posted: 03 May 2022 at 8:04am
Before you did anything I'd ensure you have at least eight inches of adjustment in your front idler. Six inches is your track pitch and if you remove a link and can only bring that idler back say five inches, you are not going to be able to remount the track without a lot of additional work. If you can only bring the idler back seven inches, it's going to be a stretch whether you will get the track remounted or not without another machine or hydraulics to assist you. On top of all that keeping proper track tension will be a challenge at best. Too tight and everything will be very short lived.
I'd start off with measuring your track pitch and undercarriage evaluation to know where you are at the start. Here is a blurb from an HD4 service manual on the track pitch:
This also breaks track measuring down a bit:
https://www.youtube.com/watch?v=WCGxq4ivn_s
I've spent a lot of hours welding up chains, sprockets, idlers, etc. to allow remachining of the same to extend the service life of machines when parts are NLA as you will experience with most AC construction equipment.
I also remember those machines on the grounds at the Springfield plant when they were new.
|
Posted By: Coke-in-MN
Date Posted: 03 May 2022 at 8:06am
With 6 different tracked vehicles over last 40 years and 2 now still used - With 15 or more Motorcycles with chain drive primary and final drives The idea the chain pitch changes as chain stretches from wear is well known . You do not measure wear between pin to pin of 2 links but over 4 or more The rollers or bushing has to align with sprocket tooth to index - inside wear is one part you can't see, outside wear at sprocket contact is easy to see and feel . If you have ever seen the inside of a crawler chain of the metal to metal wear with egg shaped inner hole in bushing and one side of the pin worn in over 1/4" it's easy to see how alignment becomes a issue . A motorcycle chain is something I replace at about 10,000 miles but lube several times during that period , in fact I keep a couple chains s I can remove and clean one chain while riding with another being cleaned and re-lubed as well as carrying a small bottle of chain lube on bike also . My H4 D was owned for over 10 years with one rebuild of tracks (turning) . My HD5G I have ran over 40 years and only ONCE did I shorten track one link - to get it moved from jobsite onto trailer to get it to the shop to replace the tracks . Removing that 1 link changes full geometry of track to sprocket wear pattern - in the short time it works but for machine life it's a real problem . If you ever noticed on a motorcycle the hooked shape pf a sprocket tooth it's from chain wear - and it's the same on a crawler . with an elongated chain, the rear sprockets will quickly get worn so the chain skipping will occur with a new chain – due to worn rear sprockets. Rear sprocket wear (except an extreme one) is impossible to determine by looking. Even a fraction of a millimetre wear is enough to cause skipping of a new chain.
------------- Life lesson: If you’re being chased by a lion, you’re on a horse, to the left of you is a giraffe and on the right is a unicorn, what do you do? You stop drinking and get off the carousel.
|
Posted By: Les Kerf
Date Posted: 03 May 2022 at 8:19am
[/QUOTE]
For the life of me I can't see how removing a track link can change the contact points on the sprocket, not saying it doesn't happen, I just can't see how? I understand the wear has changed things, but that has already been done and I look at it as the sprocket and links have wore together. Like removing a link from a motorcycle chain, it shortens it, but doesn't change its geometry? I know that's is over simplifying it. I'll look into flipping the bushings and pins, but I'm not sure that would be enough to remove enough slop for the tensioners to thread into the yokes properly. [/QUOTE]
Well, yes and no. Removing a link allows you to take all of the slack out of the chain; the chain has already 'stretched' due to wear, and if you pull it tight like a fiddle string then each link is now slightly longer, thus preventing the bushings from settling down into the sprocket.
The contact point is now higher up on the sprocket tooth and above the previous wear area. Since the same amount of force is now concentrated in a smaller area, this area will wear more rapidly than before, hastening its demise.
If the pins and bushings have never been turned, it will indeed help to have this done because the bushing area would then fill the sprocket more fully, plus the pin and bushing contact area is at a different spot inside. The chain will appear to be shorter.
If the pins and bushings have already been turned, then your options are now:
A) Run it as-is and hope the track stays on B) Find a better set of tracks (good luck with that!) C) Park it and use it for a yard ornament D) Scrap the machine E) Remove a link and get what little life remains out of your machine
If you do remove a link, run the tracks as loose as you can get away with
|
Posted By: Vetter
Date Posted: 03 May 2022 at 10:17am
Thanks for the replies and information everyone, all very helpful! I was able to get the fluids changed and everything adjusted, put the batteries back in and drove it a little to see how it runs. Everything seems to run good now except the track issues. I checked out the bushings and they have already been rotated once. The tracks definitely can't be run the way they are now, just because with the threaded adjuster not in the yoke the tracks won't stay on very long with everything being loose, and I'm sure other things will break. So the dilemma of letting it sit until I can possibly find replacement parts, or remove a link. I'll have to do more research and see what replacement parts I can find, if any.
|
Posted By: Vetter
Date Posted: 03 May 2022 at 3:52pm
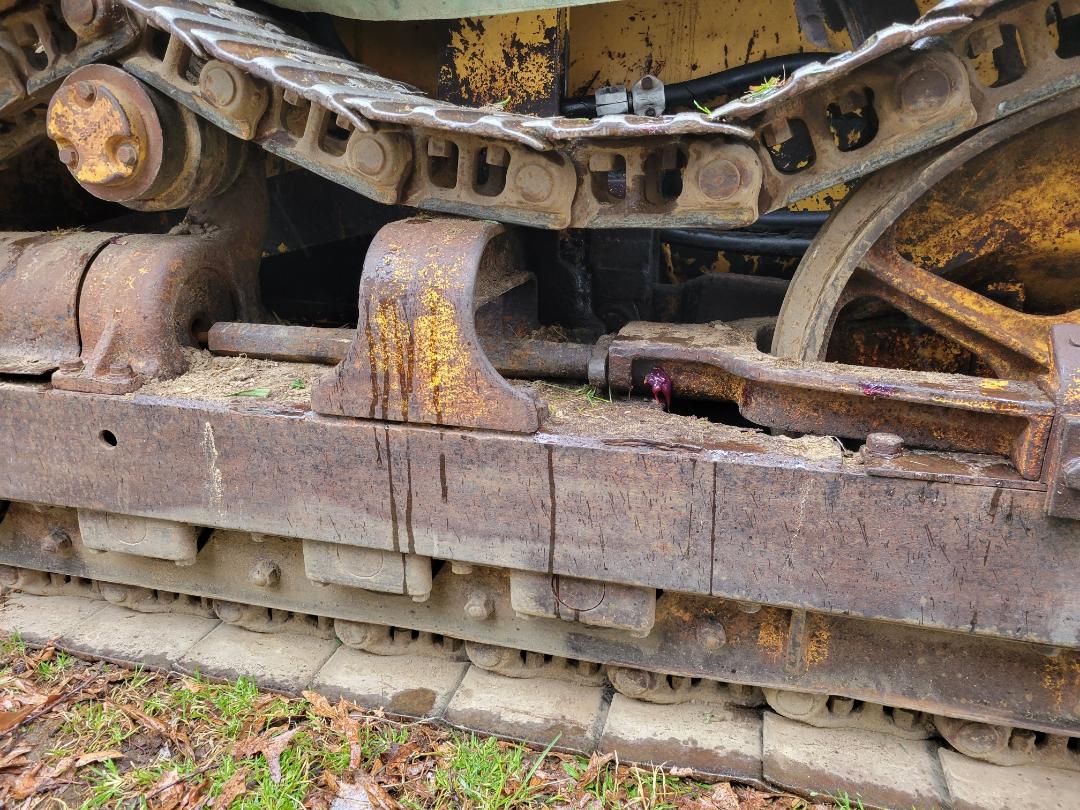 Just to show what I'm dealing with, I turned the tensioner into the yoke about 1" to the end. At this point I don't think I have any choice but removing a link if I want to use the Dozer.
|
Posted By: steve(ill)
Date Posted: 03 May 2022 at 4:24pm
I think removing a link, or maybe lengthen the adjuster rod a couple inches is a good SHORT TERM SOLUTION for a TEST. ..( im not sure there is enought LENGTH to remove 1 link and still FIT).... You just got the tractor, so you may want to RUN IT a little before you get in deeper..
I have heard of some that use "OTHER CHAINS" not built for the HD 3-4.. You need to change the sprockets to match the NEW CHAIN PITCH, and make sure the top rollers can fit inside the rails, and the bottom rollers fit outside... Some modifications may be needed.......... i thought the CASE 450 was "close"... but you need to adapt the sprockets to the Allis machine.
https://www.allischalmers.com/forum/hd4-tracks_topic143798.html" rel="nofollow - https://www.allischalmers.com/forum/hd4-tracks_topic143798.html
------------- Like them all, but love the "B"s.
|
Posted By: steve(ill)
Date Posted: 03 May 2022 at 5:54pm
some more data.......
https://www.yesterdaystractors.com/cgi-bin/viewit.cgi?bd=crawlers&th=107568" rel="nofollow - https://www.yesterdaystractors.com/cgi-bin/viewit.cgi?bd=crawlers&th=107568
------------- Like them all, but love the "B"s.
|
Posted By: Vetter
Date Posted: 03 May 2022 at 6:00pm
steve(ill) wrote:
some more data.......
https://www.yesterdaystractors.com/cgi-bin/viewit.cgi?bd=crawlers&th=107568" rel="nofollow - https://www.yesterdaystractors.com/cgi-bin/viewit.cgi?bd=crawlers&th=107568
|
Thanks Steve, great information!
|
Posted By: gemdozer
Date Posted: 03 May 2022 at 7:18pm
You should turned the rod adjuster on the other side and maybe the tread in yoke are no more good and if the adjuster rod tread are in good condition you need to turning the nut until the track are oké and dont forget to lock the nut with the 2 bolts.
|
Posted By: Vetter
Date Posted: 04 May 2022 at 5:33am
This is a pic of the left side I have adjusted to the factory 1 1/2" of sag. The tensioner rod is adjusted completely out of the yoke and only grabbing on the lock plate. Notice the front of the slide is completely forward, even the front bolts were removed on the shims to allow it to move further forward. So even if I shimmed the tensioner rod there is only about 1/4" the idler wheel could go further forward, but then the issue of the tensioner rod allowing the yoke to move around would still be a problem.
|
Posted By: gemdozer
Date Posted: 04 May 2022 at 6:14am
The rode adjustement right side is adjusted correct and we can see the tread on rod but the left sde we can't se any traid he is complet desajusted we should see the tread on rod . HECTOR
|
Posted By: Codger
Date Posted: 04 May 2022 at 7:50am
Is the parts wear pretty even side to side on the undercarriage, or is the right worse than the left? From your first photo it looks as you may have a skipping problem with the chain and sprocket wear once the track is tightened up. I'm not certain you will be able to fit the track with a link removed as Steve pointed out also. Thinking I would fabricate another adjusting rod of additional length to tighten them up and prove the tractor worthy of further investment?
As a pushing dozer, worn out street pads will do you no favors and it looks like the track pad capscrews are just about the same height as the pads from wear.
|
Posted By: Vetter
Date Posted: 04 May 2022 at 8:30am
Codger wrote:
Is the parts wear pretty even side to side on the undercarriage, or is the right worse than the left? From your first photo it looks as you may have a skipping problem with the chain and sprocket wear once the track is tightened up. I'm not certain you will be able to fit the track with a link removed as Steve pointed out also. Thinking I would fabricate another adjusting rod of additional length to tighten them up and prove the tractor worthy of further investment?
As a pushing dozer, worn out street pads will do you no favors and it looks like the track pad capscrews are just about the same height as the pads from wear. |
Yes, the wear is even on each side. The little bit I drove it, the sprocket didn't skip. And yes, even the capscrews are worn. The problem with making an extended tensioner,is there is no more forward adjustment, it's maxed out now. So really, the cheapest alternative right now is remove a link. There's plenty of slop right now that removing a link should be no problem.
|
Posted By: steve(ill)
Date Posted: 04 May 2022 at 8:54am
It may work Vetter.... but each link is 7-8 inches between the pins ? That seems like a lot to make up..... But you dont know till you try........
You have one side stretched out to the proper adjustment... When you relax that side, does the front idler move back ( or can it move back ) 7-8 inches as needed ?? ...... or maybe you only need 4 inches as you gain length on the TOP chain and the BOTTOM chain going around the idler.....
------------- Like them all, but love the "B"s.
|
Posted By: Vetter
Date Posted: 04 May 2022 at 9:05am
steve(ill) wrote:
It may work Vetter.... but each link is 7-8 inches between the pins ? That seems like a lot to make up..... But you dont know till you try........
You have one side stretched out to the proper adjustment... When you relax that side, does the front idler move back ( or can it move back ) 7-8 inches as needed ?? ...... or maybe you only need 4 inches as you gain length on the TOP chain and the BOTTOM chain going around the idler.....
|
Yes, when I take tension off the yoke by threading the tensioner all the way into the yoke, the idler moves back 6" no problem. I'm hoping that is enough, since these links are 6" pin to pin. I'm working on getting the pads off now, not bad just going slow because the bolts are worn. Atleast there isn't much corrosion seizing everything together with this machine. Trying to look at the bright side!
|
Posted By: Coke-in-MN
Date Posted: 04 May 2022 at 1:52pm
Your left side track is facing the wrong way - and also it looks like sprocket teeth are SHARP and worn beyond limit . Track pads are loader pads not dozer - Kind of a point where it might be a time to find another owner rather than chase good money into something - One reason my H4 got traded off - became anothers problem and not mine
------------- Life lesson: If you’re being chased by a lion, you’re on a horse, to the left of you is a giraffe and on the right is a unicorn, what do you do? You stop drinking and get off the carousel.
|
Posted By: Vetter
Date Posted: 04 May 2022 at 3:10pm
Coke-in-MN wrote:
Your left side track is facing the wrong way - and also it looks like sprocket teeth are SHARP and worn beyond limit . Track pads are loader pads not dozer - Kind of a point where it might be a time to find another owner rather than chase good money into something - One reason my H4 got traded off - became anothers problem and not mine |
Thanks about the track info, I didn't even notice that. I did know about the loader tracks, I assumed that was original because it was setup for a backhoe too? My initial intent was to weld on some grousers eventually, but with all the wear that isn't going to happen. I just bought this thing, looking back at things when I bought it, that's exactly what they did I think. I couldn't consciously sell this to someone knowing the issues, and if I was upfront with them I certainly could never get close to my money back. This is my mistake at this point, so I'm committed to get it running as it should. I've done dumber things in the past, but not willing to give up just yet.
|
Posted By: Coke-in-MN
Date Posted: 04 May 2022 at 3:42pm
On my tracks - I welded on rebar - 2 pieces to each pad - been running that on my HD5G for years . On my H4 I did the same - and on the D6 just 1 piece onto grouser used 6/8 rebar and welded it on both sides using 7024 drag rod at higher amps My H4 also used a quick attach backhoe but I ended up breaking 3 rear axles over years as hoe put full weight onto sprocket bearings . Still have the AC 615 hoe attachment - as cylinders are same as on my AC715D TLB machine . Clearing some land a few years back found the 715 would push more than the HD4 would in speed and power .
------------- Life lesson: If you’re being chased by a lion, you’re on a horse, to the left of you is a giraffe and on the right is a unicorn, what do you do? You stop drinking and get off the carousel.
|
Posted By: Vetter
Date Posted: 04 May 2022 at 4:47pm
My plan was to find a small backhoe, possibly from a skid loader and fabricate it to fit with the same quick detach that's currently on the dozer. I see them at the auction quite often.
|
Posted By: Vetter
Date Posted: 06 May 2022 at 2:53pm
I was able to remove a link on each side, and get the LH track going in the proper direction while I had it apart. The pic shows the RH side adjusted to the 1 1/2" sag per the maintenance manual, while the LH hasn't been adjusted yet. I feel much better now that the tensioners are threaded into the yokes, and the whole idler assembly tracks better. I can start putting some of the bolts back in the shims that were removed to tighten it up more. I will only be using this for light duty such as driveway grading, until hopefully I can find replacement tracks and sprockets. At least now I can run the machine and get the feel of everything and start cleaning it up with some fresh paint.
|
Posted By: gemdozer
Date Posted: 06 May 2022 at 3:07pm
The left side adjustement is oké but the right need more adjustement.
|
Posted By: steve(ill)
Date Posted: 06 May 2022 at 4:23pm
or the other way around....RT/LT.... LOOKS GREAT !! GOOD JOB.... Lets hope the chain FITS the sprockets good enough that it doesn't grab and pop !!
------------- Like them all, but love the "B"s.
|
Posted By: steve(ill)
Date Posted: 06 May 2022 at 4:27pm
Wha-cha got in the way of a press ? How tight were the pins ? Pull together with a comealong or winch ?
------------- Like them all, but love the "B"s.
|
Posted By: Vetter
Date Posted: 06 May 2022 at 4:41pm
steve(ill) wrote:
Wha-cha got in the way of a press ? How tight were the pins ? Pull together with a comealong or winch ? |
I used a old ball joint press I've had for about 30 years, it fit perfectly. The pins were very tight, I found if I tightened up the press as much as I could, then hit it with a hammer the pins moved, did this a couple of times and they came out. I used my tractor to pull the track when I removed it, and a comealong to tighten the tracks together.
|
Posted By: Vetter
Date Posted: 06 May 2022 at 4:43pm
A pic of the tractor helping out.
|
Posted By: Codger
Date Posted: 06 May 2022 at 4:59pm
You done well and I too am glad you got it accomplished. I've used my old OTC ball joint press for the task on a small IH dozer years ago but wasn't as fortunate as you. I had to purchase a forcing screw once done as it was bent pretty fair from the sledgehammer blows it endured. It got the job done however.
|
Posted By: Vetter
Date Posted: 06 May 2022 at 5:12pm
Codger wrote:
You done well and I too am glad you got it accomplished. I've used my old OTC ball joint press for the task on a small IH dozer years ago but wasn't as fortunate as you. I had to purchase a forcing screw once done as it was bent pretty fair from the sledgehammer blows it endured. It got the job done however. |
Thanks! The threads on my ball joint press are almost done, I will have to be doing the same soon.
|
Posted By: Codger
Date Posted: 07 May 2022 at 6:35am
If your machine turns out to be reliable and purpose serving for you there is the chinese option out there for undercarriage parts. I have an 11B dozer myself and spent about an hour and a half exchanging emails with a gent in China via "Alibaba" who was very fluent in english and versed in undercarriage parts. Long and short of the story is a mated pin and bushing set was $49.00 each with a minimum of 100 each for my tractor. These I was told were quality steel hardened to 45C on the Rockwell scale which is the same as originals. I was assured they would serve as the originals did. Truth? I don't know of course as no direct experience. As mentioned in earlier postings the sprockets and chains are easily welded up for remachining to proper dimensions and these seem to hold up pretty fair if the correct filler material is used. Myself and now deceased uncle have done many in the past. It is the same with rollers, and idlers too. Most anything can be rebuilt, or built up and remachined true, but finding someone to do the work cost effective.....
There are still several H, and HD 3, 4 series out there needing new pins and bushings and if the participants would come together and share an order placement, great savings could be spread amongst the masses. Sad to say you'd be hard pressed to find an american machine shop to make p&b sets for the price.
Your track pads only seem to be worn down near smooth to the bolt heads. 7024 rod is a great filler to use for bonding "grouser" bars to the existing pads but it is a horizontal and flat only filler rod as has a very "fluid" puddle. Great rod for platform decking as instance. 1/2" strip about 1-1/4" tall/wide welded on both sides to the pads would really dig well and not fold over very easy.
|
Posted By: Coke-in-MN
Date Posted: 07 May 2022 at 11:04am
I welded the rebar to the pads - while on the machine - I clamped bar to pad at point it was on pad on front idler - another bar to track pad at rear sprocket - then welded ONE SIDE of bar - moved track and attached another 2 bars / welded and moved track This way rod and pad allowed horizontal weld to fill easily and chip easily . Actually 4 or 5 bars could be attached at each end of machine on each turn (not just 1 bar at each end)
------------- Life lesson: If you’re being chased by a lion, you’re on a horse, to the left of you is a giraffe and on the right is a unicorn, what do you do? You stop drinking and get off the carousel.
|
Posted By: Codger
Date Posted: 08 May 2022 at 1:20am
You did it the same way I would have; on the machine and either perfectly 90 degrees. or slightly less to allow a slight "vee" shape for the weld puddle. I would have chosen the same way clamping on both ends of the machine also to save time. 5/32 rod at about 155-165 amps DC+ will lay it right in there with absolutely no concerns with edge wetting. Good rod for this purpose if only have an AC machine also, but the duty cycle will kick out if an inexpensive buzz box type. I've always used my Hobart engine drive welder which is DC only.
I like Lincoln 7018 Excalibur rod better myself and still use it quite a bit. Seems to be just as strong and much easier to control as it's an all position rod where 7024 is not.
|
Posted By: steve(ill)
Date Posted: 08 May 2022 at 9:23am
i have never welded up track shoes... But i use 7018 rod on DC exclusively for the past 40 years... Works great on everything.
------------- Like them all, but love the "B"s.
|
Posted By: Codger
Date Posted: 08 May 2022 at 9:55am
I never really knew what track chains were made from as far as carbon content but I used a lot of 9018, and 11018 rod to weld them up using stringer beads. McKay brand was the favored choice later absorbed by Hobart Bros. One stringer down the center of each link, then one on each side of the center bead, then one on the other side which would cover, or cap the link. I tended to use 5/32, or 3/16 diameter filler dependent upon link width and alternated side to side with the beads. Tracks were then sent to another party and punched apart. Uncle then would get them back and had a jig on his grinder and could do two links at a time profile grinding them back into shape. They then went back to that party for putting back together.
I never really seen them again unless a local job.
C1045 strip welded to track shoes and capped with either Stoody 31, or 35 hard facing wears pretty well in abrasive conditions which I would recommend the original poster does with his machine. The choice of 7024 rod and patience play handsomely together in this type work. 7024 in the horizontal position when joining dissimilar thickness baseplates in "tee" joint configuration is great as the edge wetting ensures penetration into the thicker material without burning through the thinner, (within reason).
|
Posted By: Daelric
Date Posted: 04 May 2023 at 8:18am
Codger wrote:
I have an 11B dozer myself and spent about an hour and a half exchanging emails with a gent in China via "Alibaba" who was very fluent in english and versed in undercarriage parts. Long and short of the story is a mated pin and bushing set was $49.00 each with a minimum of 100 each for my tractor. These I was told were quality steel hardened to 45C on the Rockwell scale which is the same as originals. I was assured they would serve as the originals did. Truth? I don't know of course as no direct experience. As mentioned in earlier postings the sprockets and chains are easily welded up for remachining to proper dimensions and these seem to hold up pretty fair if the correct filler material is used. Myself and now deceased uncle have done many in the past. It is the same with rollers, and idlers too. Most anything can be rebuilt, or built up and remachined true, but finding someone to do the work cost effective.....
There are still several H, and HD 3, 4 series out there needing new pins and bushings and if the participants would come together and share an order placement, great savings could be spread amongst the masses. Sad to say you'd be hard pressed to find an american machine shop to make p&b sets for the price.
|
After discovering that the bushings on my HD4 track are worn right through to the pin in some places, I am VERY interested in any info you have on this Alibaba/Chinese source.
|
Posted By: Codger
Date Posted: 04 May 2023 at 6:21pm
I have a lot of time, and some money vested in setting up the ability to order from China so going to be vague in my response(s). I will say a trial set is installed on an older HD-7 at my uncles place and the tractor currently has about 250 operating hours on the set. I'm told there is no noticeable wear to anything that was either built up, or replaced at this time and the dozer is used routinely. The P&B sets came from China. I had a friend make the master P&B sets. The "masters" were almost twice the cost of the China produced sets per each.
Price to end user? About $87.50 each after customs entry fees and taxes delivered to my shop on a P&B set matching specifications. There is a nine to 12 week turnaround to reception timeframe also with a 200pc minimum order. It would take a few people going in together as cost prohibitive for a single user.
It can be done albeit expensive. Keep in mind the cost of sublet repair labor also if you cannot do the work yourself. Even on a small crawler, it is a lot of work to replace the undercarriage; and many unknowns till broken into.
------------- That's All Folks!
|
Posted By: Codger
Date Posted: 05 May 2023 at 7:34am
Going to add to this just a bit. Once I have both this tractor, and another currently in testing evaluated fully, I will offer the service to rebuild tracks. I have a mobile Rogers track press with most any adapter set needed and can push any pins & bushings up to and including HD21 size tractors. My future plans are to travel and do some on site work in the warmer months in different parts of the country. Pricing will be "reasonable" for on site service.
I am working an angle to rebuild chains, rollers, idlers and sprockets but not complete on those yet. My uncle, (who we did this together) has passed on so I'm looking to replace his service(s). There are a couple of interested parties in negotiations currently.
Hopefully, in the near future this can all be brought to fruition and benefits can be had by those struggling to locate parts. I'm not really new at this kind of work so once acceptable sublet services are in place, it will be a go.
------------- That's All Folks!
|
Posted By: Codger
Date Posted: 08 May 2023 at 8:08am
Spoke with uncle yesterday and asked him to measure wear on the P&B's of the HD-7. There appears to be about .009" wear on the left track and about .0075" wear on the right track measured over four pins reference points I'd indented into the chains for trammel points install. This measurement is easily taken after the areas are cleaned and tracks tensioned properly.
There are 267 hours on the P&B's since install for reference. The dozer is not used hard but routinely to clean the feed lots. I don't know if the P&B's will wear faster once more clearances open from usage or not, but would expect so as foreign abrasive matter will inevitably find it's way in and exacerbate wear.
I've asked to be updated at 250 hour intervals to keep a log of the wear as it progresses. So far I'm quite impressed with what I've seen.
I do have the feeling that if a guy is willing to spend the money we can rebuild the tracks, or undercarriage and far extend the service life of the machine. Just because parts are obsolete doesn't mean the machine has to be put to scrap.
------------- That's All Folks!
|
Posted By: steve(ill)
Date Posted: 08 May 2023 at 9:17am
9 thousandths wear in 250 hours is GREAT !!.. Lots of tractors running with 1/8 inch wear or better... Have seen 1/4 inch on BIG tractors..... your 3000 hours from 1/8 inch wear !! 
------------- Like them all, but love the "B"s.
|
Posted By: Codger
Date Posted: 08 May 2023 at 9:31am
Yes, and thanks. I have not measured this myself but showed my relation how to use the trammel gauge I left for the purpose. My target was a 4K hours undercarriage wear rating on this size tractor which is a bit heavy for the home hobby machine.
I'm kind of hoping the service can sell itself in the near future as the pricing can come down a bit with more quantity ordered in the P&B's but will require pre orders to qualify. Ultimately this won't be limited to just A-C machines as one in test now is an IHC tractor.
------------- That's All Folks!
|
Posted By: Daelric
Date Posted: 08 May 2023 at 9:32am
That's great news Codger, thanks for doing all the work you've done towards this! I'll bet it hasn't been easy.
The only downside is that expense. I'm just assuming here, but I would imagine that there's no point in only replacing the odd P&B set. Correct me if I'm wrong, but shouldn't the entire track be replaced once it gets to the point that it can no longer be used due to wear through the bushings?
With this in mind, I counted it up and my tracks have 35 P&B sets per chain, for a total of 70 needed for 2 track chains. At your price quote that's $6125 USD I'm in Canada so that works out to $8200 CAD. Once shipping is factored in to get them to me we're into a price range where it's more than I paid for the machine to begin with!
I think at this point I'm just going to have to run the machine hoping that there are still some years left in those chains, because at this rate I don't see myself replacing the chains until they actually break on me.
|
Posted By: Codger
Date Posted: 08 May 2023 at 4:24pm
Undercarriage parts/costs have put many an otherwise serviceable tractor down over the years. Nothing new there and will continue to worsen as time marches on and parts are NLA.
You are correct in assumption there is no option to selectively replace P&B's as they must all be replaced together. Worn out P&B's such as you have does not mean the chain links are bad so these need measured up also. Drive sprockets at a minimum will require rebuild, or replacement as if they have been driving chains worn through the bushing they are extremely out of tolerance. If you put new parts against them the teeth will either break out, or at a minimum accelerated wear of your P&B's will occur. Sometimes doing a task correct is the only option IMO. Bushings worn through are a dead giveaway the tractor has had limited care and the cost will be great to rectify.
Part of what drives a price is a requirement or standards to be met. My specification of a 4K lifespan on a 15K tractor weight is a contributing factor for certain. I'm certain they would build P&B's that would only run 1K hours at reduced cost if that was the request and minimum quantities were satisfied for the order. That however is not a market I wish to participate within.
A chain doesn't usually break but rather won't stay on the machine. A few times reinstalling a thrown track usually changes a guys mind on the direction to take.
Thanks,
------------- That's All Folks!
|
Posted By: steve(ill)
Date Posted: 08 May 2023 at 4:34pm
you can not compare the original cost of the machine to what it takes to repair // replace a set of tracks.... I have bought several small farm tractors (allis B) for $500. or so... Might spend 2-3 X that much to get them running and repaired to last another 50 years..
You spend $10 K on a dozer and you might increased the value $15K.
------------- Like them all, but love the "B"s.
|
Posted By: Codger
Date Posted: 08 May 2023 at 9:10pm
Yes Steve, it is a common misconception the machine can be purchased cheap and repaired inexpensively to have the "Golden Goose" once done. However with crawlers few realize the amount of specialty tools and expertise required to do the most simple of tasks on the machine. So many variations of doing the same thing from type to type. Finding a shop these days that does track work is becoming increasingly difficult as much of the undercarriage anymore is a throwaway item once run out, and good used stocks thinning coupled with nothing available in the aftermarket or OEM levels. Many of the existing parts can be built up and machined true, but even that has limitations. It takes a special skill set to maintain aged construction equipment and most won't bear the expense of doing so; hence the reason a crawler sells for little dollars to potential value.
CTL's have mostly eliminated the small crawler in personal, and farm usage around here. Lot of versatility in a single machine. However those are pushing $75K for something with the capacity of a small metal tracked dozer, so the old crawler still has a viable purpose if used correctly. Couple the acquistion expense with the expense of repairs to their undercarriage, and it's quite a shock to many. Several around here have discovered the value in good tracks vs more inexpensive tracks in those too.
I'm only putting this out there to hopefully get people to thinking there are options available. I know where several crawlers are setting in different places unused because they won't keep a track on any longer. Staying with A-C one guy has an older HD-19, and two HD-21's that are mine for the hauling off if wanted but they all need extensive track work. The PS transmission in one of the 21's needs resealed but does work I'm told; the other has no history as was purchased for parts spares. A couple of IH tractors and certainly some Cat units. Caterpillar is the favored brand of many, but I'm from Springfield and loyal to the A-C brand in crawlers and wheel loaders. Got my feet wet many years ago, and it's been carried along the way through the years.
Once I get all the sublet labor established I plan to start purchasing up worn tracks for rebuild stocks. I'd like to offer tracks on a rebuilt exchange service eventually. This would lessen down time. Don't really have a clue of what will be desired but if the sublet shops are willing to work with me, I'll get it figured out.
I do plan to make attempt to have the P&B's machined in this country but that's not been possible from a cost perspective at this writing. As mentioned earlier, the master sets I had made meeting the criteria were almost double the cost of the chinese units. The search however will go on.
Thanks,
------------- That's All Folks!
|
Posted By: Mike K
Date Posted: 08 May 2023 at 9:45pm
Sprokets call J&H Welding Inc 906 353 6119 Mike is a nice guy to deal with
|
Posted By: Daelric
Date Posted: 09 May 2023 at 7:58am
To be fair, my intent with the comment about original cost to buy the machine wasn't meant to be a direct comparison to that cost... I am well aware that the cost to repair/refurbish machinery is very often more than the cost to buy the used piece of equipment to begin with. I also wasn't looking for any "Golden Goose" or bought the machine with inflated expectations. I live in a very isolated part of Canada where equipment is sparse and not easy to find, and this machine was literally the only tracked backhoe/loader I've ever seen come available up here in the past 20 years, so I took advantage of the opportunity.
Also, If my financial situation was better I would've bought a newer machine of some sort. The comment I made regarding cost was more a comment about my personal financial situation than anything else. While I wish I did, I simply do not have the finances to drop another $10k on this machine in the near future.
As for reinstalling a thrown track, this is definitely an issue I am facing It doesn't happen all the time, usually only when I'm having to make a tight turn using the brake along with the steering lever, but I've definitely had to put back on a thrown track probably about 5 or 6 times now in the 1.5 years I've owned the machine.
|
Posted By: Codger
Date Posted: 09 May 2023 at 1:22pm
Hi and thanks for responding; most don't. No insults or anything of the like meant by me as I'm just relaying it is possible to keep a machine operational with $$$ and the willingness to make it happen. Hard to find a good tracked backhoe these days as the combination hasn't been popular in many years. Hydraulic excavators long took that usage away. Kind of like toothed bucket trackloaders used to dig a lot of basements but not so much any longer.
I'm not trying to "drum up" business on this site at all. I will approach that when the time comes via a website and advertising aimed directly at that market. This is just the open and free flow exchange of information with track work being a single segment. I'm not any kind of close to going into production and am in the prototyping stage(s). It is a niche market I don't see anyone else chasing at this time but there is a lot of equipment that could be well served if someone took the lead. I hope it will take off, but who knows.....
------------- That's All Folks!
|
Posted By: Daelric
Date Posted: 11 May 2023 at 11:21am
Codger wrote:
it is possible to keep a machine operational with $$$ and the willingness to make it happen. |
The willingness is here 100%... unfortunately it's just the $$$ aspect for me in my current situation. If I didn't have an upcoming wedding and a major home renovation on the docket for the next year or two, it might be a different story!
Codger wrote:
Hard to find a good tracked backhoe these days as the combination hasn't been popular in many years. |
This is ultimately why I jumped at the chance to buy this machine when I did. You don't see equipment like this often. I live in an area in northwestern British Columbia on 80 acres with a lot of thick bush and trees, but the ground in a large amount of the acreage is soft and wet. This HD4 with its FEL and Backhoe attachment is the absolute PERFECT machine for the kind of work I need it for and the terrain I use it on. I absolutely love this machine, and feel like she's given me way more than my money's worth out of her in just the year and a half I've had her. If I had the cash to spare, I wouldn't think twice about putting my name down for a set of 70 pins and bushings. Hopefully in a couple years I'll be in a better position in that way.
Codger wrote:
I'm not trying to "drum up" business on this site at all. I will approach that when the time comes via a website and advertising aimed directly at that market.
|
Sounds great! Drum away! I hope when the time comes that I have the $$$ you've figured out all the kinks and are in full production... I'll certainly be keeping tabs on this forum to see your updates on that front! In closing, here are some photos of my machine. I think the sprockets appear to be in decent shape still, but that's just based on pics I've seen of other machines where the sprocket teeth look like they've been worn down to the point of looking like sharks teeth. 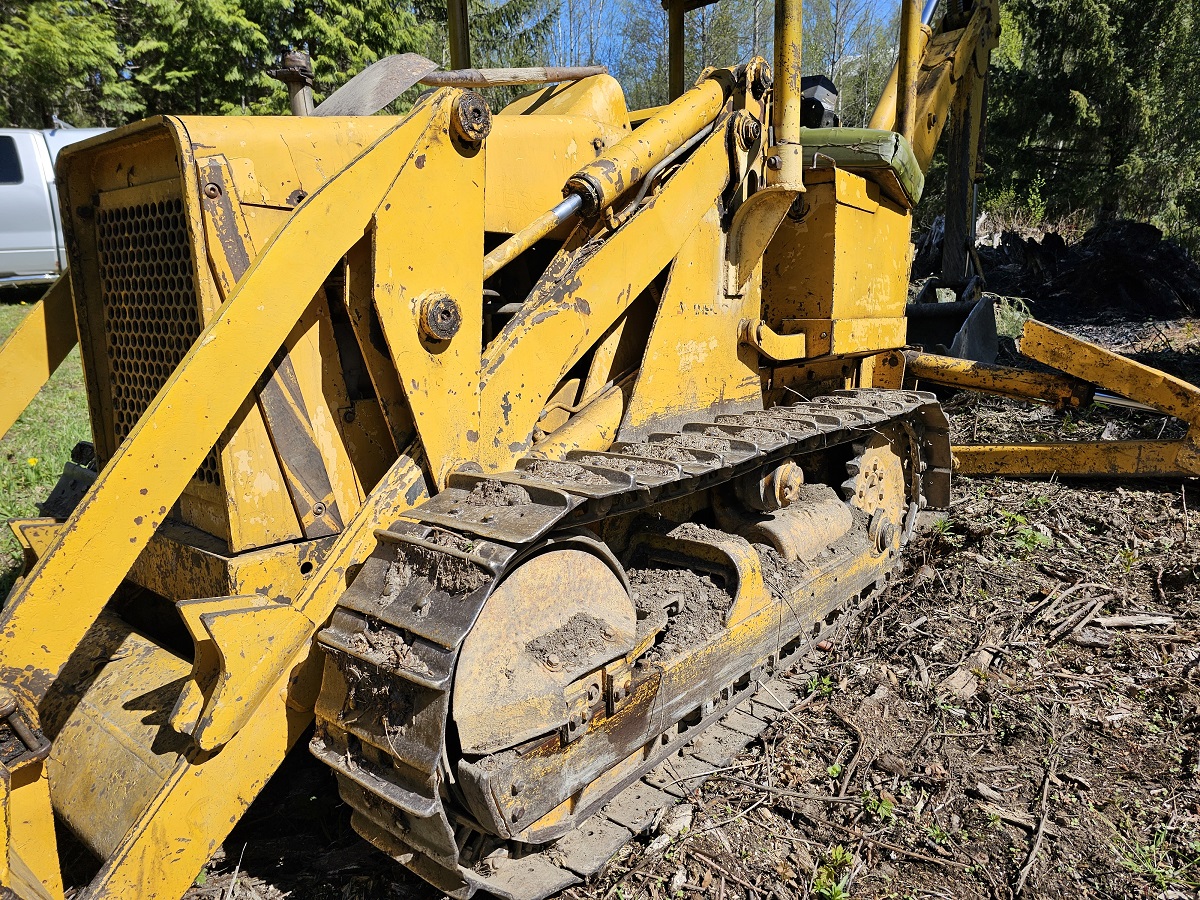 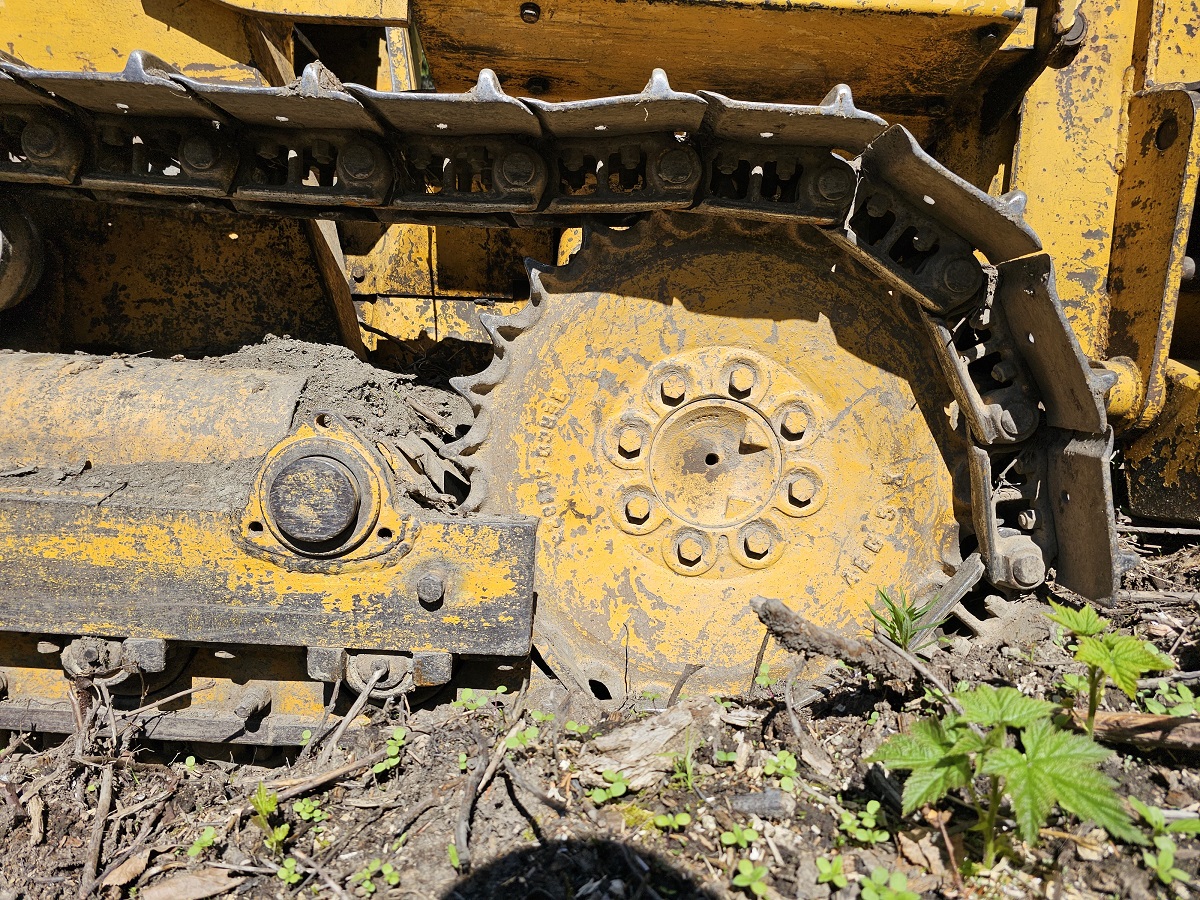
|
Posted By: Jgranat
Date Posted: 11 May 2023 at 5:13pm
Les Kerf wrote:
|
For the life of me I can't see how removing a track link can change the contact points on the sprocket, not saying it doesn't happen, I just can't see how? I understand the wear has changed things, but that has already been done and I look at it as the sprocket and links have wore together. Like removing a link from a motorcycle chain, it shortens it, but doesn't change its geometry? I know that's is over simplifying it. I'll look into flipping the bushings and pins, but I'm not sure that would be enough to remove enough slop for the tensioners to thread into the yokes properly. [/QUOTE]
Well, yes and no. Removing a link allows you to take all of the slack out of the chain; the chain has already 'stretched' due to wear, and if you pull it tight like a fiddle string then each link is now slightly longer, thus preventing the bushings from settling down into the sprocket.
The contact point is now higher up on the sprocket tooth and above the previous wear area. Since the same amount of force is now concentrated in a smaller area, this area will wear more rapidly than before, hastening its demise.
If the pins and bushings have never been turned, it will indeed help to have this done because the bushing area would then fill the sprocket more fully, plus the pin and bushing contact area is at a different spot inside. The chain will appear to be shorter.
If the pins and bushings have already been turned, then your options are now:
A) Run it as-is and hope the track stays on B) Find a better set of tracks (good luck with that!) C) Park it and use it for a yard ornament D) Scrap the machine E) Remove a link and get what little life remains out of your machine
If you do remove a link, run the tracks as loose as you can get away with
[/QUOTE]
A stretched track washes out your sprocket because it lengthens your pitch. Pitch has nothing to do with the number of links you are running.
|
Posted By: Codger
Date Posted: 11 May 2023 at 5:33pm
Thanks and always nice to see tractors in their natural beauty to which my wife swears is a beholder and eye type thing.....
Looks like a very versatile little machine and they certainly were handy in their day. They did better in sloppy dirt/mud than a rubber tired backhoe loader many times.
I do see a lot of wear in your undercarriage. The sprockets have probably been changed when the originals were "skipping" from the bushings wear, or wear through as they have been run that way quite some time. To me, the sprockets appear to be much newer than the balance of the undercarriage. I also see a lot of wear to the chain links and front idler in the photo. Much of this can be built up, or rebuilt, but the simple truth is a donor undercarriage is most beneficial and prudent citing the economics. There would be a lot of time with welding on those parts to get enough material placed to bring down to proper dimension.
I know a guy in southern Illinois that has a 655 in his yard minus an engine after the transmission went south. Last I knew it was still on it's tracks but that's been a couple of years now. I'll look this up in the next few days and relay you their information to talk if you like.
------------- That's All Folks!
|
Posted By: Jgranat
Date Posted: 11 May 2023 at 7:14pm
I'm wearing a helmet so throw stones if you must. Allis chalmers undercarriages were known for a shorter lifespan than most other construction equipment built back then. Rails, rollers, sprockets, and idlers are not made for them anymore. That said, if you can weld and make threaded holes, you could fit a suitable runnng gear on it to work it harder to recoup your costs. Or you can tighten the tracks up some, use it as it is, and enjoy it for the history it represents. It will not last as long as newer parts, but 20 hours a year won't kill it in 15 years if you are careful, and you will enjoy it.
My Grandfather had a couple Allis HD16B crawlers and he welded a lot every winter to keep them going. As much as I loved him and riding on those old dozers, my 1969 Cat D7E can still be updated with brand new UC parts , though costly, they are available. Messing with tracks in the mud is not my game anymore.
|
Posted By: DiyDave
Date Posted: 11 May 2023 at 8:33pm
Count the links on the tracks. someone mighta torched one off to tighten it up...
------------- Source: Babylon Bee. Sponsored by BRAWNDO, its got what you need!
|
Posted By: Codger
Date Posted: 11 May 2023 at 10:11pm
No need for any body, or head armor at all. No arguments, or fights to be had here. Most of what you stated in relation to parts availability is very true. Parts are NLA for Allis most of the time. Not everything is available easily for Caterpillar all of the time either. A lot still is however as the company is still in business. Where those replacement parts come from is anybody's guess. A part may be cast in India, and finished out someplace else, shipped by sea to a US port to be entered into Caterpillar's marketing arm. That's just what I've seen myself.
Never have heard someone say Caterpillar undercarriage wore, or lasted better than other's. That is just me saying as I've never heard that in the past. I'll ask the gent I purchased my track press from as both his he and dad, were involved in the undercarriage business over 40 years and they would know from a practical standpoint. I will reference both the D7E, and D7F models along with the HD-16, and HD-16B series as they would have competed for the same market share. Not looking to berate or anything, just a question I'd like an answer for.
Myself, I was mostly around IH undercarriage as doing an apprenticeship being just a few months in when the mines started shuttering and there simply weren't any jobs to be had for a young guy starting out in the field. Since then, well, you know the track business is about kaput with everything run to destruction these days. Except for the emergency type repair, track rebuild really doesn't exist as it used to.
This is where a guy like me comes in to make a part, or rebuild something that is worn out and NLA. As example, there is a guy around here that has an old Oliver crawler tractor and he made the chains that are on it. Of course they look different than the originals, but using pins and bushings from another tractor and finishing his links to meet the pins, it works well. Has rubber block pads so pulls a float on the streets during the town celebrations that go on here.
I have little actual experience and certainly am not an "operator". It does however start with an idea.
------------- That's All Folks!
|
Posted By: Mike K
Date Posted: 11 May 2023 at 10:17pm
I would contact J&H Welding Phone 906 353 6119 Mike will steer you in the correct direction
|
|