head gasket
Printed From: Unofficial Allis
Category: Other Topics
Forum Name: Pulling Forum
Forum Description: Forum dedicated to Tractor and Garden Pulling
URL: https://www.allischalmers.com/forum/forum_posts.asp?TID=111967
Printed Date: 05 Sep 2025 at 5:35pm Software Version: Web Wiz Forums 11.10 - http://www.webwizforums.com
Topic: head gasket
Posted By: autobody
Subject: head gasket
Date Posted: 14 Sep 2015 at 3:14pm
I have a gleaner motor with a 4 5/8 bore .Whoever built motor put sleeve below top of block. Blew head gasket pulling now cannot get to seal using copper gasket.Any tricks to get it to seal.
|
Replies:
Posted By: BennyLumpkin
Date Posted: 14 Sep 2015 at 3:42pm
Fix the sleeve height issue or you'll keep doing the same thing.
------------- Central PA Allis Express 1934 WC254 1945 WF 1945 WC135755 1951 WD68085 1953 WD45-150217 1957 WD45D-230744D B110
|
Posted By: mgburchard
Date Posted: 14 Sep 2015 at 6:54pm
If you think the sleeve has fallen another words only one sleeve is Lower than the other because they didn't turn enough step in the sleeve .you can knock it back up . use a right angle air drill and drill through sleeve into side of blocks bottom bore register and pin it . use small pins and make sure pins are below oil ring . hone sleeve and oring sleeve for copper gasket. Pankey fixes them like that all the time.
|
Posted By: CTuckerNWIL
Date Posted: 14 Sep 2015 at 7:07pm
Sounds like the block needs decked and C'bored. Might could get by with a cob job if just one sleeve is low, take it out and shim it up but cobbin might be a waste of time. Nothing like a clean proper C'bore with sleeves protruding as specs say.
------------- http://www.ae-ta.com" rel="nofollow - http://www.ae-ta.com Lena 1935 WC12xxx, Willie 1951 CA6xx Dad bought new, 1954WD45 PS, 1960 D17 NF
|
Posted By: mgburchard
Date Posted: 14 Sep 2015 at 7:10pm
I agree with Tucker but no ones 4 5/8 bore sleeve in a 226 block has a counter bore for a sleeve flange .
|
Posted By: autobody
Date Posted: 14 Sep 2015 at 7:12pm
All 4 sleeves are below the top of block
|
Posted By: mgburchard
Date Posted: 14 Sep 2015 at 7:17pm
Have block decked surficed ground . cut o-ring register in sleeves for .042 stainless wire with it protruding .022 to bite into copper gasket
|
Posted By: cms
Date Posted: 14 Sep 2015 at 7:39pm
4 5/8 sleeve can have and should have a counter bore flange on it. The problem with that bore with sleeves at the correct deck height is that the gasket still will blow because the gasket is thin and no strength left to hold. The block studs will pull out because of no block material left to hold, need to install studs differently. The inside of block needs to be machine out for more coolant flow. You can take head gasket out a run no head gasket, done it and yes it does work very well, do it on big bore engines. Call me you have my number if i can help.
|
Posted By: mgburchard
Date Posted: 14 Sep 2015 at 7:49pm
Don can cut sleeve for fire rings but adding the stud to torque the head enough to distort fire ring will push dons sleeves down . Pankey had one in shop like that he had to pin the sleeves to stop it
|
Posted By: wi50
Date Posted: 15 Sep 2015 at 8:28am
mgburchard wrote:
I agree with Tucker but no ones 4 5/8 bore sleeve in a 226 block has a counter bore for a sleeve flange . |
I do them with a flange.......
There isn't much to support the deck of the block on these engines. Basic physics here boys and girls, the seal is created between the sleeve and the head. Weather you have a gasket with a fire ring, a copper gasket and sleeves protruding from the block to create a pressure ring to seal, or a copper gasket with an O-ring in the sleeve or the head, a seal needs to form between the head and the sleeve
These blocks have an un-supported deck, meaning there isn't pillars running from the head bolts to the bottom web, or bores cast in the block to tie the top to the bottom. When you push on the sleeve with the pressure ring, it wants to push the sleeve down and lift the block deck up, there's a lot of leverage from the head bolts to the "pressure ring and it's going to try and distort the block and push the sleeve down. By machining a counterbore in the top of the block and a flange on the sleeve (just like original) you tie the block deck to the "pressure ring" and things stay put.
The easy way is to bore the block, leave a step in the bottom counterbore and push a sleeve in, this works on blocks that have support to the top deck, but we don't have that here. In order to get a large bore in, offsetting the original bores and boring there is little material in the bottom counterbore left, there isn't any strength there and there is a very small step. The sleeve gets pushed past the step. This type of design works fine in engines with supported decks, and enough material in the bottom web, however we are not dealing with that on these AC engines.
The way to do it right is to use a flange on top, and dowl pin the head.
------------- "see what happens when you have no practical experience doing something...... you end up playing with calculators and looking stupid on the internet"
|
Posted By: wi50
Date Posted: 15 Sep 2015 at 8:33am
I do have a set of ductile iron sleeves here from Power bore for these blocks. I also have a block done hanging on a stand. I'll have some time in the next couple days to take some pictures and put up of the sleeves and the finished product.
When I built my old WC engine for high RPM, I had welded the bottom of the sleeves to the bottom plate, and welded the top of the sleeves to the top deck. I tied the block together above the center main with tie bars and had made billet main caps and cross bolted a girdle to it. That block took a lot of abuse, took some doses of nitrous too.
------------- "see what happens when you have no practical experience doing something...... you end up playing with calculators and looking stupid on the internet"
|
Posted By: Butch(OH)
Date Posted: 15 Sep 2015 at 9:24am
As the guys have said, whom ever did the machine work screwed up but don't feel lonely, there are a lot of people out there screwing up sleeve jobs. I have a stack in front of my HBM to re-machine right now.
I have seen Pank's suggested "fix" on low pressure, low RPM engines such as hit miss when the machinist screwed up and cut the block too big for a press fit and didn't leave a stopping ledge either. I wouldn't trust that repair on a high performance application with known sleeve fit problems, if you get by with it great, if not more money down the tubes. As Marty said the clamping force generated by head bolts is tremendous, and you going to hold that back with a few small pins? Just put your thinking capon for a bit.
The fix is to re-machine the block and have new sleeves properly installed, that's my suggestion.
|
Posted By: mgburchard
Date Posted: 15 Sep 2015 at 5:38pm
Butch panks got sleeves in allis blocks turning 5000 rpms and 350 psi cylinder pressure just ask Brian Morrison .even sleeves with lips can be found below deck after being ran and having head removed . Sleeve material and block material sometimes expand and contract somewhat different . Seen sleeves .002 above be flush when pulled back apart seen sleeves that were machined flush .002 under deck after a season of hard running .
|
Posted By: autobody
Date Posted: 18 Sep 2015 at 9:43pm
Decide to junk block and build new motor.Thanks for replies to questions
|
Posted By: mgburchard
Date Posted: 20 Sep 2015 at 4:59pm
I'll give scrap price for the block you've decided to junk
|
Posted By: wi50
Date Posted: 20 Sep 2015 at 7:42pm
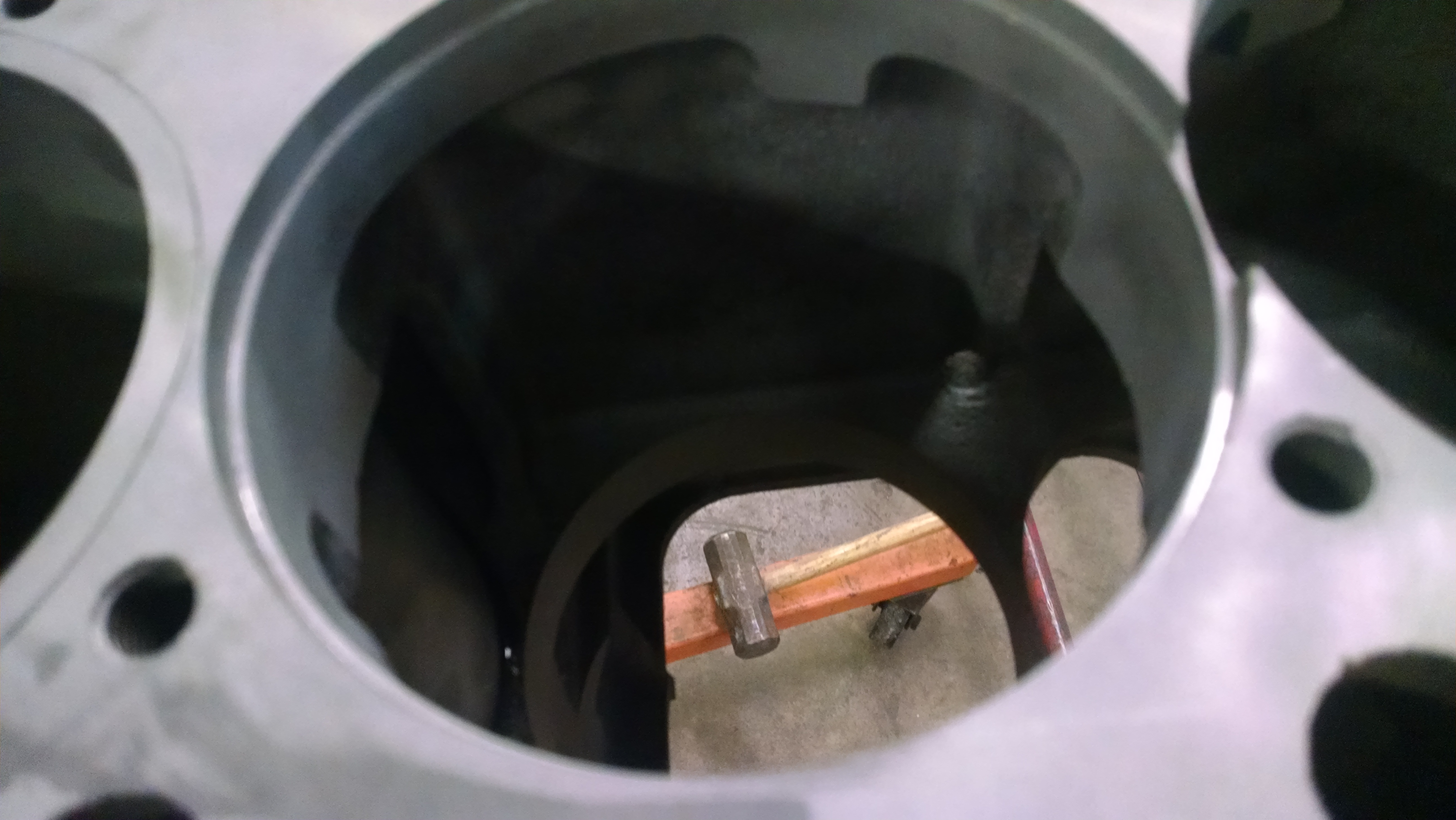
Here's a pic of how I do the flange. I offset the cylinders on the original bores, 1 and 4 go out or away from the center to each end of the block, 2 and 3 move some also. 1 and 2 along with 3 and 4 overlap some on the flange, but there is some room left from 2 to 3 in the center. All get moved away from the camshaft side of the block, then grind some clearance in the front, back and along the camshaft side to allow some coolant flow. There isn't really enough material left to run much of a press fit on the sleeves, so .0005" press fit is all. Much more press fit and it is going to split the block bottom at this point.
I make sure to take the edge off the bottom of the sleeve flange, so it has clearance to sit firmly on it's seat with out interfering with the slight radius left from the tool when boring the sleeve counterbore in the block. I also do just a slight undercut under the flange on the sleeve. If this isn't done, there is a chance that the sleeves could move a little bit
I blast the block clean on the inside, install sleeves with sleeve retainer around the bottoms. Then I use a product called Rock Block, it's a fiber based block filler. Grout based fillers will weep water, fiber will not, and it machines out easy and doesn't wreck tooling if the need ever arises in the future.
After install, they get bored, honed and block gets decked, then I cut O ring grooves in the sleeve.
This particular block in the picture is a #40 so it's solid above the center main for a 201 engine. It's set at 4.6" bore with room left to bore to 4.7" a time or two should it get worn or scored.
------------- "see what happens when you have no practical experience doing something...... you end up playing with calculators and looking stupid on the internet"
|
Posted By: wi50
Date Posted: 20 Sep 2015 at 8:09pm
The sleeve I spec out has 5 different diameters on it.
Flange, .100" larger, just say 5.000"
top counter bore 4.900" barrel, I just make it .010" smaller than the top counter bore so it slides through for easy install, 4.890"
bottom counter bore, press fit to the block 4.800"
and the bottom of the sleeve, .010" smaller than that of the bottom counter bore diameter to allow the sleeve to 4.790"
Internal bore is 4.5" and rough to allow boring to desired size after install.
So you have a 4.890" sleeve barrel with a 4.6" bore, leaves you with .145 wall thickness, or if you wanted to bore to 4.7" you wind up .095" which is on the thin side.
I have a set of ductile iron sleeves here made by power bore if you need them. Though I'll have to check the dimensions it may be .050" larger on all dimensions than what I posted above.
------------- "see what happens when you have no practical experience doing something...... you end up playing with calculators and looking stupid on the internet"
|
Posted By: mgburchard
Date Posted: 23 Sep 2015 at 6:02pm
Pank bores the top 4.950 turns the sleeve two inches up from bottom in lathe to 4.800 lets sleeve set on block bottom bore with Bing with .oo2 interference on 4 5/8 bore sleeves . On 4 3/4 bore sleeves be bores 4.950 installs straight sleeve and pins in bottom on 4.800 piston bore he bores 5.060 and pins straight sleeve in bottom . he fills the block and doesn't run water .he fixes alot of the run water blocks by hard blocking and opening up cylinder bore making cylinder block more rigid for more hp
|
Posted By: bradley6874
Date Posted: 23 Sep 2015 at 6:43pm
mg pank was kicked of the site because he could not back up what he kept saying he does and arguing with everybody now you keep braging about all he does and how great you think he is most of us don't want to here about him so please take this hint if you cant do it YOURSELF don't tell us what pank can do thanks and have a great quiet day
------------- You can wash the dirt off the body but you can’t wash the farmer out of the heart and soul
|
|