WD45 D alternator rebuild
Printed From: Unofficial Allis
Category: Allis Chalmers
Forum Name: Farm Equipment
Forum Description: everything about Allis-Chalmers farm equipment
URL: https://www.allischalmers.com/forum/forum_posts.asp?TID=110547
Printed Date: 21 Aug 2025 at 9:02am Software Version: Web Wiz Forums 11.10 - http://www.webwizforums.com
Topic: WD45 D alternator rebuild
Posted By: banjerpicker
Subject: WD45 D alternator rebuild
Date Posted: 17 Aug 2015 at 8:24am
The battery on my WD45 diesel isn't charging. Can anyone help me figure out what's going wrong+ It has a single wire alternator on it.
Thank you!
|
Replies:
Posted By: Gerald J.
Date Posted: 17 Aug 2015 at 9:11am
Alternator wasn't original. Single wire needs to be spun fast to start charging. Once it starts it will charge at low speed. There might not be enough engine speed possible if it has the original generator large diameter pulley. Good auto electric shops can supply a smaller diameter pulley to get it spun fast enough to start charging. On my gas 4020 the small pulley takes about 1650 engine RPM to start charging and that's with a 5 or 6" crankshaft pulley.
Most 1 wire alternators charge without spinning fast with an added wire from the gas ignition switch through a lamp, resistor, or diode. On a diesel a convenient technique is with an oil pressure switch that closes on pressure rise, available from NAPA. Requires a T at the oil pressure sensor.
Gerald J.
|
Posted By: DougS
Date Posted: 17 Aug 2015 at 9:11am
Pure and simply it's probably the alternator, unless your ammeter is defective. Measure the voltage at the alternator output while the engine is running around 1000 RPM. If you don't have 13.5 to 14.5 volts, you need to have your alternator serviced. If the voltage is correct, check your ammeter.
|
Posted By: banjerpicker
Date Posted: 17 Aug 2015 at 11:12am
I don't have a tach and had to guess on the rpm. Put a multimeter on it and didn't get any change no matter the rpm. Would it be best to do a conversion from single to 3 wire alternator?
|
Posted By: DougS
Date Posted: 17 Aug 2015 at 1:19pm
I would prefer to install a 3-wire alternator. You can pick one up at a junkyard for much less than a rebuilt. It does not have to be a large alternator. The smaller alternators still put out more than the old 1950s generators. You might have a problem figuring our how to wire it. Do you understand what Gerald is saying when he mentions installing an oil pressure switch?
|
Posted By: banjerpicker
Date Posted: 17 Aug 2015 at 1:22pm
Not really. Never done much electrical work. About what size do I need?
|
Posted By: banjerpicker
Date Posted: 21 Aug 2015 at 10:31am
While on the topic, I've heard of rigging a tachometer to the alternator. Is this possible?
|
Posted By: BennyLumpkin
Date Posted: 21 Aug 2015 at 12:10pm
Not on a diesel. You need the impulse from the ignition to run an electronic tach
------------- Central PA Allis Express 1934 WC254 1945 WF 1945 WC135755 1951 WD68085 1953 WD45-150217 1957 WD45D-230744D B110
|
Posted By: banjerpicker
Date Posted: 21 Aug 2015 at 12:13pm
Is there a way to rig a tach on a diesel? The reason I'm asking is, this is a former pull tractor that seems to run at a higher rpm, and I don't want to blow an implement by running it too fast.
|
Posted By: Leesok
Date Posted: 21 Aug 2015 at 6:33pm
Have a 210 and a 175D that the tach is driven from the alt. Would take some rigging but is possible. http://s590.photobucket.com/user/leeok/media/Mobile%20Uploads/image_3.jpg.html" rel="nofollow">
|
Posted By: TramwayGuy
Date Posted: 21 Aug 2015 at 7:22pm
Some alternators have a terminal that can drive a tach. Similar to the ignition style. Would have to be calibrated.
|
Posted By: Gerald J.
Date Posted: 21 Aug 2015 at 7:37pm
Some Perkins engines connect a mechanical tach to the cam shaft end. I looked at a MF-135 set up that way today and the tach pointer rotation is opposite from my NF-135 with a Continental engine where the tach drive is by a rotation reversing and speed changing gear box on the back of the generator. My 4020 uses a gear drive under the distributor.
Modern pickup diesel engines use crankshaft or cam shaft position sensors to indicate speed.
A classic electric tachometer uses a permanent magnet generator. Its decently precise that the voltage from the armature is exactly proportional to the generator's shaft speed.
An alternator generates alternating current and rectifies it (usually internally, but vintage Leece-Neville alternators used external rectifiers). Some tapped the AC for a tachometer because the frequency of the AC is exactly proportional to the alternator shaft speed. The frequency is predicted by counting the rotor poles. Two rotor poles passing one field pole makes one cycle of AC, so a 16 pole alternator rotor makes 8 cycles of AC per revolution. Frequency is not hard to read with many PIC chips having a built in counter and they can drive a display. I'm sure something like that is in use on many a modern tractor and semi.
Then there are optical tachometers that shine a light on a shaft with a bit of reflective tape on the shaft that light hits and display the shaft speed directly on the display.
Then there are mechanical tachometers that are nothing more than a high ratio work gear drive from the input shaft to a dial pointer. Time the dial pointer revolutions or count them for a minute, multiply by the gear ratio. Not handy when the end of the shaft isn't handy and its working hard. There are also mechanical tachometers that drive from the end of a shaft usually with a rubber button and move the pointer to show the shaft speed.
A shaft position sensor can put out pulses usable by an ignition triggered electronic tachometer too, but may need amplification to have enough voltage.
And there are sensors specifically made for shaft speed, a lot like the speedometer sensor in my '98 F150.
Gerald J.
|
Posted By: eighty nine
Date Posted: 21 Aug 2015 at 7:40pm
Probably be best to check rpm at pto shaft with a hand tach & set engine speed to spec. I am sure someone on here could tell you the proper shaft speed for the correct high idle setting . And you could mark the throttle quadrant at 540 rpm also . .
|
Posted By: Steve in NJ
Date Posted: 22 Aug 2015 at 9:13am
Most one wire Alternators need 1200-1400 rpm in order for them to excite the regulator to start charging. I wouldn't recommend a one wire Alternator for a Tractor. Most one wire Alternators though can be changed to a three wire by simply wiring in the VR. Pop the plug out of the top of the one wire and plug in the three wire pigtail. We offer the conversion in a kit to change your one wire to a three wire. To read more about the conversion and learn a little about the system, drop by our website. I have some good information and articles on our site. Steve@B&B bb-customcircuits.com
------------- 39'RC, 43'WC, 48'B, 49'G, 50'WF, 65 Big 10, 67'B-110, 75'716H, 2-620's, & a Motorhead wife
|
Posted By: banjerpicker
Date Posted: 22 Aug 2015 at 12:04pm
Thank you! What I might do, of I can't get this one to work, is get one for another AC that has the tach drive on it. If it does work, I'll do a conversion to 3 wire and fudge the tach somehow.
|
Posted By: banjerpicker
Date Posted: 24 Aug 2015 at 7:54pm
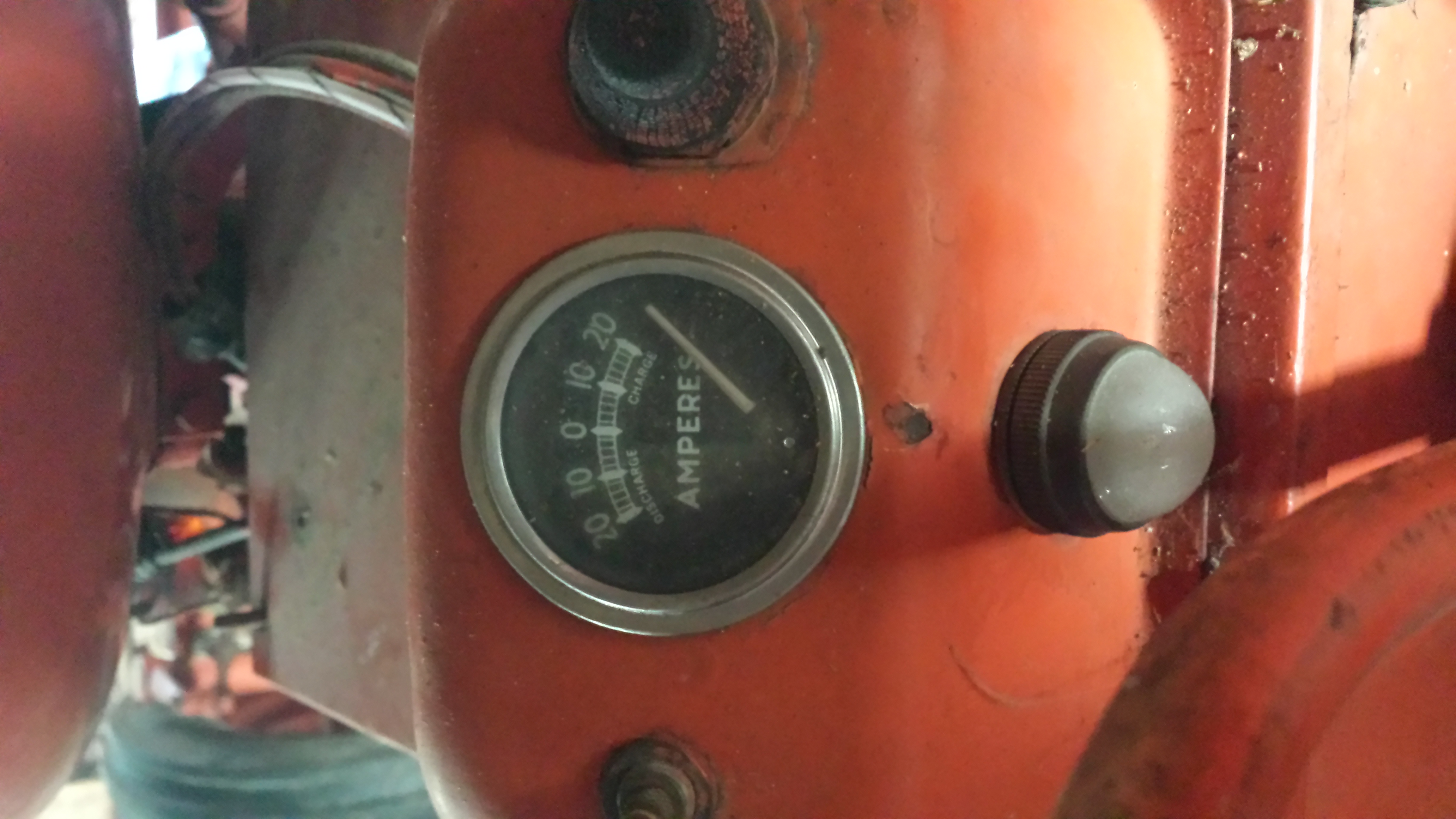
Got it too full throttle, and the needle went crazy. Looks like the alternator is good.
|
Posted By: DougS
Date Posted: 24 Aug 2015 at 8:34pm
That's why you want a larger ammeter when you install an alternator. You may want to consider something as large as a 60-0-60.
|
Posted By: WF owner
Date Posted: 24 Aug 2015 at 8:42pm
I had a 7000 with an electrical tach that ran off the alternator. It might be easier than running a cable.
|
Posted By: banjerpicker
Date Posted: 24 Aug 2015 at 8:50pm
So it is possible.
Now that I know this one works, I can do a 3 wire conversion and focus on reinstalling the hydraulics, including traction boost and adding a 3 point hitch.
|
|