Best way to repair stripped out 7/8" threads
Printed From: Unofficial Allis
Category: Other Topics
Forum Name: Shops, Barns, Varmints, and Trucks
Forum Description: anything you want to talk about except politics
URL: https://www.allischalmers.com/forum/forum_posts.asp?TID=174132
Printed Date: 22 Jun 2024 at 10:14pm Software Version: Web Wiz Forums 11.10 - http://www.webwizforums.com
Topic: Best way to repair stripped out 7/8" threads
Posted By: CaseyCreek
Subject: Best way to repair stripped out 7/8" threads
Date Posted: 05 Sep 2020 at 9:01pm
(Details. The actual question is at the bottom.)
I didn't start this problem, but I have to admit that I finished the damage. I bought a Ford 7700 and I have used it for about five years. Great tractor, even if it isn't orange. The problem is that one of the bolts which hold in the sway blocks pulled out and took the threads with it. There is no way to just screw the bolt back in to the original hole.
The bolt is 7/8"-9 x 3" and it goes up in to the chassis of the tractor. I don't have a picture of the bolt location, but in the video I am posting, the bolt is just behind the play button on the link. On my tractor, the bolts attach to chains which prevent the lift arms from swinging around. One of the bolts is still attached and giving no problems.
[TUBE]dY9oXtih_5g[/TUBE]
(The question)
Basically, what is the pilot hole size for the next size up from a 7/8"-9 thread? Should I punt on this one and let a local machine shop do the work?
------------- D17 Series III,D17 Series IV, 185
|
Replies:
Posted By: steve(ill)
Date Posted: 05 Sep 2020 at 9:27pm
One common fix is to use a thread insert repair kit... I have done a couple on the B final drive case that you mount the draw bar loop to.
You drill out the hole to ( lets say) 1-1/8 inch and thread it.... then you LOCITITE a threaded sleeve into the hole that is 1-1/8 OD and 7/8 inch ID... Back to original size...
another way is to rethread the 7/8 hole to 1 inch and use a NEW bolt.
------------- Like them all, but love the "B"s.
|
Posted By: steve(ill)
Date Posted: 05 Sep 2020 at 9:29pm
this is one version.....
https://www.amazon.com/V-Coil-8-inch-UNC-Thread-Repair/dp/B00EO4NULO" rel="nofollow - https://www.amazon.com/V-Coil-8-inch-UNC-Thread-Repair/dp/B00EO4NULO
------------- Like them all, but love the "B"s.
|
Posted By: CaseyCreek
Date Posted: 05 Sep 2020 at 9:44pm
I had looked up a helicoil repair kit and it was going to set me back over $200. For that much money, I thought I could probably take it to a local machine shop. We are lucky enough to have a good one a few miles away.
I looked at the repair kit you posted with the link from amazon. At $95, the price is now getting within range of trying it myself. Thanks.
As to drilling out a 3" deep hole to 1" in solid metal with a hand-held drill, I don't trust myself to do that yet. If I could pull that off, the end product would probably be stronger than new, though.
------------- D17 Series III,D17 Series IV, 185
|
Posted By: Tracy Martin TN
Date Posted: 05 Sep 2020 at 10:22pm
Casey, Helicoil is the route to go. I don't know which bolt hole it is. Can it be drilled using a magnetic base drill? I have done hundreds of them of various sizes and locations. Post a pic of hole and its location. Thanks Tracy
------------- No greater gift than healthy grandkids!
|
Posted By: shameless dude
Date Posted: 05 Sep 2020 at 10:28pm
get sum dog chain and a short tarp strap, wrap it around the lower lift arms, when hooking up something the tarp strap will stretch enough to hook up. have used this on most all my tractors for years.
|
Posted By: jaybmiller
Date Posted: 06 Sep 2020 at 6:33am
hmm... does this bolt hole go INTO the casting far ? drilling it ,might go too far , and oopsy... you found gold, black gold, Texas tea ????? I KNOW what happens to D14 rockshaft PTO cover holes if bolts are too long....
maybe you could just weld/braze a nut onto the casting? It seems there wouldn't be a lot of stress on it( sway chain ) ??
just trying to think of options not seeing it in person.
Jay
------------- 3 D-14s,A-C forklift, B-112 Kubota BX23S lil' TOOT( The Other Orange Tractor)
Never burn your bridges, unless you can walk on water
|
Posted By: Jim.ME
Date Posted: 06 Sep 2020 at 6:54am
7/8" is the tap drill for 1"-8 NC thread. 59/64" tap drill for 1"-12 NF.
Here is a Starrett chart.
uploads/16335/tap_chart.pdf" rel="nofollow - uploads/16335/tap_chart.pdf
|
Posted By: DougG
Date Posted: 06 Sep 2020 at 7:18am
If that metal is as easy as drilling on an Allis it will be a breese, seems it's low grade stuff, I'd be careful not to go to deep as Jay mentioned but I think back there it's out of the oil housing
|
Posted By: DrAllis
Date Posted: 06 Sep 2020 at 7:57am
There are several thread repairs of different designs available to do this good. Trouble is, most of them need a lot of meat around the hole to work. Drill the hole oversize and install a one inch bolt and Loctite it.
|
Posted By: desertjoe
Date Posted: 06 Sep 2020 at 8:24am
Hey Jim.ME,,,I made me a copy of your link to post above my lathe,,,, THANKS,,!!!  
|
Posted By: steve(ill)
Date Posted: 06 Sep 2020 at 8:37am
If your 7/8 bolt is stripped out , your not too far from the root diameter of a 1 inch NC bolt.. Use a small drill with very little horse power.. Get a drill bit turned down on the end to fit the smaller drill ( 3/8 inch)... Just go slow and round out the hole.. Your only taking out 1/16 of an inch or so.... Why 3 inches deep? A 1 inch bolt only needs to go in 1-1/4 inch to get strength.
------------- Like them all, but love the "B"s.
|
Posted By: steve(ill)
Date Posted: 06 Sep 2020 at 8:40am
you could even take a 1 inch stud and turn the outside part back to 7/8 NC and thread it... Screw the 1 inch stud in 1-1/2 inch with loctite, and let the 7/8 end outside be the original size.
------------- Like them all, but love the "B"s.
|
Posted By: CaseyCreek
Date Posted: 06 Sep 2020 at 9:21am
steve(ill) wrote:
Your only taking out 1/16 of an inch or so.... Why 3 inches deep? A 1 inch bolt only needs to go in 1-1/4 inch to get strength. |
The three inches is the current depth of the bolt hole. I was just duplicating the factory measurements. I really do appreciate the help on this, btw. I have rethreaded stuff for years, but this one is outside of my experience.
------------- D17 Series III,D17 Series IV, 185
|
Posted By: thendrix
Date Posted: 06 Sep 2020 at 12:45pm
Easy way to figure trap drill size is OD - thread pitch. For example, 1"-8 the has a .125 (1/8") thread pitch. You figure this by 1" divided by 8 thread which equals .125. 1 minus .125 equals .875 or 7/8. Works the same for metric but metric threads give you the pitch without having to divided 1 by the threads per inch.
------------- "Farming is a business that makes a Las Vegas craps table look like a regular paycheck" Ronald Reagan
|
Posted By: jaybmiller
Date Posted: 06 Sep 2020 at 3:50pm
yeesh, 3" deep thread hole !! If it's ONLY used for the sway chain, maybe fill with JBWeld ,then drill and tap. I just can't see a sway chain needing 3" x 7/8" bolt to secure it. Maybe I'm missing something ??
------------- 3 D-14s,A-C forklift, B-112 Kubota BX23S lil' TOOT( The Other Orange Tractor)
Never burn your bridges, unless you can walk on water
|
Posted By: DiyDave
Date Posted: 06 Sep 2020 at 7:09pm
jaybmiller wrote:
yeesh, 3" deep thread hole !! If it's ONLY used for the sway chain, maybe fill with JBWeld ,then drill and tap. I just can't see a sway chain needing 3" x 7/8" bolt to secure it. Maybe I'm missing something ??
|
Don't matter how big the bolt is, there is always the loose nut behind the wheel, that can break an anvil with a feather... 
You've already got a 7/8" hole drilled, 3" deep. Just take the right sized bit, for the thread you want to make, and hand drill it, with an old slow speed 1/2" drill, and the proper sized bit for the bolt or heli-coil you are putting in. Most taps have the size of the drill you need, printed right on the side. With a Heli-coil, the bit is usually included in the kit! If you get it a degree or 2 off true, it aint that critical, to make any kind of difference, anyway!  
------------- Source: Babylon Bee. Sponsored by BRAWNDO, its got what you need!
|
Posted By: steve(ill)
Date Posted: 06 Sep 2020 at 9:11pm
im starting to wonder if you could take a 7/8 stud and smear JB weld all over one end and screw / pound it into the hole and let it dry..... If the load is not that great, the stud sticking out should be able to anchor the chain with no problem... i think epoxy or JB weld should hold that load.
------------- Like them all, but love the "B"s.
|
Posted By: Fred in Pa
Date Posted: 07 Sep 2020 at 6:35am
I would never even think of JB Weld for a repair like this .Fix it right.
------------- He who dies with the most toys is, nonetheless ,still dead. If all else fails ,Read all that is PRINTED.
|
Posted By: Sugarmaker
Date Posted: 07 Sep 2020 at 7:03am
my two cents also, I would carefully drill the damaged hole out with a hand held drill to the 1 inch coarse thread size. You will need a stepped down bit for that. You local shop may have the tooling. Going the full 3 inches deep to clean up. Hand tap the 1 inch thread. Drill the mating component clearance hole out to 1 1/16 inch, Get a good Grade 5 bolt to replace the 7/8 fastener that broke pulled out the thread. For some reason this threaded connection failed? was it over loaded or was it loose and wore out from use? Good luck with your repair. That is a good tractor, Having this repaired will allow you to sleep better too!  Regards, Chris
------------- D17 1958 (NFE), WD45 1954 (NFE), WD 1952 (NFE), WD 1950 (WFE), Allis F-40 forklift, Allis CA, Allis D14, Ford Jubilee, Many IH Cub Cadets, 32 Ford Dump, 65 Comet.
|
Posted By: Clay
Date Posted: 07 Sep 2020 at 8:26am
One of the best heli-coil type inserts are the ones sold by CAT.
|
Posted By: ocharry
Date Posted: 07 Sep 2020 at 9:21am
hi Casey,,,hey im pretty sure i have a 7/8 drill with a 1/2 shank,,,that is the tap drill for a 1" bolt,,,,and i am also pretty sure i have a 1"-8 tap ,,,
so if i do,,, i could send them to you to use,,,,and when you are finished you could send them back to me,,,,i probably also have a fine thread set too,,,but i need to look and see,,,,pretty sure i do have the 1"-8 tap and i know i have a short 7/8 with a 1/2" shank drill
reason i mentioned fine thread it will be easier to turn and make threads in the hole,,,,a 1" tap will need a big wrench
that hole is already to size mostly,,,just needs cleaned up and made some kind of round again,,,then put a tap in there and threads will be back but next size up
and old trick is to use good old crisko (showing my age here,,,lol),,for lube on the tap,,,,but if you have or can find some stuff called tap-ezz it works good too,,,im sure there are other specialty tapping lubes out there too
just me trying to help out some
ocharry
|
Posted By: chaskaduo
Date Posted: 07 Sep 2020 at 11:04am
You're a mighty fine man Oil Can. 
------------- 1938 B, 79 Dynamark 11/36 6spd, 95 Weed-Eater 16hp, 2010 Bolens 14hp
|
Posted By: CaseyCreek
Date Posted: 07 Sep 2020 at 3:53pm
ocharry wrote:
hi Casey,,,hey im pretty sure i have a 7/8 drill with a 1/2 shank,,,that is the tap drill for a 1" bolt,,,,and i am also pretty sure i have a 1"-8 tap ,,,
so if i do,,, i could send them to you to use,,,,and when you are finished you could send them back to me,,,,i probably also have a fine thread set too,,,but i need to look and see,,,,pretty sure i do have the 1"-8 tap and i know i have a short 7/8 with a 1/2" shank drill
reason i mentioned fine thread it will be easier to turn and make threads in the hole,,,,a 1" tap will need a big wrench
that hole is already to size mostly,,,just needs cleaned up and made some kind of round again,,,then put a tap in there and threads will be back but next size up |
I can't thank you enough for the offer, but I have a decent set of drills and a tap and die set. I just haven't ever worked anything this big before where I couldn't put it what I am working with on a bench.
I think I am going to try and drill the hole out for a 1" bolt instead of using a heli coil.
------------- D17 Series III,D17 Series IV, 185
|
Posted By: DougG
Date Posted: 07 Sep 2020 at 3:54pm
That JB Weld fix comment was way out there- gotta wonder what thoughts are elsewhere
|
Posted By: Tbone95
Date Posted: 07 Sep 2020 at 4:59pm
I somewhat support Steve’s jb weld suggestion, though I would use ....I can’t remember the number...it’s a green loctite industrial adhesive. We use it at work to bond a workpiece to an arbor for hi precision high torque specialized machining processes. You can snap the steel driver off before that stuff breaks loose in the hole / arbor.
If it should happen to fail, the option to fix it with a drill and tap is still there.
|
Posted By: steve(ill)
Date Posted: 07 Sep 2020 at 5:24pm
i posted the JB weld comment to get some discussion and more input... I do not know the EXACT purpose of that bolt, but i though he said it was to hold the side movement plate and chain.. I dont know why the bolt would be 7/8 inch diameter. Maybe the load is greater than i think....
Look at it this way... The hole is now about 1 inch diameter.. or about 3 inch circumference.. He said the hole is 3 inches deep... Lets assume we shove the stud in 2 inches... 2 inches x 3 inches is 6 SQUARE INCHES of surface area between the stud and the hole bore... if the Epoxy or JB weld has a SHEER strength of 2000 psi, then 2000 x 6 is 12,000 POUNDS that the stud could hold before the epoxy RIPPED out..
Is there 12,000 pounds of load on that bolt ? I though maybe NO.. but again, why is the bolt 7/8 inch diameter ? My "guess" would be that a 5/8 inch bolt would be enough to hold the chain and block ? What did i miss ?
------------- Like them all, but love the "B"s.
|
Posted By: steve(ill)
Date Posted: 07 Sep 2020 at 5:26pm
I have used high strength epoxy to glue 1/2 inch studs into concrete holes drilled 4 inches deep.... if you put a puller on that stud and pull, you will bust a chunk of concrete 6 inches in diameter out ( a couple TONS load), before the epoxy will let go.
------------- Like them all, but love the "B"s.
|
Posted By: DiyDave
Date Posted: 07 Sep 2020 at 5:38pm
Common problem, with all bolts that point up, is that they tend to loosen, from side loading. Now you have a chain attached to it, connected to the lower 3 point arms, you get a swing, an impact, and viola, the bolt starts loosening. In any case, I'd put lock-tite on it, no matter what/how you replace it. A perfect example of this movement is AC's D-series factory 3 point hitches, which install with 3 up-threading bolts, they loosen, then shear the bolt(s) off, if not watched...
Remember, also, don't turn with a rigidly mounted implement, in the down position... 
------------- Source: Babylon Bee. Sponsored by BRAWNDO, its got what you need!
|
Posted By: tadams(OH)
Date Posted: 08 Sep 2020 at 2:15pm
Was the bolt 3" long that went in it ? If the hole is 3" deep and the bolt was there is probably good threads still in there that if a guy ran a tap in and cleaned up you could put a longer bolt in and not have to redrill.
|
Posted By: Ken(MI)
Date Posted: 08 Sep 2020 at 6:02pm
Couple things here, if that bolt is a grade 8, it needs minimum of 1 1/2 to 2 times the diameter of full thread engagement in cast iron for it to realize it's full potential, the factory didn't drill the hole that deep for enjoyment. No epoxy will hold that sway chain load, think of a 500 lb. brush hog swinging on the end of the arms, even a couple inches of travel and it's a 500 lb. hammer swinging on the end of the arms. There are several options for an effective repair as mentioned above, threaded inserts, Heli-Coil inserts, or drilling and tapping oversize. One other point to consider is that fine threads are stronger than coarse threads and fine thread taps twist in a whole lot easier. As mentioned above, to keep the hole straight and centered, I would grind a drill with a pilot at least an inch long, go as deep as possible and finish with a non piloted drill to full depth, and probably do the same with the tap at least to get it started, but I have a machine shop and a cutter grinder to make short work of the tools required, not to discourage you, but this could go bad fast if you're not entirely sure of your abilities and could run into bigger money to get it right if you make a Boo Boo. I wish you the best of luck with your decision and the repair, that 7700 is a fine tractor, even if it is blue.
|
Posted By: Tbone95
Date Posted: 08 Sep 2020 at 7:40pm
I’m not familiar with that specific tractor, I admit. However, I don’t think I can think of a tractor where the chain keeps something from swinging out too far. The ones I’ve seen, when hitched to a brush hog or plow or whatever, the lift arms are sucked in and keep from swaying by the insides of the arms coming into contact with the rear end housing and usually a plate of some sort. The chains limit movement when free and unhitched.
|
Posted By: CaseyCreek
Date Posted: 08 Sep 2020 at 8:02pm
tadams(OH) wrote:
Was the bolt 3" long that went in it ? If the hole is 3" deep and the bolt was there is probably good threads still in there that if a guy ran a tap in and cleaned up you could put a longer bolt in and not have to redrill. |
Been there, done that. When I bought the tractor in 2015, someone had already put the current bolts in. My belief is that they had been slipping out before I bought the tractor. I kept torquing the bolts down (no Loctite, I'm going to fix that this time) and they kept loosening up. This time when they loosened up there wasn't anything left to grab on to.
What I haven't made clear enough is that these bolts take a beating. I use this on a loader tractor. I keep an 1,100 lb stump grinder on the back to keep by back wheels on the ground. Oh, and I work on hillsides. What ends up happening is that the stump grinder is always working back and forth.
The picture is of the last treetop that I cleared this season. I have been clearing trees of this field for almost ten years. I still have about three to go. There are over 3,000 stump holes that I periodically drive over in this field. It pays to go slowly. The whole field is terraced so I am constantly swinging everything back and forth.
Probably a lot more detail than you wanted, but I am sure that a lot of people are wondering why I couldn't have just done what you suggested. I really appreciate the help offered on this forum. I was completely out of my element on this one.
------------- D17 Series III,D17 Series IV, 185
|
Posted By: steve(ill)
Date Posted: 08 Sep 2020 at 8:36pm
and NOW FOR THE REST OF THE STORY.... that explains a lot.. NICE TRACTOR.. drilling it round and retap to 1 inch seems like your easiest, best bet... 
------------- Like them all, but love the "B"s.
|
Posted By: CaseyCreek
Date Posted: 08 Sep 2020 at 8:38pm
Tbone95 wrote:
However, I don’t think I can think of a tractor where the chain keeps something from swinging out too far. The ones I’ve seen, when hitched to a brush hog or plow or whatever, the lift arms are sucked in and keep from swaying by the insides of the arms coming into contact with the rear end housing and usually a plate of some sort. The chains limit movement when free and unhitched.
|
Tbone, on an Allis, I would have sway blocks. Here is the way Ford did it.
So, my drill size is 7/8" and I only have one (cobalt). If I understand what I have been reading, I need to get a cheaper drill and reduce the size of the to fit inside the hole, then make a pilot hole before drilling the hole which will hold the threads? To do fine threads, I need a 59/64 drill?
------------- D17 Series III,D17 Series IV, 185
|
Posted By: Jim.ME
Date Posted: 08 Sep 2020 at 9:17pm
Yes, a 59/64 bit is required for 1"-12 NF threads.
If the fine threads would be stronger in the cast housing I would think the manufacturer would have used fine. Coarse is usually found in cast materials from what I've seen.
If the bolts were 7/8"-9 NC originally I would use 1"-8 NC. Clean, degrease, and use the primer for the thread locker on the threads (tapped holes and the capscrews) after tapping. Use red thread locker.
I believe Ken (MI) was suggesting grinding about 1 inch of the end of the drill smaller in diameter to act as a pilot in your existing stripped out hole.
|
Posted By: Ken(MI)
Date Posted: 09 Sep 2020 at 6:54am
I forgot an important item, when drilling and tapping cast iron, ALWAYS machine it dry, any kind of lubricant will do nothing but cause it to work harden and you won't be drilling it with any tool known to mankind, especially using hand tools. Cast iron is full of free carbon also known as graphite, so it has it's own built in lubricant. As for the debate on fine versus course threads, fine threads are always stronger, but not always practical, especially in a production setting, a 1" hole isn't that hard to hand tap, but a fine thread tap is much easier to twist in, I think either course or fine would be suitable for your application, properly torqued with lubricant, loc-tite shouldn't be required, but if you choose to go that way stay away from the red stuff, blue or green with everything clean and using the proper primer, they aren't going anywhere.
|
Posted By: Tbone95
Date Posted: 09 Sep 2020 at 7:11am
CaseyCreek wrote:
Tbone95 wrote:
However, I don’t think I can think of a tractor where the chain keeps something from swinging out too far. The ones I’ve seen, when hitched to a brush hog or plow or whatever, the lift arms are sucked in and keep from swaying by the insides of the arms coming into contact with the rear end housing and usually a plate of some sort. The chains limit movement when free and unhitched.
|
Tbone, on an Allis, I would have sway blocks. Here is the way Ford did it.
So, my drill size is 7/8" and I only have one (cobalt). If I understand what I have been reading, I need to get a cheaper drill and reduce the size of the to fit inside the hole, then make a pilot hole before drilling the hole which will hold the threads? To do fine threads, I need a 59/64 drill?
| On an Allis, on a Deere, on the Massey I had, on the Ford 6000 I had....but I digress! Between this and your post about what you've been up to, yeah, whole bunch to the rest of the story!
So these bolts bolt that plate the chains are attached to HORIZONTALLY into the rear end just under the PTO? And the lift arms don't ever come into contact near the drawbar side mounts?
Interesting. But yeah, drill and tap for 1 inch UNC. Good luck. I don't see why you would need a pilot on the end of the drill. With the bolt hole already there, the drill is going to follow that unless you try really hard to screw it up.
|
Posted By: Tbone95
Date Posted: 09 Sep 2020 at 7:14am
I remember our Massey, it had brace bars that attached farther out the axle to limit sway for certain jobs. Just kind of odd that it would rely on jerking a chain like that.....but it is what it is.
|
Posted By: Jim.ME
Date Posted: 09 Sep 2020 at 7:50am
You are right Ken, I may have been a bit aggressive saying use red thread locker, the blue will be fine.
Another point about cast iron to go with Ken's point on no cutting oil needed for drilling. When doing work on old Allis Chalmers Hydro Turbines, Voith (holds the rights to most of them now) said not to use anti-seize or other lube on fasteners threaded into cast iron for the same reason, the carbon/graphite in it provides its own lubricant. Thread lockers do provide some lubrication so don't over torque.
You know this but you only have check chains to stop the arms from hitting the tires. The sway/ stabilizer set up Tbone95 mentioned was an option, there were no blocks on the sides of the case for the arms to hit limiting sway.
|
Posted By: Tbone95
Date Posted: 09 Sep 2020 at 8:02am
I would be looking into what Jim just posted. Makes a whole lot more sense than jerking a chain bolted into your cast rear end with all that weight and momentum!
|
Posted By: ocharry
Date Posted: 09 Sep 2020 at 10:34am
you know i was sitting here reading this,,,and i mentioned earlier to use crisko or tap-ezz or other specialty tapping solutions,,,,,
but Ken and Jim brought up a good point about this being cast iron,,,,duuuuuhhh,,,never even thought about it being cast iron,,,,(was thinking cast steel)but if it is,,,skip all the stuff i said about using a lube,,,,you wont need it
and it will tap WAY easier than steel,,,,not that it will be easy,,,,but a tap will cut easier in the cast iron,,,and if it is,, it is more than likely a good cast
also,, if it is cast iron,,, thats probably why the hole is 3" deep,,,cast isnt as strong as steel so it needs a little more purchase ,,,hence more thread contact
also Ken's idea about a piloted drill is a good idea,,,it will help keep the drill from jumping around,,,kinda like the drill in a hole saw,,,,ever try using a hole saw without the drill to keep it centered
anyway,,,,go slow and careful and you can do it
ocharry
|
Posted By: CaseyCreek
Date Posted: 27 Sep 2020 at 5:04pm
Given the amount of help I received on this topic, I wanted to post some pictures of how things turned out. I went ahead and tapped both holes to 1" (7/8" drill bit) so that they would match. Then, I used blue Loctite when I put the bolts back in. I had a local machine shop drill out the holes in the steel plate to 1 1/16". The twenty dollars they charged was less than the cost of a new drill bit of that size. I thought things turned out pretty well.
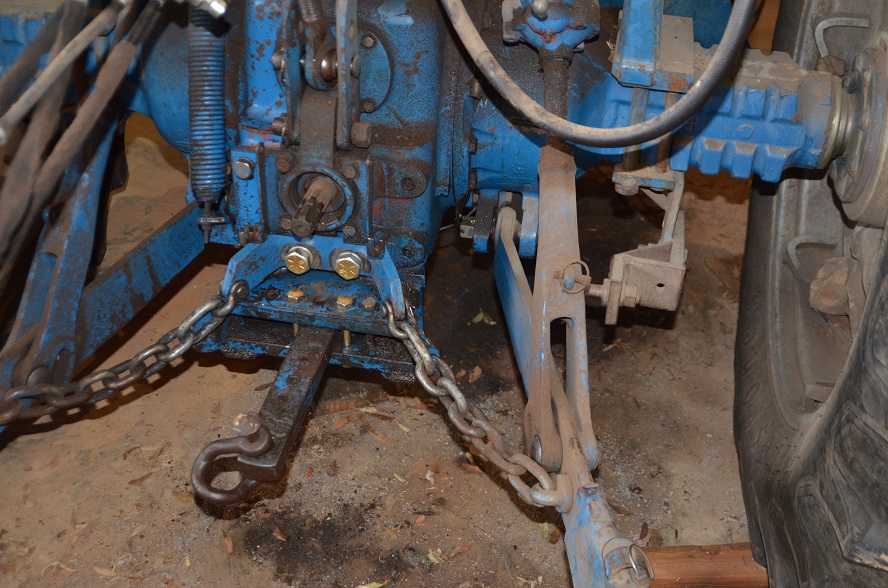
This was actually working well, but I kept thinking about the parts diagram from Jim.ME which seemed to show a stabilizer. So, I started looking online for one of those. What I found out surprised me quite a bit. The Ford 7710 which replaced the 7700 used a very slick adjustable part on the outside of the lift arms. Even better, the 7700 was fully drilled and ready for the system on the 7710. So, I ordered two of those stabilizers and wound up with the situation you see below. I had to order knock-offs because I couldn't find any original Ford parts in the salvage yards I contacted. That being said, it works really well and I don't worry about the bolts getting pulled out again.
------------- D17 Series III,D17 Series IV, 185
|
Posted By: DougG
Date Posted: 27 Sep 2020 at 5:31pm
Good job , thanks for the final pics
|
Posted By: DMiller
Date Posted: 27 Sep 2020 at 5:47pm
Posted By: Tbone95
Date Posted: 28 Sep 2020 at 6:57am
There you go! Yeah, that makes a WHOLE LOT more sense. Good luck in your future endeavors.
|
Posted By: Ken(MI)
Date Posted: 28 Sep 2020 at 7:54am
Posted By: Ted J
Date Posted: 28 Sep 2020 at 2:44pm
------------- "Allis-Express" 19?? WC / 1941 C / 1952 CA / 1956 WD45 / 1957 WD45 / 1958 D-17
|
|