An Auction for the Rest of Us.
Printed From: Unofficial Allis
Category: Allis Chalmers
Forum Name: Construction and other equipment
Forum Description: everything else with orange (or yellow) paint
URL: https://www.allischalmers.com/forum/forum_posts.asp?TID=144296
Printed Date: 18 Jul 2025 at 3:24pm Software Version: Web Wiz Forums 11.10 - http://www.webwizforums.com
Topic: An Auction for the Rest of Us.
Posted By: Garlic Pete
Subject: An Auction for the Rest of Us.
Date Posted: 09 Nov 2017 at 10:20am
Garlic Mom, Ray, Billy and I went to an auction near Merced on Saturday. Garlic Mom and I went to Billy's Friday afternoon. We brought him a present of a Fifteen parts tractor that WyoCat was nice enough to arrange for us. Billy had a Fifteen parts tractor which used to sit in front of his house connected to a tumblebug. A guy stopped by regularly and asked him to sell it. One day he had a weak moment and had been regretting it ever since. Now he has a Fifteen to complement his tumblebug again. Billy and Annette were kind enough to host us for dinner and let us stay in their guest house. Billy's house is about two hours north of us, and the auction was about an hour from his house. Here's Billy's truck in its house. http://postimg.org/image/8j5ki1t79/" rel="nofollow"> Saturday morning we woke up early and unloaded the Fifteen and put it where it belonged. We went to Firebaugh for breakfast at the Giant Burger, which is the local duck bill club. There we met several of Billy's friends, including one who has mules and showed us lots of neat pictures and videos of the mules, interesting tractors and other stuff. After a good breakfast, we headed north to find the auction. Our original plan was to bring three trucks, ours, Billy's and Joe's, along with our 966. It turned out Joe had other commitments and Billy's truck turned up with the shifter air lines eaten by mice, so we were down to one truck and the 966. That was O. K. though. When we got to the auction, there was even more, better stuff than the flyer had advertised. In addition to the Allis Chalmers Wheel Dozer and neat Allis Chalmers HD-16A we were interested in, there was another bareback Allis HD-16A, about the most pristine Adams pull grader I've seen. The big one with ten foot wide axles, two neat military Jeeps and quite a few Cats. Many of our Cat friends were there, so we didn't figure to get any of the Cats, but we did strike on a few good things. Here's a really neat 100 year old flat belt pump with pipe which we got for a couple hundred. This'll go in Daron's front yard. http://postimg.org/image/jp4gwqsr9/" rel="nofollow"> http://postimg.org/image/7kp7frfv9/" rel="nofollow"> http://postimg.org/image/hylfv9b85/" rel="nofollow"> http://postimg.org/image/ag2ammjv9/" rel="nofollow"> Here's the Allis Chalmers HD-16A we got for $850.00. It hadn't run in over ten years. It has a Detroit 6-71 for power. It also has a really neat Garwood blade with Garwood front cable control and Garwood double drum rear cable control. We added water and removed the valve cover to check for stuck injector. Pulling the engine through a revolution revealed three stuck injectors. I was able to pry them up and down a few times and get them loosened up. I pulled it through a couple more revolutions and they were still a little stiff, but the rack stayed free. Ray pushed me with the 966 and in about a revolution or so it was running just fine. Everything works, including the front cable control drum and both rear drums, all steering clutches and brakes and the master clutch. We tried the starter with two good batteries, but it didn't want to spin the engine over. We were just using jumper cables though and the old batteries were still connected, so sucking current too. I think if we got two good batteries and wired them up correctly, it'll start as it should. http://postimg.org/image/iuhxapkwl/" rel="nofollow"> http://postimg.org/image/3ztbwjbbp/" rel="nofollow"> http://postimg.org/image/t0qitp5at/" rel="nofollow"> http://postimg.org/image/a4pfnlst1/" rel="nofollow"> Here's an absolutely spectacular big Twenty which Skinner bought. I think he got a steal. http://postimg.org/image/srxjhihw5/" rel="nofollow"> http://postimg.org/image/4pgpmn191/" rel="nofollow"> http://postimg.org/image/fxuwaff2t/" rel="nofollow"> Here's a really nice, straight Wooldridge which we got for $450.00. The tires all hold air and it looks really good. http://postimg.org/image/c7zuv9slx/" rel="nofollow"> http://postimg.org/image/ak0pgmeqd/" rel="nofollow"> Here's a really nice ripper which we let go to a friend, who kindly backed off on bidding on some of the stuff we wanted. I think he gave $500.00 for it. http://postimg.org/image/3xe1nfx1x/" rel="nofollow"> And here's a nifty little Allis Chalmers wheel dozer. I believe it is a D-30 model. It has the Allis Chalmers six cylinder turbo diesel which was originally a Buda design, before they were purchased by Allis. We got this for $550.00. http://postimg.org/image/ay21g7ytx/" rel="nofollow"> http://postimg.org/image/5nx2oxel1/" rel="nofollow"> http://postimg.org/image/bq9at5set/" rel="nofollow"> We were a little worried about the right front tire. The lock ring was pushed back about six inches off the o-ring and the tire was pretty cracked. The other three tires took air and appeared to hold well. We lifted the trunnion and set it on a big block, then ran a chain around the right front tire. We jerked on the chain with the 966 to try to pull the lock ring back out. At first, no dice. We tried pushing the ring in a bit with a fork tip and got the ring to move. Some nice people gave us a can of P. B. Blaster which we used liberally. With it all lubed up, we started jerking the chain again. It took lots of jerks and creative repositioning of the chain, but eventually we got the ring back up to the o-ring and started pumping in air. It took a bunch more jerks and repositioning of the chain, but we finally got the air inflow to overcome the leaks and the ring seated, o-ring sealed and the tire held fifty pounds of air. http://postimg.org/image/8ah6jlv6d/" rel="nofollow"> http://postimg.org/image/43wc49vkl/" rel="nofollow"> http://postimg.org/image/ne3cnphjp/" rel="nofollow"> Saturday after the auction, Skinner needed some help hauling a nice Twenty Eight parts tractor to his place, so Garlic Mom and Billy followed him with our pickup and car trailer while Ray and I worked on the HD-16A. When they got back, we had it loaded up and were ready to take it to Billy's house. That was all we could get done that day, so we spent Saturday night at Billy's and returned Sunday morning, after another nice Giant Burger breakfast. Sunday morning, after fixing the wheel dozer tires, we were going to try to start it, but we discovered the fuel filters and canisters had disappeared. This engine has a Roosamaster pump and the filter base is a remote affair bolted to the block. It has provision for two canisters with what looked like six lines coming from it. My theory is that, even though it is mounted canister down, it is similar to the International scheme, where one canister is a prefilter from the fuel tank, then the lines go to the lift pump, then back to the second filter for a fine filtration, then back to the pump for injection. If I'm right, Billy has a spare set of those from his International MD, so I may be able to adapt something to work. Since we couldn't start it, we towed it around and got it lined up with the trailer. This has that fully hydraulic steering, where the steering wheel is connected to a rotor and lines go to the steering cylinders, no mechanical connection. That worked out good because we could just bump the wheels to steer where we needed. We got it all loaded up, chained down and hauled over to Billy's. We fired up the HD-16A to unload. Here's s short video. https://www.youtube.com/watch?v=cnkwNAXlDV4&feature=youtu.be" rel="nofollow - https://www.youtube.com/watch?v=cnkwNAXlDV4&feature=youtu.be and some photos. http://postimg.org/image/ghdroxamt/" rel="nofollow"> http://postimg.org/image/cso2pg0lx/" rel="nofollow"> http://postimg.org/image/ljqi5yuj9/" rel="nofollow"> Here's Billy and granddaughter McKenna, who were supervising. http://postimg.org/image/4ppwe4g0l/" rel="nofollow"> While at the auction, we helped several people load stuff, including the buddy who bought the ripper and he also bought a really neat Galion grader with a UD-18 engine. Neat to have a full hydraulic grader with twin stacks from that era. This looks like something King of Obsolete needs. http://postimg.org/image/m4a4med5h/" rel="nofollow"> http://postimg.org/image/s2nxwmw45/" rel="nofollow"> http://postimg.org/image/q6wk7qhw5/" rel="nofollow"> It was a fun day, lots of good friends and made some new ones and got some neat equipment pretty easy on the wallet. It'll be fun to get it home, adjusted, greased up and repaired, ready to play. Pete. Garlic Mom and I returned and loaded the Wooldridge, dumping the truck with it still on at Billy's and beat it for home. We were home by about 9:30 pm.
|
Replies:
Posted By: Garlic Pete
Date Posted: 09 Nov 2017 at 10:21am
New Here. I'm new here, but I have posted over on the Caterpillar bulletin board for a while. Someone over there told me about this forum and I thought you all might be interested in our latest acquisitions, and maybe could help us as we learn about them. Pete.
|
Posted By: CAL(KS)
Date Posted: 09 Nov 2017 at 10:35am
Welcome and thanks for posting! Awesome buys.
------------- Me -C,U,UC,WC,WD45,190XT,TL-12,145T,HD6G,HD16,HD20
Dad- WD, D17D, D19D, RT100A, 7020, 7080,7580, 2-8550's, 2-S77, HD15
|
Posted By: Ferdinand
Date Posted: 09 Nov 2017 at 10:38am
Here's the Allis Chalmers HD-16A we got for $850.00.  ............................Ray pushed me with the 966 and in about a revolution or so it was
running just fine.
Maybe one day, i"ll find something like that.
Really like the Peterbilt. Is it a 351?
------------- Because narrow is the gate, and narrow is the way, which leads unto life, and few there be that find it. Mathew 7:14
|
Posted By: jerbob
Date Posted: 09 Nov 2017 at 11:25am
Welcome to the group. Great acquisitions. Good job.
|
Posted By: orangeman
Date Posted: 09 Nov 2017 at 4:06pm
Garlic Pete: I hope the ACMOC boys don't rib you too bad for collecting the AC's.
All the best - nice job on saving these machines.
Orangeman
|
Posted By: dustydoo
Date Posted: 09 Nov 2017 at 6:36pm
Welcome to the boards ! Great purchases , wish you best of luck with them all !
|
Posted By: Tracy Martin TN
Date Posted: 09 Nov 2017 at 10:37pm
That is my kind of day!
------------- No greater gift than healthy grandkids!
|
Posted By: JC-WI
Date Posted: 09 Nov 2017 at 11:06pm
Garlic Pete, as far as I know, the HD16 crawlers all had AC engines in them... unless somegody transplanted one from an HD15... and I wish it had been in my neck of the woods... 850 bucks PFFFFTT!!! no body sells them hunks of irons that cheap here nor in that good of condition. wouldn't have minded the LeTournue scrapper either.
------------- He who says there is no evil has already deceived himself The truth is the truth, sugar coated or not. Trawler II says, "Remember that."
|
Posted By: Steve allis dozer
Date Posted: 09 Nov 2017 at 11:59pm
Hey Garlic Pete I like the D30 wheel dozer , it will have the allis 11000 series engine and the fuel pump is an American Bosch (AMBAC) you are correct with the fuel filters and the way they are set up there is a large one and smaller one , they have a steel outer housing that is held in with a centre bolt I would be surprised if they weren't laying around near the machine or in the shed i f you could find them all you would need is the paper cartridge inner element .Regards steve
|
Posted By: shameless dude
Date Posted: 10 Nov 2017 at 2:31am
welcome to the forum, and thank you for posting the story and pics! you will find a lot of good info in here from a lot of great people!
|
Posted By: Garlic Pete
Date Posted: 13 Nov 2017 at 1:58pm
Thank you all. Ferdinand - I'm not sure of the model, but the Peterbilt is a 1963. I believe it might be a 351. It has been converted to single axle, but was originally tandem drive. JC(WI) - As you'll see below, you are correct on the tractor model. Steve allis dozer - Thank you for the information on the engine model number and filter arrangement. I think I have a lead on the person who bought a pallet of parts, which probably had these canisters and bolts on it. If not, I'd appreciate any guidance anyone might be able to provide about getting canisters and bolts for an 110000 filter housing. I wasn't able to make the trip to another Member's this weekend because of some family health issues with Garlic Sweetie's Dad. Those are under control now, so Garlic Mom and I, joined by Daniel, Colby and the two dogs, piled into the pickup and headed up to Billy's Sunday afternoon to retrieve one of our treasures. Billy had pizza, hot links and potato and macaroni salad ready for us when we got there. After a nice lunch, we got down to business. We drained some of the water and added antifreeze to the HD-15, started it up and ran it to circulate stuff. Ray from Madera came over to pick up Garlic Mom's John Deere crank inventory. We transferred the cranks out of the back of the pickup and into Ray's trailer. Ray stayed around to help us out loading. He even donated some of his WD-40 to lubricate my binders. He said something about being smart enough not to fight with a piece of steel which was probably smarter than me. I was able to check the serial number. It is, in fact, an HD-15AC, as pictured: http://postimg.org/image/4w50wtsid/" rel="nofollow"> http://postimg.org/image/k2b2nrij9/" rel="nofollow"> Daniel and Colby had a good time running the HD-15 and the 966. We pushed the wheel dozer up onto the Cozad with a minimum of drama and got it tied down. http://postimg.org/image/w1r68tdhx/" rel="nofollow"> http://postimg.org/image/42sf47mhh/" rel="nofollow"> http://postimg.org/image/wm67bi6qd/" rel="nofollow"> http://postimg.org/image/8tsam8fbp/" rel="nofollow"> http://postimg.org/image/rc18k7mhh/" rel="nofollow"> http://postimg.org/image/gwqgxjzx1/" rel="nofollow"> I thought the wheel dozer looked pretty frog like sitting there on the truck. http://postimg.org/image/e95m0xw9h/" rel="nofollow"> http://postimg.org/image/n5ge4vmvp/" rel="nofollow"> In the first picture, you can see Garlic Mom at the edge on the left, then Ray, Colby, Daniel and Billy. I can't remember the big dog's name, but the little dog is called "Little Dog". She likes to ride, so any chance she sees an open door, she zips into the car and hides her face in the corner of the passenger seat floorboard, thinking she's invisible. I'll need some parts for the engine of the wheel dozer. The fuel filter elements and canisters are missing. It is an Allis Chalmers 11000 engine, originally a Buda design. I believe one canister is larger than the other. The filter base is a remote affair so I could adapt different bases and filters to do the job, if necessary. I'll get more detailed pictures and post them in the next couple of days. Pete.
|
Posted By: DiyDave
Date Posted: 13 Nov 2017 at 5:36pm
Ida thought the dog's name shoulda been garlic dog, er maybe clovus, hee hee hee!!
|
Posted By: JohnCO
Date Posted: 14 Nov 2017 at 2:02am
Maybe Big Dog?
------------- "If at first you don't succeed, get a bigger hammer" Allis Express participant
|
Posted By: Garlic Pete
Date Posted: 11 Dec 2017 at 9:06am
We had a little play day over the weekend. There is a bit of off topic in here. Didn't really do any digging, but did repair a few things, start and run several things and had a really good time. Daron and Marianne came over from California City and Joe came from Buttonwillow. Daron helped me figure out I had the Allis Chalmers batteries hooked up backwards, should be positive ground. After fixing that, and a bit of manual adjustment (bending a voltage regulator points spring attach point) he had the generator generating. The last piece I need to fix on it is the Hobbs mechanical hour meter. I got it apart last night and need to figure out if it has an electrical problem or a mechanical clock movement problem. Tom and his Brother Doug came down from Tehachapi in his immaculate 1959 GMC Cannonball. https://postimg.org/image/on1h84zo5/" rel="nofollow"> https://postimg.org/image/l4phbqys5/" rel="nofollow"> He has put the axles from a 2001 Peterbilt under it, so it rides nice with the Peterbilt air leaf suspension. He also just finished overhauling the 6-71 to solve a heating problem. The Detroit injectors fit into a copper sleeve which can develop pinholes and let combustion gasses into the cooling system. It is an absolutely spectacular truck. Tom was kind enough to take me for a ride and let me drive it a bit. It is better than new! Steering is tight, everything works, it is just beautiful. Garlic Mom wanted to get her Allis Chalmers UC going, so we aired up the tires, added some gas and got it running. Joe took it for a spin, then Garlic Mom took her turn. https://postimg.org/image/h4ibzi8b9/" rel="nofollow"> https://postimg.org/image/wol4cat1x/" rel="nofollow"> https://postimg.org/image/vg1u4eqhh/" rel="nofollow"> https://postimg.org/image/x40zj24d1/" rel="nofollow"> Here's some video of Joe riding around. https://www.youtube.com/watch?v=T2v5oc0WU8I" rel="nofollow - https://www.youtube.com/watch?v=T2v5oc0WU8I https://postimg.org/image/hxqcedoyd/" rel="nofollow"> Joe spent some time on the RD-7. https://postimg.org/image/6dq4035at/" rel="nofollow"> https://youtu.be/_yWE2rbvl8U" rel="nofollow - https://youtu.be/_yWE2rbvl8U Tom also got some seat time on the RD-7, but we were too busy having fun to shoot the video! We started the sawmill turbo D7 17A. I hadn't been able to test the steering brake repair I did, but it seems to work, steers in both directions now! I still need to swap out the rusted through transmission filter tower and get some new cable so that the blade will work. No pictures or video of that, though. Too busy trying to start, operate and evaluate. After lunch, Tom and Doug took the Allis Chalmers HD-15AC and Wooldridge for a spin. Video courtesy of Tom's (Rileydog362) YouTube channel. https://www.youtube.com/watch?v=pBH6XLapxRg" rel="nofollow - https://www.youtube.com/watch?v=pBH6XLapxRg We had a really nice time. Pete.
|
Posted By: Garlic Pete
Date Posted: 11 Dec 2017 at 9:08am
Old School Contracting. Garlic Mom had such a good time at the play day Saturday, she didn't want the fun to end. Sunday, she said we needed to do some Old School Contracting, so we got out the 1963 Peterbilt, hooked it to the Cozad and loaded up the HD-15AC and Wooldridge for some fun. https://postimg.org/image/ybexb9uhh/" rel="nofollow"> https://postimg.org/image/cewzon6ol/" rel="nofollow"> https://postimg.org/image/8h54lhuhh/" rel="nofollow"> https://postimg.org/image/k8xla1ehh/" rel="nofollow"> https://postimg.org/image/ka7j3ggb9/" rel="nofollow"> https://postimg.org/image/55bf5xs45/" rel="nofollow"> https://postimg.org/image/jlyokihlh/" rel="nofollow"> https://postimg.org/image/i871p7ic5/" rel="nofollow"> https://postimg.org/image/m0lyr78gl/" rel="nofollow"> https://postimg.org/image/85no8qe1h/" rel="nofollow"> https://postimg.org/image/sacn0gihh/" rel="nofollow"> https://postimg.org/image/hm8w1m8id/" rel="nofollow"> https://postimg.org/image/lstqgy845/" rel="nofollow"> [url=https://postimg.org/image/qns0syvth/] https://s26.postimg.org/eyo1504ux/20171210_123444.jpg" rel="nofollow - [/url - https://s26.postimg.org/eyo1504ux/20171210_123444.jpg[/img][/url ] Here's a video with some taking off, some driving by, a few sessions of poorly executed twin stick shifting and the unload at the end. https://www.youtube.com/watch?v=jHjNlK2qle4" rel="nofollow - https://www.youtube.com/watch?v=jHjNlK2qle4 Anybody need a hole dug? Pete.
|
Posted By: Garlic Pete
Date Posted: 11 Dec 2017 at 9:12am
Help With 11000 Fuel Filter Canisters and Filters. I got a few pictures of the fuel filter base and engine details of the 11000 engine in the wheel dozer. Can anyone suggest where I could get the missing canisters, bolts and other internal parts. Also could use help with filter element part numbers. I didn't get a readable picture of the engine serial number. I'll try to get that next time I'm out there and post here. https://postimg.org/image/jvx0cdhg5/" rel="nofollow"> https://postimg.org/image/i05643mad/" rel="nofollow"> https://postimg.org/image/3uzd2ad91/" rel="nofollow"> https://postimg.org/image/dtkbormol/" rel="nofollow"> https://postimg.org/image/lh7872lcl/" rel="nofollow"> https://postimg.org/image/bg7fuvel1/" rel="nofollow"> Thanks for any help you can give. Pete.
|
Posted By: Ian Beale
Date Posted: 11 Dec 2017 at 3:27pm
I think you'll find that filter assembly on anything using Allis 10000 up engines going on our AC 45 grader parts books. There is one on the HD 11 516 Buda/Lanova parts engine I got too so might be even earlier in them.
Might be on other Allis models as well.
Probably easier to get the whole assembly than just the parts you're missing
The elements are the same for that type filter and the earlier separate filter assemblies (from the parts books - the canisters etc from those are the same)
Primary 4347787 (Fleetguard FF106)
Secondary 065583 (Fleetguard FF109)
(From AC Forty Five / 45 parts books and experience)
|
Posted By: DMiller
Date Posted: 11 Dec 2017 at 4:03pm
I have the filter head and canisters off my donor, I believe. Will have to go look and let you know.
|
Posted By: gemdozer
Date Posted: 11 Dec 2017 at 5:11pm
I shold have the complet filter housing ass.
|
Posted By: James Coons
Date Posted: 11 Dec 2017 at 10:52pm
Looks like your having tons of fun!!
|
Posted By: Mikez
Date Posted: 11 Dec 2017 at 11:07pm
I really like the video of the ole Pete. Thanks for sharing.
|
Posted By: shameless dude
Date Posted: 12 Dec 2017 at 7:22am
looks like your play pen is a fun place to be!
|
Posted By: gemdozer
Date Posted: 12 Dec 2017 at 9:14am
I check this morning and have the fuel filter housing complet 4389051
|
Posted By: Garlic Pete
Date Posted: 12 Dec 2017 at 11:07am
Thanks everyone. I'm glad you enjoyed. We had a lot of fun. gemdozer - Let me know here or over on ACMOC how much for the filter assembly. I think I still have your address, but I'll check. As far as I can tell, if I can get that filter back in service, I can at least try starting the engine and diagnosing from there. The only other obvious sign of trouble with that unit is the hydraulic pump, which is hung below the crank pulley and driven by two V-belts, has been removed. I still have it and can see where there was damage to the supply line to it from the tank. I just can't tell if that damage is the cause for the partial removal or if it happened after another failure, which is the cause for the partial removal. Anyway, with the fuel filter housing attached, I can at least start the engine, diagnose it and see how it sounds and begin working on other issues. Thanks for the interest and replies. Pete.
|
Posted By: Garlic Pete
Date Posted: 12 Dec 2017 at 11:08am
Dmiller - Thanks for mentioning that you have them, too. If something happens with gemdozer's, I may come back and see if you're interested in selling yours. Pete.
|
Posted By: DMiller
Date Posted: 12 Dec 2017 at 12:06pm
Still have not looked but will get what I have available IF needed!!
|
Posted By: Garlic Pete
Date Posted: 13 Dec 2017 at 8:05am
Can anyone tell me where, on the filter base assembly, to look for a part number? I don't see anything visible in my photos. I need to go back out to the machine and look again. Maybe it is on the top somewhere under that diesel soaked dirt, or on the inside of the raised part of the casting on the top? gemdozer has two different housings and I need to find out which I have to make sure he sends the right one. The part numbers he has are 4377258 and 4389051. He thinks mine should be 4377258, but would like to know for sure. Thanks for any help you can give, Pete.
|
Posted By: gemdozer
Date Posted: 13 Dec 2017 at 12:41pm
The 4389051 is aluminum housing and the 4377258 is in stell housing
|
Posted By: DMiller
Date Posted: 13 Dec 2017 at 12:47pm
So long as get cans and all can exchange the housings, just swap the entire assembly.
|
Posted By: Ian Beale
Date Posted: 13 Dec 2017 at 2:18pm
The Ac 45 parts book for 10000 engine doesn't give a part number for a complete filter assembly, only numbers for the component parts.
In that the head assembly is 4377259
Later (Head assembly is the filter base)
|
Posted By: Garlic Pete
Date Posted: 13 Dec 2017 at 5:39pm
Thanks guys. Garlic Mom checked and our filter base appears to have part number 4377258. Could maybe be a nine at the end, but I think gemdozer said the unit he has with the steel base has a part number of 4377258 on it, so it looks like we've got a match. We might have smoke and noise from that wheel dozer yet! Pete.
|
Posted By: Garlic Pete
Date Posted: 03 Jan 2018 at 10:47am
gemdozer was kind enough to sell me the exact right fuel filter housings and base for the Allis Chalmers 11000 engine in the wheel dozer. He even included one brand new filter with the package! Last weekend I decided to see if I could get it to run. There are seven connections to that filter housing, if I counted correctly. Every single one of them had about an inch or two of almost concrete like stuff plugging them up. I think they must have been mud dauber wasp work, mixed with diesel. I spent most of a day tracing connections, getting loose rusted, grown together fittings on hard hoses and unpacking all that stuff. I now have good clear flow from the tank, through the primary filter, to the lift pump, back to the secondary filter and out to the main injection pump. The injection pump is an American Bosch, I believe it is a PSB model. I have good flow through the hydraulic head and out of it to the pressure relief and air vent port, back to the filter housing return to the tank. I removed the shutoff rod and the cover over the shutoff. The governor regulator rod is free and appears to move normally through the proper range of motion. Everything I can see in there is clean, with a good coating of oil and no rust, not even a speck. When I crank the engine, I can see the injector pump gear rotating behind the governor regulator rod arm. I also removed the top cover from the governor and flyweight section. Everything in there is clean, no rust, moves properly and has a nice coating of oil. I can't get any fuel to pump out of the hydraulic head into the injector lines. I removed the injector lines from the hydraulic head and even though I have flow through the head and out the pressure relief port, nothing pumps out the injector line ports. I removed the center plug bolt from the hydraulic head, which I believe covers the actual injector piston. When I crank the engine with that bolt removed, I get flow out of the center port, but not pulsed flow like the pump is working, just low pressure flow like it is bypassing the pump piston through the metering scroll being pushed by the lift pump. My feeling is that the center injector piston is probably stuck, but I can't for the life of me figure out how to access it. I have no manuals, but have looked at some drawings on the internet. I haven't removed the pump from the engine. I thought perhaps I might be able to access the bottom of the injector pump from the side if I remove the lift pump, but I can't tell for sure. Perhaps there is a cover on the other side of the pump which is against the block? I feel if I could just access that injector pump at the lifter end and gently get it moving, like on a Cat, I'd have this thing running, but I sure can't figure out how to do that. Appreciate any help you all can give. Pete.
|
Posted By: JC-WI
Date Posted: 03 Jan 2018 at 1:13pm
GP, does the governor arm /fuel arm going into the injector head, is that stuck or moves freely? the arm that is behind the bracket that is held in by two screws... maybe the metering pin is wore, broke or missing to lift the fuel metering ring on back side... or a stuck center plunger like you said. Got some material on a PBS pump that would be similar, will post below.
------------- He who says there is no evil has already deceived himself The truth is the truth, sugar coated or not. Trawler II says, "Remember that."
|
Posted By: JC-WI
Date Posted: 03 Jan 2018 at 1:25pm
I will post the PBS lit here, it is for a WD45 diesel but will be similar.
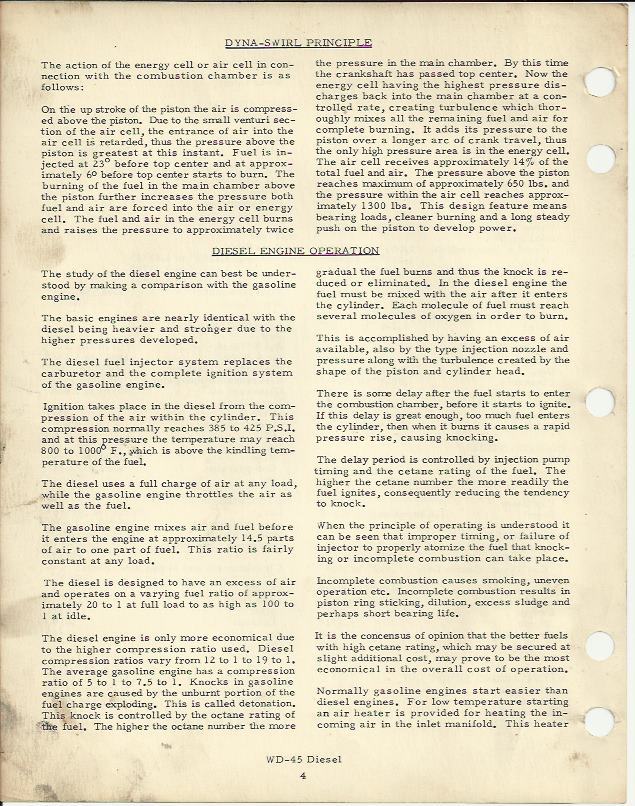
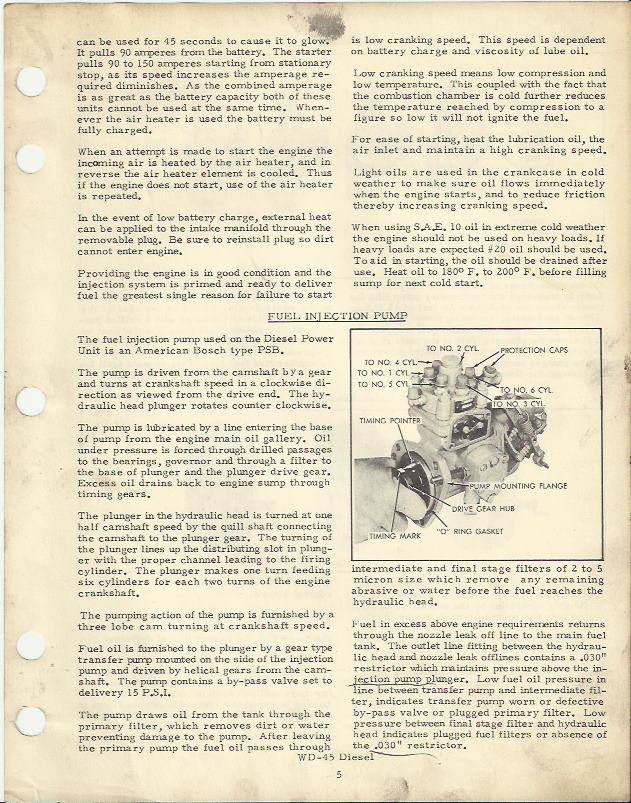
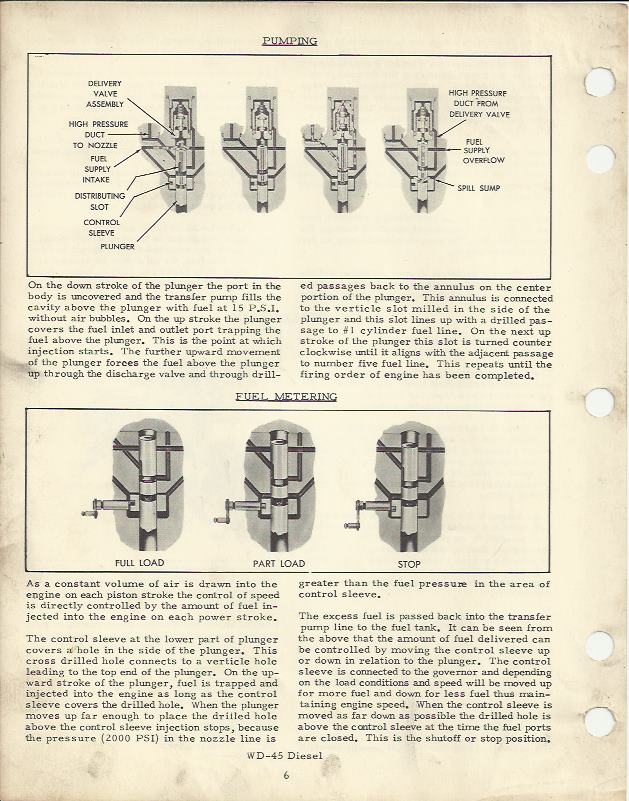
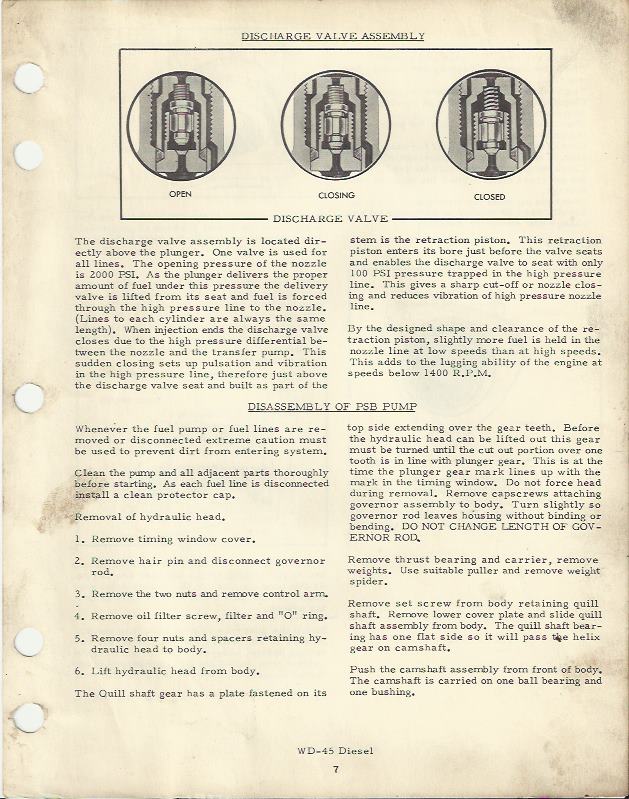
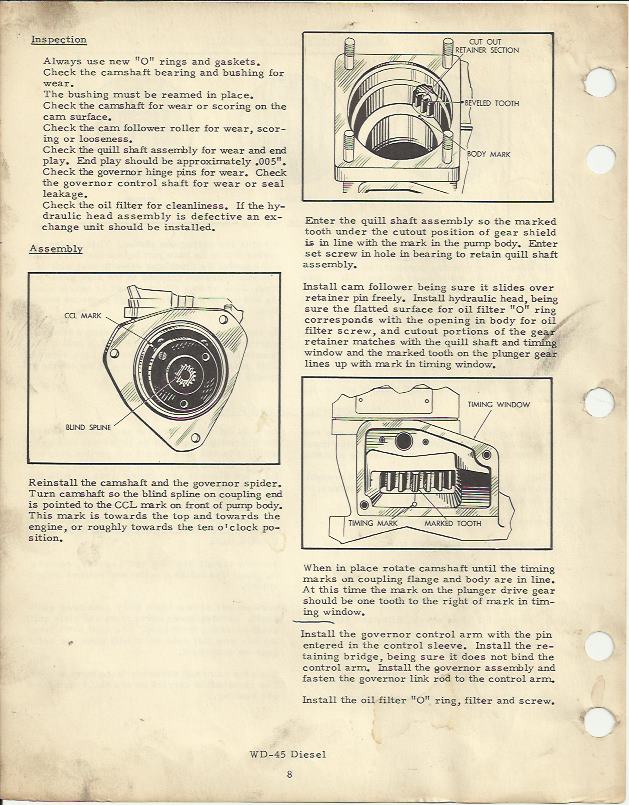
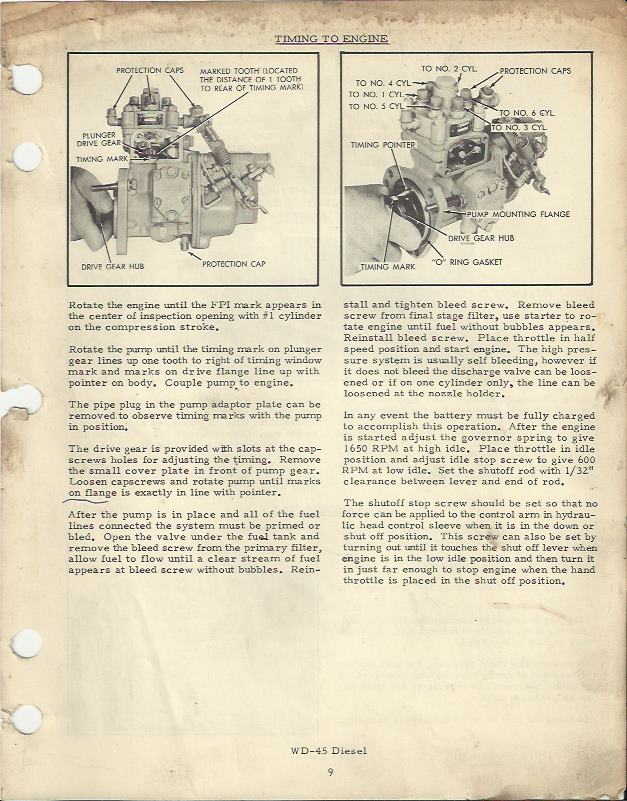
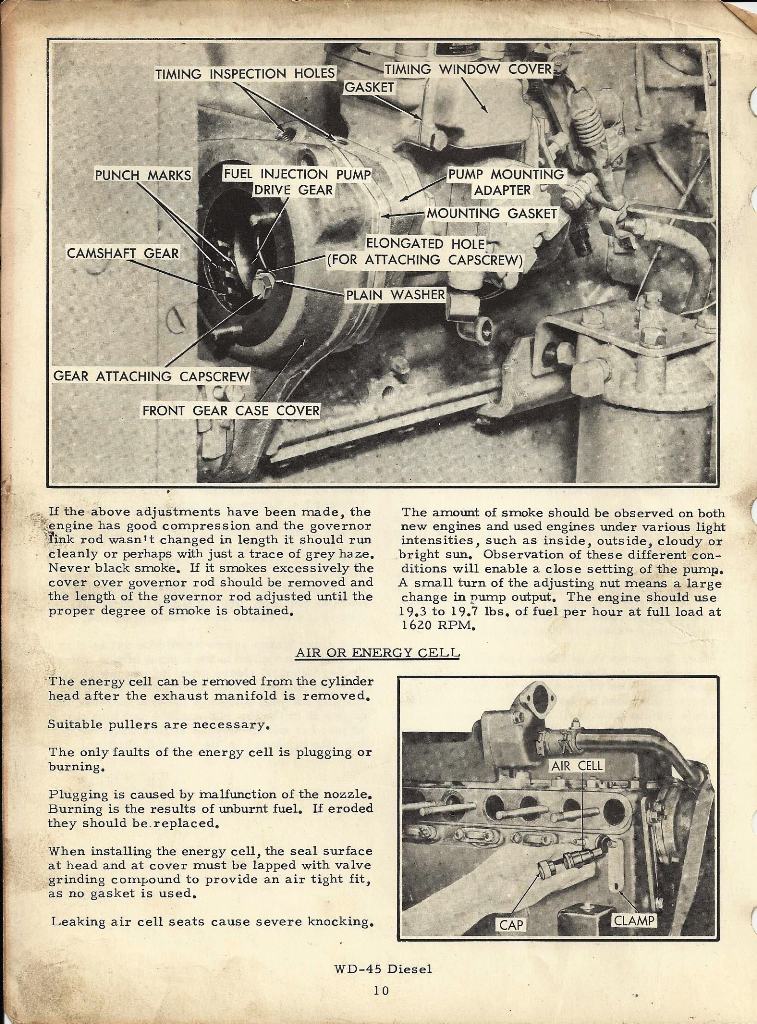
------------- He who says there is no evil has already deceived himself The truth is the truth, sugar coated or not. Trawler II says, "Remember that."
|
Posted By: Garlic Pete
Date Posted: 03 Jan 2018 at 1:59pm
Thanks, JC(WI). That will be really helpful. The governor arm is free. I believe when I first attempted to move it, there was a slight resistance, I'll bet it and the sleeve were just lightly stuck. It didn't take any force at all to get it to move, but it was just a bit sticky for a while. It is moving completely freely now though. I'm sure that the pump plunger probably has the same tiny bit of gum holding it up, so it can't do its job. With the information you've posted, I should pretty easily be able to pull the hydraulic head and get to the pump plunger. With access, I can gently apply a bit of persuasion and work it back and forth until it is free. Thanks for the outstanding information. Next weekend is filled with a hauling trip, so it'll probably be a week and a half before I can put it to use. Hopefully once I'm back with, I'll be able to post some videos of smoke and noise. Pete.
|
Posted By: Ian Beale
Date Posted: 03 Jan 2018 at 3:22pm
IIRC if you take out that stud in the centre of the hydraulic head and the valvery you should be able to get a rod on the top of the plunger and feel if it is moving. If stuck you might be able to bump it down gently.
If you have to remove the head you have to remove a stud that goes in the side of the head (faces the back of the pump iirc). That has a square o-ring on it. Check that it comes out with the stud as it may not and will interfere with getting the head off. And treat it gently as it seems like much to do with PSB pumps it is unobtanium.
And watch that little retaining clip on the bottom of the plunger.
Removing the head is easier if you make yourself the special spanner to undo the pipe nuts. Get yourself a picture, a long socket of the right size, your angle grinder with a thin cut-off wheel and have at it.
I posted on this back when we were getting our Forty Five going.
More on PSB pumps in here
http://www.oldengine.org/members/diesel/Ambac/AmbacMenu1.htm" rel="nofollow - http://www.oldengine.org/members/diesel/Ambac/AmbacMenu1.htm
There was a comment from an injection repairer recently (might have been over at YT) to the effect that with modern diesel you should check that PSB type pumps are actually free if sitting for longer that about 6 months to avoid internal damage to unobtainable parts.
I'd worry that if your plunger is stuck up its cylinder that the spill port ought to be closed and that diesel should not be coming out the top of the head. But I haven't checked a diagram and I hope I'm wrong! The feel test ought to decide that.
|
Posted By: Ian Beale
Date Posted: 03 Jan 2018 at 3:50pm
Also not sure of the manuals you might need but for engine details you might need access to a HD 11 manual .
The Jensales repro for the Forty Five grader is pretty sketchy on the engine section. You need access to a HD 11 one for full cover of the engine (Lanova, 10000, 11000). Though for dozers it covers replacing the cam bearings for the grader engine, which is longer on the front one because of the blower drive.
|
Posted By: HD6 Merv
Date Posted: 03 Jan 2018 at 7:29pm
Just one minor point worth noting. The plug on the side of the heads on psb pumps is often mistaken as a bleed plug. Its not; it covers the delivery, or check valve for the fuel pump. Be very careful if you had that out. That its put back in correctly and the valve and its spring are seating correctly. If spring was incorrectly installed; and bent. It will give you all the syptoms your having. I discovered all this the hard way. . . . As others have said, centre plug is the correct bleed port on a psb pump
------------- tits tyres and tracks
they all cost you money
|
Posted By: Ian Beale
Date Posted: 04 Jan 2018 at 2:54pm
Here are a couple of pages on timing a PSB 6 from the AC Forty Five manual. Apologies for the one upside down
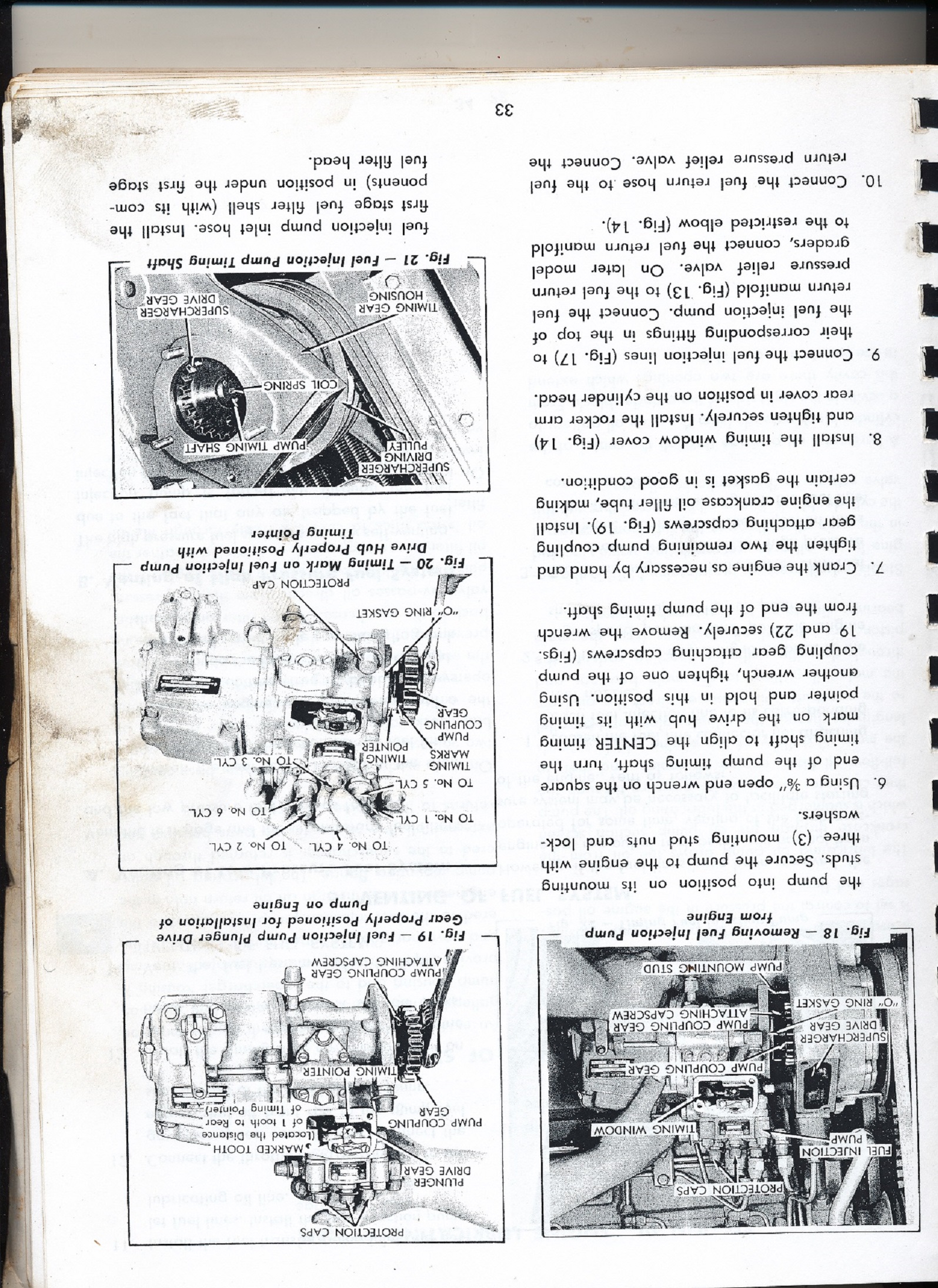
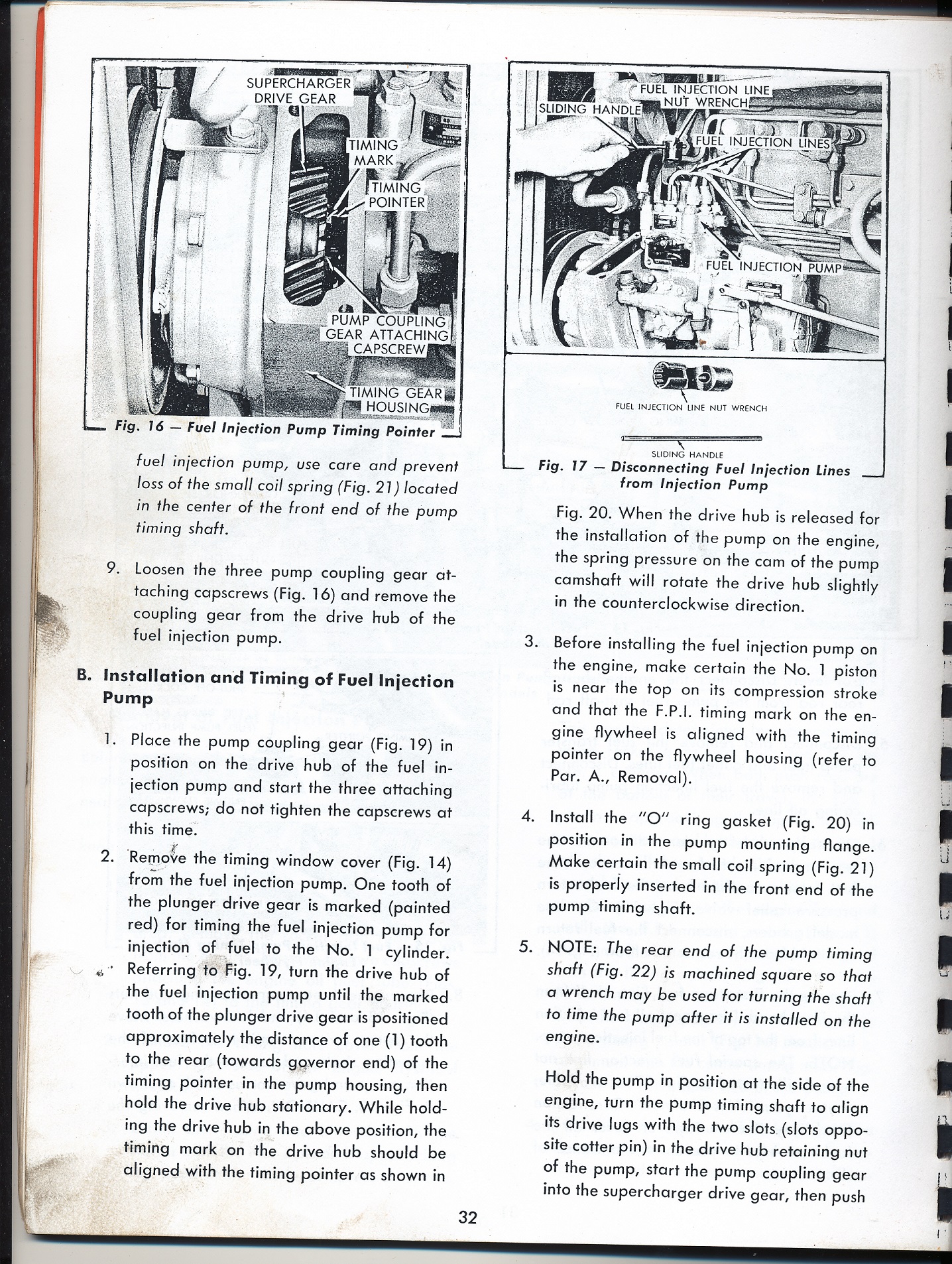
|
Posted By: DiyDave
Date Posted: 04 Jan 2018 at 5:51pm
first page hadda come from a aussie manual...
|
Posted By: Ian Beale
Date Posted: 04 Jan 2018 at 5:54pm
Dave
All positions from Jensales.
Plus I was navigating upload at the time
|
Posted By: ac_sd
Date Posted: 06 Jan 2018 at 6:43pm
Looks like an HD-15A and great Buy !!
|
Posted By: Garlic Pete
Date Posted: 13 Jan 2018 at 7:25pm
I think I've found my problem. It looks like my injector pump plunger is
stuck up. The pivot tang on the sleeve
control shaft has also sheared off.
Here's a picture before disassembly:
https://postimg.org/image/m7c4gs3jp/" rel="nofollow">
Here's a picture of the model and serial number tag:
https://postimg.org/image/vrvr3mil1/" rel="nofollow">
After removing the lines and connectors and the center plug,
here is the flow I get when cranking the engine. This flow is doesn't really pulse, it is more
of a steady fountain.
https://postimg.org/image/l51xybd1h/" rel="nofollow">
Here is the sleeve control rod after removal.
https://postimg.org/image/czjw016r9/" rel="nofollow">
This is the other end, which should have the little pivot
tang attached which fits into a slot in the sleeve.
https://postimg.org/image/6ym731cg5/" rel="nofollow">
Here you can see the sleeve through the hole that the sleeve
control shaft passes through.
https://postimg.org/image/4u1u1zstx/" rel="nofollow">
Here is the hydraulic head after removal. You can see the metering sleeve and slot in
the window.
https://postimg.org/image/56t883b2t/" rel="nofollow">
Here is the broken tang, which I found lying just under the
sleeve.
https://postimg.org/image/pe6o0eg9x/" rel="nofollow">
Here's a close up of the hydraulic head tag.
https://postimg.org/image/k2rrfqrn9/" rel="nofollow">
In this picture of the hydraulic head, you can see that the
injector plunger spring is all the way compressed.
https://postimg.org/image/9fxyabyxh/" rel="nofollow">
When I first removed it, it was not completely compressed,
but almost. I tapped it with a hammer it
moved slightly inward, but is now jammed with the spring completely
compressed. I can move the sleeve on the
plunger shaft, but only by prying it with a chisel and tapping the chisel with
a hammer.
The rotator gear does rotate, but very stiffly. With the smooth, machined surfaces of the plunger,
it is difficult to tell for sure, but I believe it is not rotating with the
gear, leading me to believe it has probably sheared whatever drive interface it
has with the gear.
I suspect my hydraulic head is not field repairable as it
is. I'll probably either have to find a
good replacement or have this one rebuilt.
Any advice?
Pete.
|
Posted By: Ian Beale
Date Posted: 13 Jan 2018 at 8:04pm
Pete
PSB6A - 100EH says it has a 10 mm plunger. Allis played tunes on HD 11 pumps in that some had 9 mm plungers and some 10 - I don't know the inside story there.
Have a look at
http://www.oldengine.org/members/diesel/Ambac/AmbacMenu1.htm" rel="nofollow - http://www.oldengine.org/members/diesel/Ambac/AmbacMenu1.htm
from page 19 on to see how the internals of a PSB work
As far as I know you are in unobtanium territory now with that head as far as rebuilt.
A while back there was an outfit advertising remade or rebuilt ones for PSBs and M100s for pulling but then the PSB ones disappeared. IIRC there is an earlier post of mine on that here somewhere and some replies. Plus some on the injection pump saga we had getting our AC Forty Five going.
Back then I found an Ambac list of replacement heads (pdf so I don't think I can hook it on here) which lists HD5901 as a replacement for your number (HD5155A as I read it). The one on our original pump was HD4607AR (R = rebuilt) for comparison.
Anyway unless you're lucky you're probably looking at finding a used pump that works or a diesel shop that has a hidden replacement head or at least one that is useable. Maybe try Hector Gemme up in Canada who watches here and see what he has
|
Posted By: LeonR2013
Date Posted: 13 Jan 2018 at 9:59pm
Something has sure gone thru. that pump that's created a nightmare. You might call Rick at Cell 314-479-7757 He's fooled around with AC parts for a long time and knows a lot of people.
|
Posted By: DMiller
Date Posted: 14 Jan 2018 at 7:28am
Local Fuel Inj shop shudders every time one is brought in, parts are scarce, the new turn is to try to find a inline Bosch to replace the Ambac or swap to a Roosa Master style.
|
Posted By: Ian Beale
Date Posted: 14 Jan 2018 at 3:00pm
DMiller wrote:
Local Fuel Inj shop shudders every time one is brought in, parts are scarce, the new turn is to try to find a inline Bosch to replace the Ambac or swap to a Roosa Master style. |
DM
Any chance of more detail on these swaps? Which pumps etc. Seems to me that the Allis setup must run the pump at crank speed so the pump must have reduction gears??
|
Posted By: Garlic Pete
Date Posted: 14 Jan 2018 at 3:12pm
It is good to have lots of good support and people who have been there before. One of the guys on the ACMOC board suggested heating it in the oven and cooling the plunger. I put it in Garlic Mom's oven at 350 degrees for fifteen or twenty minutes. (She left out one batch of roasted garlic to make space.) At first it was no dice. I even tried the ice on the plunger end trick. It wasn't really hot yet, though. I could hold my hand on it momentarily before it started to burn. I put it back in for another ten minutes. At that point it was really too hot to touch at all. I got Garlic Mom's BIG junk drawer screwdriver and pried between the spring coils. It looked like it budged. I pried some more. There was definitely some space between the coils now, so I had worked the plunger back up some. It took quite a while of prying it up and tapping it down with a hammer, but pretty soon, the plunger was moving as far as the sleeve would allow. The sleeve was still REALLY stuck on the plunger though. I reheated it a couple of times and kept working it back and forth, using various wedges to hold the sleeve in one position or another. Another twenty minute's work and it is now working really nice. Here's a short video of me working it by hand. You can see the sleeve moving with the plunger, but when it hits the stop, the plunger moves the rest of the way through the sleeve. https://youtu.be/Nhum5QYOn-Y" rel="nofollow - https://youtu.be/Nhum5QYOn-Y And here's a short video where I've used a paperclip to hold the sleeve in one position. You can see the marks on the plunger where the sleeve was stuck. https://youtu.be/wOm6GWo3T9U" rel="nofollow - https://youtu.be/wOm6GWo3T9U Now my only problem is going to be the sleeve control shaft with the sheared key. https://postimg.org/image/pyiiyw145/" rel="nofollow"> https://postimg.org/image/woz08b8ud/" rel="nofollow"> https://postimg.org/image/gqqai71rp/" rel="nofollow"> https://postimg.org/image/rdk3nmpcl/" rel="nofollow"> rymram, you mentioned silver soldering it, but the sleeve has a slot and the key is rectangular so it needs to rotate in relation to the shaft to say parallel with the slot. I bet I could get away with just putting a blob of silver solder on the end and shaping it into a round plug. As long as the plug didn't bind in the slot and didn't come off, it should hold that sleeve wherever it needs to. The sleeve can't really put much torque on the shaft, I believe it essentially floats in there, when it isn't bound up to the plunger. I may just try the solder blob and see what happens. It won't wear as well as the proper system, but it'll probably last for the rest of my life. Pete.
|
Posted By: JC-WI
Date Posted: 14 Jan 2018 at 3:27pm
If you have some real good silver solder, why don't you just heat the two parts up and soldier them back together...have to clean the faces good good, and clean all the extra material away. Good luck.
------------- He who says there is no evil has already deceived himself The truth is the truth, sugar coated or not. Trawler II says, "Remember that."
|
Posted By: Ian Beale
Date Posted: 14 Jan 2018 at 4:02pm
You probably have a good chance of getting that part in useable condition out of a dead pump. Then you'll know it is right.
|
Posted By: Garlic Pete
Date Posted: 21 Jan 2018 at 5:15pm
Last weekend I succeeded in brazing a blob on the end of the
shaft where the tang was. Here’s a photo
of the result. It seemed to work quite
well, didn’t bind and the sleeve moved up and down as it should.
https://postimg.org/image/7hk111uat/" rel="nofollow">
I reassembled the pump and cranked the engine a bit. I got fuel from one injector supply port, but
only one! I could control the flow by
working the governor arm back and forth, from significant pulses down to
nothing in the shutdown position.
I was confused about why I only got fuel from one supply
port until I watched the rotator gear while cranking. The gear wasn’t rotating anymore. Looking closer, I noticed that the timing window
through the sheet metal cover had shifted somewhat. That is as far as I could get last weekend.
Yesterday, I took the hydraulic head off to see what was the
damage. The sheet metal retainer over
the driven gear had rotated and gotten bound between the teeth of the drive
gear and driven gear.
[url=https://postimg.org/image/lrozz4dn9/] https://s26.postimg.org/gga3eerkp/20180120_103615.jpg%5b/img%5d%5b/url" rel="nofollow - [/url ]
[url=https://postimg.org/image/m4ge5byhx/] https://s26.postimg.org/qdl47i1rd/20180120_103832.jpg%5b/img%5d%5b/url" rel="nofollow - [/url ]
[url=https://postimg.org/image/4eepk9q1x/] https://s26.postimg.org/h5svqrzu1/20180120_103833.jpg%5b/img%5d%5b/url" rel="nofollow - [/url ]
[url=https://postimg.org/image/7l993vncl/] https://s26.postimg.org/qqcidn20p/20180120_103835.jpg%5b/img%5d%5b/url" rel="nofollow - [/url ]
[url=https://postimg.org/image/jn4my09fp/] https://s26.postimg.org/ols5cjd8p/20180120_103840.jpg%5b/img%5d%5b/url" rel="nofollow - [/url ]
I know the reason for this problem. When I tried to reassemble the hydraulic head
the first time, there was a small piece of sheet metal over the drive gear on
the end of the quill shaft which interfered with the rotator gear teeth,
preventing the hydraulic head from lowering all the way into place.
I fiddled and fiddled, trying to move the rotator gear teeth
slightly one way or another to fish them past the little piece of sheet metal
without luck. Finally, I decided that
the sheet metal over the quill shaft must have moved out a bit from the position
where it belongs. I bent it back just a
bit with a punch to get it to clear the rotator gear teeth.
That adjustment allowed the hydraulic head to lower down,
but apparently that piece of sheet metal over the quill shaft is supposed to
prevent the sheet metal cover over the rotator gear from rotating itself and
binding in the gear teeth.
[url=https://postimg.org/image/umpu9m7kl/] https://s26.postimg.org/ixlulngm1/20180120_103856.jpg%5b/img%5d%5b/url" rel="nofollow - [/url ]
[url=https://postimg.org/image/f18ipmdlx/] https://s26.postimg.org/667of3otl/20180120_103857.jpg%5b/img%5d%5b/url" rel="nofollow - [/url ]
[url=https://postimg.org/image/41nbe2cx1/] https://s26.postimg.org/yvukbsijt/20180120_103900.jpg%5b/img%5d%5b/url" rel="nofollow - [/url ]
Since the pump was pumping, but not rotating, I knew the
main pump drive shaft was rotating with the engine. There had to be a catastrophic failure somewhere
in the quill shaft or rotator gear. I
pulled the pump and disassembled to investigate.
[url=https://postimg.org/image/cc94lml91/] https://s26.postimg.org/yo6xf0kd5/20180121_082241.jpg%5b/img%5d%5b/url" rel="nofollow - [/url ]
[url=https://postimg.org/image/b9yy31zut/] https://s26.postimg.org/qvg9n0bt5/20180121_082236.jpg%5b/img%5d%5b/url" rel="nofollow - [/url ]
[url=https://postimg.org/image/fvv2bf0th/] https://s26.postimg.org/46r2ng9ux/20180121_082213.jpg%5b/img%5d%5b/url" rel="nofollow - [/url ]
[url=https://postimg.org/image/o1d49r4jp/] https://s26.postimg.org/9i5z8cbex/20180121_083015.jpg%5b/img%5d%5b/url" rel="nofollow - [/url ]
[url=https://postimg.org/image/egthmwa2t/] https://s26.postimg.org/lwsr8oxs9/20180121_083019.jpg%5b/img%5d%5b/url" rel="nofollow - [/url ]
[url=https://postimg.org/image/mmbjl0o11/] https://s26.postimg.org/t00mo9sx5/20180121_083219.jpg%5b/img%5d%5b/url" rel="nofollow - [/url ]
Here’s the problem.
The quill shaft twisted off the helical gear on the bottom of it.
[url=https://postimg.org/image/ipy7p0nlx/] https://s26.postimg.org/hno16h4sp/20180121_083354.jpg%5b/img%5d%5b/url" rel="nofollow - [/url ]
[url=https://postimg.org/image/tcs0ufgbp/] https://s26.postimg.org/m9k5etaw9/20180121_083359.jpg%5b/img%5d%5b/url" rel="nofollow - [/url ]
[url=https://postimg.org/image/ax7jx2k7p/] https://s26.postimg.org/yo6xf6kex/20180121_083432.jpg%5b/img%5d%5b/url" rel="nofollow - [/url ]
[url=https://postimg.org/image/6bbfoqtjp/] https://s26.postimg.org/sahubyae1/20180121_083810.jpg%5b/img%5d%5b/url" rel="nofollow - [/url ]
Here is a picture of the drive gear end of the quill
shaft. It turns out the sheet metal I
saw wasn’t attached to the housing, it is a little sheet metal hat attached to
the top of the quill shaft with a single little cutout.
[url=https://postimg.org/image/uf27d7js5/] https://s26.postimg.org/qiovh7ysp/20180121_083827.jpg%5b/img%5d%5b/url" rel="nofollow - [/url ]
Apparently that sheet metal hat provides a guide to keep the
sheet metal cover over the rotator gear from doing what it did to me. The hat has a cutout to allow the hydraulic
head rotator gear teeth to drop into mesh when the cutout is oriented
properly. I assume that the cutout is
aligned properly when the engine has the No. 1 cylinder at top dead center,
since that is how timing is accomplished.
Luckily, my buddy Daron has three surplus military deuce and
a half engines, each with American Bosch fuel pumps. I made a quick trip up the hill to California
City for spare parts.
He acquired these engines through a government liquidation
auction back around 1980. They haven’t
run or rotated since then, but they’ve been pretty well protected. Two have the pumps still mounted and plumbed,
but one had the pump removed and sitting next to the engine in the crate. We took that one because it was easy.
[url=https://postimg.org/image/on2364f45/] https://s26.postimg.org/6x0el31jd/20180121_063430.jpg%5b/img%5d%5b/url" rel="nofollow - [/url ]
[url=https://postimg.org/image/oaaozy4k5/] https://s26.postimg.org/hju7qiheh/20180121_063445.jpg%5b/img%5d%5b/url" rel="nofollow - [/url ]
[url=https://postimg.org/image/lg7jmh7it/] https://s26.postimg.org/cl6pbyiqh/20180121_063512.jpg%5b/img%5d%5b/url" rel="nofollow - [/url ]
It is a PSB6 pump, although a slightly different
variant. Hopefully the internal parts I
need will be the same as mine.
The military pumps have an interesting timing advance
mechanism between the pump and the engine accessory drive. It apparently works from oil pressure, as it
has a line that connects from the pump oil supply to its housing.
[url=https://postimg.org/image/7cboe1q0l/] https://s26.postimg.org/m8a7ln1fd/20180121_072609.jpg%5b/img%5d%5b/url" rel="nofollow - [/url ]
I separated them and can see it has a slight helical gear
with springs which push the drive out on the helix. As oil pressure (or perhaps shaft RPMs)
increase, the springs are compressed and the helix changes the injection timing
slightly.
[url=https://postimg.org/image/5xa3pb9hx/] https://s26.postimg.org/8eluwkteh/20180121_072615.jpg%5b/img%5d%5b/url" rel="nofollow - [/url ]
[url=https://postimg.org/image/xxe79m03p/] https://s26.postimg.org/d0hz4y22x/20180121_072621.jpg%5b/img%5d%5b/url" rel="nofollow - [/url ]
[url=https://postimg.org/image/v3b1w5ihx/] https://s26.postimg.org/esaxzu609/20180121_072626.jpg%5b/img%5d%5b/url" rel="nofollow - [/url ]
[url=https://postimg.org/image/m8a7ll3z9/] https://s26.postimg.org/hme3d8ig9/20180121_072629.jpg%5b/img%5d%5b/url" rel="nofollow - [/url ]
After separating the variable timing drive, the first order
of business was to remove the governor control shaft. If this sleeve locator tang was intact, I
didn’t want to risk breaking this one.
Pulling the shutoff cover, the inside was promisingly clean and rust
free.
[url=https://postimg.org/image/n80ihdylh/] https://s26.postimg.org/yx4i5cpk9/20180121_063623.jpg%5b/img%5d%5b/url" rel="nofollow - [/url ]
I removed the hairpin clip on the governor shaft, pushed the
shaft back through the pivot arm and removed the two shaft retainer screws and
clamp. They all came off nicely and
easily.
I tried to be careful not to put any rotating force to the
shaft at all. I tried to pry carefully
on the retainer ears and the governor arm itself. Nothing wanted to move.
I gradually escalated my efforts, prying a little harder
each time. I couldn’t get the shaft or
retainer to budge. I finally resorted to
trying to very slightly rotate the shaft retainer ears, thinking perhaps it was
gummy or a bit stuck.
At first I couldn’t even get the shaft to rotate at
all. Eventually I was able to just very
slightly rotate the retainer a fraction one way, then a fraction the
other. I felt confident that I wasn’t
moving it enough to shear the tang off.
I was just moving it enough to have a barely perceptible movement.
I kept prying gently while very slightly rotating it one
way, then the other. One time, I pried a
bit too hard and broke off one of the shaft retainer ears, but it still wouldn’t
come out.
Finally, I decided to apply some heat, so I carefully and
gently heated the hydraulic head around the area where the shaft
penetrates. I was taking a risk because
of the rubber seal behind the shaft and the other passages and seals inside the
head, but I had to get the shaft out one way or another.
Eventually, after several cycles of heat, working slightly back
and forth and prying, getting it a bit hotter each time, I got the shaft to
come out.
Unfortunately, once the shaft was out, it was apparent that
its tang had been sheared long ago and the shaft, the sleeve and what I could
see of the plunger were very crusty and corroded. Apparently this part of the system had
suffered from years of being empty with an opening to humidity.
[url=https://postimg.org/image/bb8vwymed/] https://s26.postimg.org/xzy2wj3s9/20180121_120220.jpg%5b/img%5d%5b/url" rel="nofollow - [/url ]
[url=https://postimg.org/image/rm8ztam1h/] https://s26.postimg.org/5ab6zwmxl/20180121_120227.jpg%5b/img%5d%5b/url" rel="nofollow - [/url ]
[url=https://postimg.org/image/n80ihdylh/] https://s26.postimg.org/yx4i5cpk9/20180121_063623.jpg%5b/img%5d%5b/url" rel="nofollow - [/url ]
[url=https://postimg.org/image/m5qbytd79/] https://s26.postimg.org/6x0el1jix/20180121_071148.jpg%5b/img%5d%5b/url" rel="nofollow - [/url ]
[url=https://postimg.org/image/lsyxsosdh/] https://s26.postimg.org/eczo6w4o9/20180121_071153.jpg%5b/img%5d%5b/url" rel="nofollow - [/url ]
Obviously, this pump wasn’t going to be a donor for a sleeve
control shaft. That is O. K. Daron has two more we can investigate for
that piece and this pump still might have the other parts I need.
I pulled the quill shaft out, which looked great.
[url=https://postimg.org/image/uds9jrn39/] https://s26.postimg.org/ml1lrsh49/20180121_073008.jpg%5b/img%5d%5b/url" rel="nofollow - [/url ]
[url=https://postimg.org/image/lirf9960l/] https://s26.postimg.org/d0hz4wzi1/20180121_073041.jpg%5b/img%5d%5b/url" rel="nofollow - [/url ]
[url=https://postimg.org/image/js8e7ee39/] https://s26.postimg.org/cc94llqe1/20180121_073049.jpg%5b/img%5d%5b/url" rel="nofollow - [/url ]
One point I’d like to confirm with those who have been there
before me relates to aligning the sheet metal window on the quill shaft
hat. I assumed that I need to align the
timing pointer on the pump drive with the timing mark, then install the quill
shaft such that the window in the hat faces out, allowing the hydraulic head
gear to drop in.
In this photo, you can see the pointer, with the timing mark
about twenty degrees past the pointer.
[url=https://postimg.org/image/5lsncly7p/] https://s26.postimg.org/4jigu2feh/20180121_083817.jpg%5b/img%5d%5b/url" rel="nofollow - [/url ]
Here is how I installed the quill shaft with the line
aligned with the pointer. It made me a
bit nervous that the sheet metal hat isn’t quite centered, but I tried one
tooth in either direction and this is clearly the best fit.
[url=https://postimg.org/image/oe4ig7a1h/] https://s26.postimg.org/urtljgexl/20180121_084239.jpg%5b/img%5d%5b/url" rel="nofollow - [/url ]
Now, my problem is to find out how to put the No. 1 cylinder
on top dead center of the compression stroke.
I found the timing window on the flywheel housing. It is in an easy to get to spot which is
impossible to see because of the torque converter hoses and other stuff in the
way.
I pulled the valve cover and rotated the engine by hand a handful
of times, identifying when the No. 1 cylinder valves were rocking from one
closing to the other opening. From
there, I rotate the engine three hundred sixty degrees, figuring that should be
close to top dead center.
Garlic Mom got her flashlight and hand mirror and squeezed
between the tire and frame to watch the timing window for me.
[url=https://postimg.org/image/ax7jxbs05/] https://s26.postimg.org/rkz1ztmrt/20180121_095320.jpg%5b/img%5d%5b/url" rel="nofollow - [/url ]
We went back and forth about thirty degrees on either side
of where I thought top dead center was.
We decided that this hole and circle must be the top dead center mark,
as it seemed to be just in the right spot.
That spot also corresponded pretty well with 360 degrees from the valve
rock point. Is this really the timing
mark?
[url=https://postimg.org/image/iegrc3745/] https://s26.postimg.org/96oive021/20180121_100343.jpg%5b/img%5d%5b/url" rel="nofollow - [/url ]
[url=https://postimg.org/image/7245uab9x/] https://s26.postimg.org/pug0xv7o9/20180121_100531.jpg%5b/img%5d%5b/url" rel="nofollow - [/url ]
If it is, I should be at top dead center for the No. 1
cylinder. By the way, I assume that No.
1 is the one closest to the fan and furthest from the flywheel.
I see that the pump drive gear has a FRONT mark and a timing
punch mark on a tooth immediately below that FRONT mark.
[url=https://postimg.org/image/v5uximjh1/] https://s26.postimg.org/xafajpl3t/20180121_102105.jpg%5b/img%5d%5b/url" rel="nofollow - [/url ]
If I’m right about the position of the engine, I expected to find a timing mark on the
accessory drive gear. I couldn’t find
anything though.
[url=https://postimg.org/image/ipy7pf0l1/] https://s26.postimg.org/4w9v0d7zt/20180121_102304_001.jpg%5b/img%5d%5b/url" rel="nofollow - [/url ]
[url=https://postimg.org/image/qwq7gg0s5/] https://s26.postimg.org/e5c19xr09/20180121_102306.jpg%5b/img%5d%5b/url" rel="nofollow - [/url ]
[url=https://postimg.org/image/cc94m50tx/] https://s26.postimg.org/qiovhdbp5/20180121_102329_001.jpg%5b/img%5d%5b/url" rel="nofollow - [/url ]
[url=https://postimg.org/image/d31urcq6d/] https://s26.postimg.org/rm8zsrjbd/20180121_102330_001.jpg%5b/img%5d%5b/url" rel="nofollow - [/url ]
[url=https://postimg.org/image/te1yo6aj9/] https://s26.postimg.org/9w7b88dll/20180121_102333.jpg%5b/img%5d%5b/url" rel="nofollow - [/url ]
[url=https://postimg.org/image/6pcro7nw5/] https://s26.postimg.org/alq3k78vt/20180121_102355_001.jpg%5b/img%5d%5b/url" rel="nofollow - [/url ]
[url=https://postimg.org/image/ly2p2e29h/] https://s26.postimg.org/ypgv8wc1l/20180121_102358.jpg%5b/img%5d%5b/url" rel="nofollow - [/url ]
I see that the pump drive gear has slotted bolt holes. I assume I need to find the timing mark on
the accessory drive gear and set the gear in, then align the pump drive flange
score to the pump timing pointer, then tighten down the drive gear on to the
pump drive flange. That will ensure the
quill shaft hat window will allow the hydraulic head to drop on. At the same time, the hydraulic head rotator
gear will be timed because the marked tooth will be aligned with the timing
pointer in the timing window of the pump itself.
Those in the know, please confirm the above pump
installation procedures. If I’m right
about the procedure, maybe I don’t need to worry too much about timing marks
between the accessory drive gear and the pump drive gear. As long as the engine really has No. 1 at top
dead center on the compression stroke and I have enough room in the pump drive
gear slots to align the pump drive flange score mark with the pump timing
pointer, everything should be O. K.
Now for some questions about the rotating gear, the tin
cover for it and the drive from the rotating gear to the plunger itself.
I can see that the tin cover is assembled by slipping it
over the rotating gear and hydraulic head flange, then it is crimped in four
places and staked at one place (which should keep it from rotating).
Since my tin cover got chewed up, I didn’t see any loss by
prying it off.
[url=https://postimg.org/image/z289eszdh/] https://s26.postimg.org/6pcrocdnd/20180121_103818.jpg%5b/img%5d%5b/url" rel="nofollow - [/url ]
[url=https://postimg.org/image/ei3fgbrc5/] https://s26.postimg.org/96oivm59l/20180121_103819.jpg%5b/img%5d%5b/url" rel="nofollow - [/url ]
[url=https://postimg.org/image/ir85ihf5x/] https://s26.postimg.org/84ecd270p/20180121_103820.jpg%5b/img%5d%5b/url" rel="nofollow - [/url ]
If I had to, I think I could straight this cover out and
salvage it, but I think I’m better off to carefully remove the tin cover from Daron’s
donor pump. It appears to be in perfect
shape and I don’t see any differences in this area between the two pumps.
If I can remove the tin cover from the donor pump, should I
be O. K. to just recrimp in the same four places with a screwdriver, then stake
it with a punch in the same place as is provided on both hydraulic heads?
Once I had the tin cover off, I could see what I think are
other problems. The rotating gear
operates on what I think is supposed to be a one piece collar which has two
ears engaged in recesses in the rotating gear and has a square opening through
which the square part of the plunger shaft passes.
On my pump, this collar is in two pieces. It must have split when the plunger was seized
and the engine was first rotated. It is
possible that it is supposed to be in two pieces, I haven’t taken apart the
donor hydraulic head yet.
I don’t think it is supposed to be in two pieces because the
two pieces aren’t symmetrical and the plunger shaft is able to move rather a
lot in relation to the rotating gear.
Here are some pictures of the assembly as it is now, including a couple
which show the plunger shaft rotated within the collar one way, then the other.
[url=https://postimg.org/image/w8541chrp/] https://s26.postimg.org/7245uighl/20180121_105737.jpg%5b/img%5d%5b/url" rel="nofollow - [/url ]
[url=https://postimg.org/image/xafajvsv9/] https://s26.postimg.org/5ztzbypyh/20180121_105744.jpg%5b/img%5d%5b/url" rel="nofollow - [/url ]
[url=https://postimg.org/image/tqtcucddh/] https://s26.postimg.org/7evk0ye9l/20180121_105748.jpg%5b/img%5d%5b/url" rel="nofollow - [/url ]
[url=https://postimg.org/image/4ksengu2t/] https://s26.postimg.org/3v9mb3tjd/20180121_105752.jpg%5b/img%5d%5b/url" rel="nofollow - [/url ]
The plunger does rotate with the gear, but I’d estimate
there is probably fifteen or twenty degrees of play with the system the way it
currently is. I can’t imagine this is
acceptable. Without disassembling the
donor hydraulic head, I can see that all the rotating gear and drive stuff is
in good shape and doesn’t appear to have the slack that this system has. Is it likely I can swap the drive collar from
the donor pump onto this one?
I know I can’t swap plungers, as they’re matched. I would expect this drive collar and the
square part of the plunger to be standardized though, so I hope exchanging the
drive collar shouldn’t be a problem.
That leads me to what I hope is my last question: If the drive collar can be exchanged, I have
four possibilities to assemble the rotating gear onto the plunger shaft. How do I time the shaft to the drive
collar? Is it as simple as aligning the
spill slot in the plunger with the timing tooth on the rotating gear? Maybe there is a timing mark on the plunger
shaft end that I haven’t noticed?
Thanks for any help the group can give me.
I think if I can accumulate all the knowledge and hopefully
find one good governor control shaft with a good tang on it from Daron, I might
be able to reassemble this thing and hear it run next weekend.
Pete.
|
Posted By: Garlic Pete
Date Posted: 21 Jan 2018 at 5:17pm
Apparently only the first photo link above worked. The links worked in other posts, maybe my post had too many characters. I'm going to try again in three pieces here.
Last weekend I succeeded in brazing a blob on the end of the
shaft where the tang was. Here’s a photo
of the result. It seemed to work quite
well, didn’t bind and the sleeve moved up and down as it should.
https://postimg.org/image/7hk111uat/" rel="nofollow">
I reassembled the pump and cranked the engine a bit. I got fuel from one injector supply port, but
only one! I could control the flow by
working the governor arm back and forth, from significant pulses down to
nothing in the shutdown position.
I was confused about why I only got fuel from one supply
port until I watched the rotator gear while cranking. The gear wasn’t rotating anymore. Looking closer, I noticed that the timing
window through the sheet metal cover had shifted somewhat. That is as far as I could get last weekend.
Yesterday, I took the hydraulic head off to see what was the
damage. The sheet metal retainer over
the driven gear had rotated and gotten bound between the teeth of the drive
gear and driven gear.
[url=https://postimg.org/image/lrozz4dn9/] https://s26.postimg.org/gga3eerkp/20180120_103615.jpg%5b/img%5d%5b/url" rel="nofollow - [/url ]
[url=https://postimg.org/image/m4ge5byhx/] https://s26.postimg.org/qdl47i1rd/20180120_103832.jpg%5b/img%5d%5b/url" rel="nofollow - [/url ]
[url=https://postimg.org/image/4eepk9q1x/] https://s26.postimg.org/h5svqrzu1/20180120_103833.jpg%5b/img%5d%5b/url" rel="nofollow - [/url ]
[url=https://postimg.org/image/7l993vncl/] https://s26.postimg.org/qqcidn20p/20180120_103835.jpg%5b/img%5d%5b/url" rel="nofollow - [/url ]
[url=https://postimg.org/image/jn4my09fp/] https://s26.postimg.org/ols5cjd8p/20180120_103840.jpg%5b/img%5d%5b/url" rel="nofollow - [/url ]
I know the reason for this problem. When I tried to reassemble the hydraulic head
the first time, there was a small piece of sheet metal over the drive gear on
the end of the quill shaft which interfered with the rotator gear teeth,
preventing the hydraulic head from lowering all the way into place.
I fiddled and fiddled, trying to move the rotator gear teeth
slightly one way or another to fish them past the little piece of sheet metal
without luck. Finally, I decided that
the sheet metal over the quill shaft must have moved out a bit from the
position where it belongs. I bent it
back just a bit with a punch to get it to clear the rotator gear teeth.
That adjustment allowed the hydraulic head to lower down,
but apparently that piece of sheet metal over the quill shaft is supposed to
prevent the sheet metal cover over the rotator gear from rotating itself and
binding in the gear teeth.
[url=https://postimg.org/image/umpu9m7kl/] https://s26.postimg.org/ixlulngm1/20180120_103856.jpg%5b/img%5d%5b/url" rel="nofollow - [/url ]
[url=https://postimg.org/image/f18ipmdlx/] https://s26.postimg.org/667of3otl/20180120_103857.jpg%5b/img%5d%5b/url" rel="nofollow - [/url ]
[url=https://postimg.org/image/41nbe2cx1/] https://s26.postimg.org/yvukbsijt/20180120_103900.jpg%5b/img%5d%5b/url" rel="nofollow - [/url ]
Since the pump was pumping, but not rotating, I knew the
main pump drive shaft was rotating with the engine. There had to be a catastrophic failure
somewhere in the quill shaft or rotator gear.
I pulled the pump and disassembled to investigate.
[url=https://postimg.org/image/cc94lml91/] https://s26.postimg.org/yo6xf0kd5/20180121_082241.jpg%5b/img%5d%5b/url" rel="nofollow - [/url ]
[url=https://postimg.org/image/b9yy31zut/] https://s26.postimg.org/qvg9n0bt5/20180121_082236.jpg%5b/img%5d%5b/url" rel="nofollow - [/url ]
[url=https://postimg.org/image/fvv2bf0th/] https://s26.postimg.org/46r2ng9ux/20180121_082213.jpg%5b/img%5d%5b/url" rel="nofollow - [/url ]
[url=https://postimg.org/image/o1d49r4jp/] https://s26.postimg.org/9i5z8cbex/20180121_083015.jpg%5b/img%5d%5b/url" rel="nofollow - [/url ]
[url=https://postimg.org/image/egthmwa2t/] https://s26.postimg.org/lwsr8oxs9/20180121_083019.jpg%5b/img%5d%5b/url" rel="nofollow - [/url ]
[url=https://postimg.org/image/mmbjl0o11/] https://s26.postimg.org/t00mo9sx5/20180121_083219.jpg%5b/img%5d%5b/url" rel="nofollow - [/url ]
Here’s the problem.
The quill shaft twisted off the helical gear on the bottom of it.
[url=https://postimg.org/image/ipy7p0nlx/] https://s26.postimg.org/hno16h4sp/20180121_083354.jpg%5b/img%5d%5b/url" rel="nofollow - [/url ]
[url=https://postimg.org/image/tcs0ufgbp/] https://s26.postimg.org/m9k5etaw9/20180121_083359.jpg%5b/img%5d%5b/url" rel="nofollow - [/url ]
[url=https://postimg.org/image/ax7jx2k7p/] https://s26.postimg.org/yo6xf6kex/20180121_083432.jpg%5b/img%5d%5b/url" rel="nofollow - [/url ]
[url=https://postimg.org/image/6bbfoqtjp/] https://s26.postimg.org/sahubyae1/20180121_083810.jpg%5b/img%5d%5b/url" rel="nofollow - [/url ]
Here is a picture of the drive gear end of the quill
shaft. It turns out the sheet metal I
saw wasn’t attached to the housing, it is a little sheet metal hat attached to
the top of the quill shaft with a single little cutout.
[url=https://postimg.org/image/uf27d7js5/] https://s26.postimg.org/qiovh7ysp/20180121_083827.jpg%5b/img%5d%5b/url" rel="nofollow - [/url ]
|
Posted By: Garlic Pete
Date Posted: 21 Jan 2018 at 5:21pm
Sorry for the mess. I guess it didn't like the hyperlinks.
Last weekend I succeeded in brazing a blob on the end of the
shaft where the tang was. Here’s a photo
of the result. It seemed to work quite
well, didn’t bind and the sleeve moved up and down as it should.
https://postimg.org/image/7hk111uat/" rel="nofollow">
I reassembled the pump and cranked the engine a bit. I got fuel from one injector supply port, but
only one! I could control the flow by
working the governor arm back and forth, from significant pulses down to
nothing in the shutdown position.
I was confused about why I only got fuel from one supply
port until I watched the rotator gear while cranking. The gear wasn’t rotating anymore. Looking closer, I noticed that the timing
window through the sheet metal cover had shifted somewhat. That is as far as I could get last weekend.
Yesterday, I took the hydraulic head off to see what was the
damage. The sheet metal retainer over
the driven gear had rotated and gotten bound between the teeth of the drive
gear and driven gear.
https://postimg.org/image/lrozz4dn9/" rel="nofollow">
https://postimg.org/image/m4ge5byhx/" rel="nofollow">
https://postimg.org/image/4eepk9q1x/" rel="nofollow">
https://postimg.org/image/7l993vncl/" rel="nofollow">
https://postimg.org/image/jn4my09fp/" rel="nofollow">
I know the reason for this problem. When I tried to reassemble the hydraulic head
the first time, there was a small piece of sheet metal over the drive gear on
the end of the quill shaft which interfered with the rotator gear teeth,
preventing the hydraulic head from lowering all the way into place.
I fiddled and fiddled, trying to move the rotator gear teeth
slightly one way or another to fish them past the little piece of sheet metal
without luck. Finally, I decided that
the sheet metal over the quill shaft must have moved out a bit from the
position where it belongs. I bent it
back just a bit with a punch to get it to clear the rotator gear teeth.
That adjustment allowed the hydraulic head to lower down,
but apparently that piece of sheet metal over the quill shaft is supposed to
prevent the sheet metal cover over the rotator gear from rotating itself and
binding in the gear teeth.
https://postimg.org/image/umpu9m7kl/" rel="nofollow">
https://postimg.org/image/f18ipmdlx/" rel="nofollow">
https://postimg.org/image/41nbe2cx1/" rel="nofollow">
Since the pump was pumping, but not rotating, I knew the
main pump drive shaft was rotating with the engine. There had to be a catastrophic failure
somewhere in the quill shaft or rotator gear.
I pulled the pump and disassembled to investigate.
https://postimg.org/image/cc94lml91/" rel="nofollow">
https://postimg.org/image/b9yy31zut/" rel="nofollow">
https://postimg.org/image/fvv2bf0th/" rel="nofollow">
https://postimg.org/image/o1d49r4jp/" rel="nofollow">
https://postimg.org/image/egthmwa2t/" rel="nofollow">
https://postimg.org/image/mmbjl0o11/" rel="nofollow">
Here’s the problem.
The quill shaft twisted off the helical gear on the bottom of it.
https://postimg.org/image/ipy7p0nlx/" rel="nofollow">
https://postimg.org/image/tcs0ufgbp/" rel="nofollow">
https://postimg.org/image/ax7jx2k7p/" rel="nofollow">
https://postimg.org/image/6bbfoqtjp/" rel="nofollow">
Here is a picture of the drive gear end of the quill
shaft. It turns out the sheet metal I
saw wasn’t attached to the housing, it is a little sheet metal hat attached to
the top of the quill shaft with a single little cutout.
https://postimg.org/image/uf27d7js5/" rel="nofollow">
Apparently that sheet metal hat provides a guide to keep the
sheet metal cover over the rotator gear from doing what it did to me. The hat has a cutout to allow the hydraulic
head rotator gear teeth to drop into mesh when the cutout is oriented
properly. I assume that the cutout is
aligned properly when the engine has the No. 1 cylinder at top dead center,
since that is how timing is accomplished.
Luckily, my buddy Daron has three surplus military deuce and
a half engines, each with American Bosch fuel pumps. I made a quick trip up the hill to California
City for spare parts.
He acquired these engines through a government liquidation
auction back around 1980. They haven’t
run or rotated since then, but they’ve been pretty well protected. Two have the pumps still mounted and plumbed,
but one had the pump removed and sitting next to the engine in the crate. We took that one because it was easy.
https://postimg.org/image/on2364f45/" rel="nofollow">
https://postimg.org/image/oaaozy4k5/" rel="nofollow">
https://postimg.org/image/lg7jmh7it/" rel="nofollow">
It is a PSB6 pump, although a slightly different
variant. Hopefully the internal parts I
need will be the same as mine.
The military pumps have an interesting timing advance
mechanism between the pump and the engine accessory drive. It apparently works from oil pressure, as it
has a line that connects from the pump oil supply to its housing.
https://postimg.org/image/7cboe1q0l/" rel="nofollow">
I separated them and can see it has a slight helical gear
with springs which push the drive out on the helix. As oil pressure (or perhaps shaft RPMs)
increase, the springs are compressed and the helix changes the injection timing
slightly.
https://postimg.org/image/5xa3pb9hx/" rel="nofollow">
https://postimg.org/image/xxe79m03p/" rel="nofollow">
https://postimg.org/image/v3b1w5ihx/" rel="nofollow">
https://postimg.org/image/m8a7ll3z9/" rel="nofollow">
After separating the variable timing drive, the first order
of business was to remove the governor control shaft. If this sleeve locator tang was intact, I
didn’t want to risk breaking this one.
Pulling the shutoff cover, the inside was promisingly clean and rust
free.
https://postimg.org/image/n80ihdylh/" rel="nofollow">
I removed the hairpin clip on the governor shaft, pushed the
shaft back through the pivot arm and removed the two shaft retainer screws and
clamp. They all came off nicely and easily.
I tried to be careful not to put any rotating force to the
shaft at all. I tried to pry carefully
on the retainer ears and the governor arm itself. Nothing wanted to move.
I gradually escalated my efforts, prying a little harder
each time. I couldn’t get the shaft or
retainer to budge. I finally resorted to
trying to very slightly rotate the shaft retainer ears, thinking perhaps it was
gummy or a bit stuck.
At first I couldn’t even get the shaft to rotate at
all. Eventually I was able to just very
slightly rotate the retainer a fraction one way, then a fraction the
other. I felt confident that I wasn’t
moving it enough to shear the tang off.
I was just moving it enough to have a barely perceptible movement.
I kept prying gently while very slightly rotating it one
way, then the other. One time, I pried a
bit too hard and broke off one of the shaft retainer ears, but it still
wouldn’t come out.
Finally, I decided to apply some heat, so I carefully and
gently heated the hydraulic head around the area where the shaft
penetrates. I was taking a risk because
of the rubber seal behind the shaft and the other passages and seals inside the
head, but I had to get the shaft out one way or another.
Eventually, after several cycles of heat, working slightly
back and forth and prying, getting it a bit hotter each time, I got the shaft
to come out.
Unfortunately, once the shaft was out, it was apparent that
its tang had been sheared long ago and the shaft, the sleeve and what I could
see of the plunger were very crusty and corroded. Apparently this part of the system had
suffered from years of being empty with an opening to humidity.
https://postimg.org/image/bb8vwymed/" rel="nofollow">
https://postimg.org/image/rm8ztam1h/" rel="nofollow">
https://postimg.org/image/n80ihdylh/" rel="nofollow">
https://postimg.org/image/m5qbytd79/" rel="nofollow">
https://postimg.org/image/lsyxsosdh/" rel="nofollow">
Obviously, this pump wasn’t going to be a donor for a sleeve
control shaft. That is O. K. Daron has two more we can investigate for
that piece and this pump still might have the other parts I need.
I pulled the quill shaft out, which looked great.
https://postimg.org/image/uds9jrn39/" rel="nofollow">
https://postimg.org/image/lirf9960l/" rel="nofollow">
https://postimg.org/image/js8e7ee39/" rel="nofollow">
One point I’d like to confirm with those who have been there
before me relates to aligning the sheet metal window on the quill shaft
hat. I assumed that I need to align the
timing pointer on the pump drive with the timing mark, then install the quill
shaft such that the window in the hat faces out, allowing the hydraulic head
gear to drop in.
In this photo, you can see the pointer, with the timing mark
about twenty degrees past the pointer.
https://postimg.org/image/5lsncly7p/" rel="nofollow">
Here is how I installed the quill shaft with the line
aligned with the pointer. It made me a
bit nervous that the sheet metal hat isn’t quite centered, but I tried one
tooth in either direction and this is clearly the best fit.
https://postimg.org/image/oe4ig7a1h/" rel="nofollow">
Now, my problem is to find out how to put the No. 1 cylinder
on top dead center of the compression stroke.
I found the timing window on the flywheel housing. It is in an easy to get to spot which is
impossible to see because of the torque converter hoses and other stuff in the
way.
I pulled the valve cover and rotated the engine by hand a
handful of times, identifying when the No. 1 cylinder valves were rocking from
one closing to the other opening. From
there, I rotate the engine three hundred sixty degrees, figuring that should be
close to top dead center.
Garlic Mom got her flashlight and hand mirror and squeezed
between the tire and frame to watch the timing window for me.
https://postimg.org/image/ax7jxbs05/" rel="nofollow">
We went back and forth about thirty degrees on either side
of where I thought top dead center was.
We decided that this hole and circle must be the top dead center mark,
as it seemed to be just in the right spot.
That spot also corresponded pretty well with 360 degrees from the valve
rock point. Is this really the timing
mark?
https://postimg.org/image/iegrc3745/" rel="nofollow">
https://postimg.org/image/7245uab9x/" rel="nofollow">
If it is, I should be at top dead center for the No. 1
cylinder. By the way, I assume that No.
1 is the one closest to the fan and furthest from the flywheel.
I see that the pump drive gear has a FRONT mark and a timing
punch mark on a tooth immediately below that FRONT mark.
https://postimg.org/image/v5uximjh1/" rel="nofollow">
If I’m right about the position of the engine, I expected to find a timing mark on the
accessory drive gear. I couldn’t find
anything though.
https://postimg.org/image/ipy7pf0l1/" rel="nofollow">
https://postimg.org/image/qwq7gg0s5/" rel="nofollow">
https://postimg.org/image/cc94m50tx/" rel="nofollow">
https://postimg.org/image/d31urcq6d/" rel="nofollow">
https://postimg.org/image/te1yo6aj9/" rel="nofollow">
https://postimg.org/image/6pcro7nw5/" rel="nofollow">
https://postimg.org/image/ly2p2e29h/" rel="nofollow">
I see that the pump drive gear has slotted bolt holes. I assume I need to find the timing mark on
the accessory drive gear and set the gear in, then align the pump drive flange
score to the pump timing pointer, then tighten down the drive gear on to the
pump drive flange. That will ensure the
quill shaft hat window will allow the hydraulic head to drop on. At the same time, the hydraulic head rotator
gear will be timed because the marked tooth will be aligned with the timing
pointer in the timing window of the pump itself.
Those in the know, please confirm the above pump
installation procedures. If I’m right
about the procedure, maybe I don’t need to worry too much about timing marks
between the accessory drive gear and the pump drive gear. As long as the engine really has No. 1 at top
dead center on the compression stroke and I have enough room in the pump drive
gear slots to align the pump drive flange score mark with the pump timing
pointer, everything should be O. K.
Now for some questions about the rotating gear, the tin
cover for it and the drive from the rotating gear to the plunger itself.
I can see that the tin cover is assembled by slipping it
over the rotating gear and hydraulic head flange, then it is crimped in four
places and staked at one place (which should keep it from rotating).
Since my tin cover got chewed up, I didn’t see any loss by
prying it off.
https://postimg.org/image/z289eszdh/" rel="nofollow">
https://postimg.org/image/ei3fgbrc5/" rel="nofollow">
https://postimg.org/image/ir85ihf5x/" rel="nofollow">
If I had to, I think I could straight this cover out and
salvage it, but I think I’m better off to carefully remove the tin cover from
Daron’s donor pump. It appears to be in
perfect shape and I don’t see any differences in this area between the two
pumps.
If I can remove the tin cover from the donor pump, should I
be O. K. to just recrimp in the same four places with a screwdriver, then stake
it with a punch in the same place as is provided on both hydraulic heads?
Once I had the tin cover off, I could see what I think are
other problems. The rotating gear
operates on what I think is supposed to be a one piece collar which has two
ears engaged in recesses in the rotating gear and has a square opening through
which the square part of the plunger shaft passes.
On my pump, this collar is in two pieces. It must have split when the plunger was
seized and the engine was first rotated.
It is possible that it is supposed to be in two pieces, I haven’t taken
apart the donor hydraulic head yet.
I don’t think it is supposed to be in two pieces because the
two pieces aren’t symmetrical and the plunger shaft is able to move rather a
lot in relation to the rotating gear.
Here are some pictures of the assembly as it is now, including a couple
which show the plunger shaft rotated within the collar one way, then the other.
https://postimg.org/image/w8541chrp/" rel="nofollow">
https://postimg.org/image/xafajvsv9/" rel="nofollow">
https://postimg.org/image/tqtcucddh/" rel="nofollow">
https://postimg.org/image/4ksengu2t/" rel="nofollow">
The plunger does rotate with the gear, but I’d estimate
there is probably fifteen or twenty degrees of play with the system the way it
currently is. I can’t imagine this is
acceptable. Without disassembling the
donor hydraulic head, I can see that all the rotating gear and drive stuff is
in good shape and doesn’t appear to have the slack that this system has. Is it likely I can swap the drive collar from
the donor pump onto this one?
I know I can’t swap plungers, as they’re matched. I would expect this drive collar and the
square part of the plunger to be standardized though, so I hope exchanging the
drive collar shouldn’t be a problem.
That leads me to what I hope is my last question: If the drive collar can be exchanged, I have
four possibilities to assemble the rotating gear onto the plunger shaft. How do I time the shaft to the drive
collar? Is it as simple as aligning the
spill slot in the plunger with the timing tooth on the rotating gear? Maybe there is a timing mark on the plunger
shaft end that I haven’t noticed?
Thanks for any help the group can give me.
I think if I can accumulate all the knowledge and hopefully
find one good governor control shaft with a good tang on it from Daron, I might
be able to reassemble this thing and hear it run next weekend.
Pete.
|
Posted By: Ian Beale
Date Posted: 21 Jan 2018 at 11:23pm
Pete
Try that set of pages for the AC 45. If yours is similar -
1. You ought to have a timing mark on the top LHS of the flywheel housing under a squarish plate. When you have No 1 (Fan end cylinder) about TDC you need the FPI mark lined up with that pointer.
2. You need the marked tooth on the head lined up 1 tooth to the rear of that timing pointer. If you have it lined up directly it seems the plunger is hydraulic locking until the distributor lines up with the injection pipe port - which doesn't sound good for the internals
3. Then there is another timing pointer under a plate on top of the timing housing (the oil filler on an AC 45). Which has to line up with the centre mark on the boss that holds the timing gear. And the plunger spring wants to turn the shaft away from lining up with that mark. You set that on the grader (blower engine) with a shaft that sticks out the front of the timing case which has a square end for a spanner and then tighten the 3 bolts as you turn the engine to get at them. I'm not sure how you'll do that as I don't have a manual that covers 10000-on engines. Would be in a comprehensive HD 11 engine manual if you can find one of them.
I've never been in the skew gear section so no help there.
When you do that spill valve shaft and the tang area make sure there are no tiny burrs on anything. We had problems with throttle response from one which used to catch with the primary fuel pressure on it. It took our very patient diesel mech son most of a day to find it.
How we got into this in the beginning? We scored an unused short block with a supposedly reconditioned pump. Which leaked fuel into the oil. Because it was missing the bottom O-ring for the head.
Hope yours works
|
Posted By: DMiller
Date Posted: 22 Jan 2018 at 6:04am
When you load photos you have to use the photo load in the menu line above the writing block. Looks like a tree with an arrow on it. The site does not allow drag and drop nor does it seem to like odd hyper links. Will have to go back in and edit or delete as there is not much room in the site storage. Just my $.02.
|
Posted By: Garlic Pete
Date Posted: 29 Jan 2018 at 10:24am
Mom and I made a trip up to Daron’s in California City
Saturday. Along the way, we delivered
Chad’s tail seat Twenty Two, which he had bought at the Doug Peltzer auction
and picked up a nifty little Allis Chalmers WC grader that Daron had bought.
Here’s a little video of the loading process. We had plenty of help.
https://youtu.be/N86qi0zmyZ4
Daron’s last spare engine had the intact sleeve control
shaft that I needed. It was a bit
crusty, but still intact and looked like it would clean up nicely.
https://postimg.org/image/8ql9w9ol1/" rel="nofollow">
https://postimg.org/image/4hgju3t1h/" rel="nofollow">
https://postimg.org/image/a5mukza8l/" rel="nofollow">
https://postimg.org/image/ib4wj5679/" rel="nofollow">
First, I soaked in some P. B. Blaster for a while. After that, I very gently tried to work the
tang back and forth by hand. I couldn’t
get it to move, so I tried some small pliers, just very gently and carefully.
At first, I still couldn’t see or feel any movement, but
after a bunch of very gentle back and forth cycles, I thought I could see just
a tiny amount of movement. I just kept
patiently working it back and forth, back and forth and eventually it got a bit
easier each time. Once it was moveable
by finger pressure, I knew I had it made.
Once I was confident that the tang would free up enough to
float freely, I started soaking and spraying the sleeve and shaft. They moved, but were very, very stiff.
I soaked and worked them many cycles, but it was apparent
that they weren’t going to come free enough to allow the governor to work.
I decided I’d better remove the nut and control arm from the
splines and try to work the shaft out of the sleeve. The nut and control arm came off the shaft
reasonably easily.
With them out of the way, I was able to carefully use two
vice grips to rotate the shaft within the sleeve while pulling them apart.
That shaft fought me all the way until the last micron. It took a long time and a lot of working,
rotating and pulling, but they finally came apart.
https://postimg.org/image/zbnsru6dx/" rel="nofollow">
Of course the shaft and bore looked clean and shiny and as
soon as they parted, they slid back together and worked effortlessly. These are apparently a close enough fit that
just a few molecules of rust are enough to create a bind.
Once everything was clean and moving freely, I reassembled
the shaft, sleeve, arm, nut and lock.
Now, to remove the broken pump drive collar from the good
hydraulic head and swap it with the good one from Daron’s donor pump.
The donor pump plunger was frozen in its bore, apparently
partially compressed. Mom helped me and
we tried to compress the spring and remove the valve keepers from the head, but
there wasn’t quite enough room to get them fished out.
I didn’t want to damage the drive collar, as I knew the
other one was broken. I tried wedging
chisels in the spring coils to push the plunger out, but it wouldn’t
budge. Knowing this plunger and
hydraulic head were no good, I finally just snapped the end off the plunger to
get the spring and keepers out of the way.
https://postimg.org/image/3rxrhpxmt/" rel="nofollow">
Here are some photos of the drive collar installed on the
good hydraulic head. The collar has
three flats and one curved side to match the pump plunger, meaning as long as
it is installed with the right side up, the plunger will be timed to the drive
gear properly.
https://postimg.org/image/f4aczjgmd/" rel="nofollow">
https://postimg.org/image/f4aczkbhh/" rel="nofollow">
https://postimg.org/image/56zc6iblh/" rel="nofollow">
It was easy work reinstalling the spring and retainers.
https://postimg.org/image/l581wnsyt/" rel="nofollow">
I timed the hydraulic head to the drive sleeve timing mark, following
the instructions so that when the sleeve hash mark aligned with the pointer the
timing tooth on the hydraulic head gear was one tooth to the right of the
timing mark on the pump body.
Here is the completed pump, ready for installation on the
tractor.
https://postimg.org/image/inwape1cl/" rel="nofollow">
https://postimg.org/image/699ip224l/" rel="nofollow">
The rest of the installation was pretty quick and easy. Just hang the pump then tighten down the
three flange nuts. I already had the
engine set with the No. 1 cylinder at top dead center on the compression
stroke.
After that, slip the timing gear in, then use the pump shaft
nut to rotate the pump until the hydraulic head drive gear had the marked tooth
one tooth to the right of the timing mark.
Hold it there and tighten down the three timing gear to pump drive
flange retaining nuts, which locks the gear in relation to the pump drive
flange.
Hook up all the fuel lines and it was ready to go. I cranked the engine with the injector lines
off until it primed up and pumped some fuel out of the injector supply
ports. Hopefully any dirt or grit in
there would get pumped overboard. It
didn’t take long to have nice flow from all six ports.
I reconnected the injection lines and gave it a spin. Here’s a video with me tightening the lines,
then the first start and a bit of a run.
https://youtu.be/k6xtloV71N0
I still have several problems. The suction line from the fuel tank has leaks
and restrictions, so it is sucking air.
I believe the return line must have obstructions too, because I could
see air bubbles coming from several bad places and loose connections on a few
of the return lines to the filter manifold.
The governor also seemed to want to maintain the engine at a
high idle. I concluded that I likely
didn’t index the arm correctly on the sleeve control shaft. I think if it was a tooth off on the spline,
the governor would want to maintain the wrong speeds. I could control the engine speed by manually
manipulating the sleeve control shaft (I had the shut off cover removed), but
with the fuel supply problems, I couldn’t really run it long enough and
consistently enough to diagnose.
I’m going to run new lines from the tank (which is up in
front of the operator’s station) back to the pump, eliminating any restrictions
and leaks, next work session. (Hopefully
next weekend).
I have taken a big step in resurrecting this tractor, mostly
because of the help I received here.
Thank you all and I’ll keep you posted as things progress.
Pete.
|
Posted By: Garlic Pete
Date Posted: 29 Jan 2018 at 10:26am
Here are live links to the videos: Loading the WC grader. https://youtu.be/N86qi0zmyZ4" rel="nofollow - First run of the wheel dozer. https://youtu.be/k6xtloV71N0" rel="nofollow - Pete.
|
Posted By: Garlic Pete
Date Posted: 05 Feb 2018 at 10:37am
More Progress, More
Questions.
I made more progress this weekend, but have more questions.
The first order of business was the last remaining issue
with the PSB pump. The governor seemed to
work like on a generator set, not a tractor.
It maintained high idle, no matter where the throttle lever was
positioned.
I knew it was working because if the throttle lever was put
in the idle position, the governor would just slightly reduce engine speed, but
as soon as the throttle lever was moved off the stop, the governor would
increase engine speed again, but not overspeed the engine.
I decided to take apart the governor on Daron’s spare pump
first, to learn how the mechanism works and hopefully learn something that
would help diagnose the one on the tractor.
Here’s another situation where having Daron as a friend with lots of
spare stuff really pays off!
As with most stuff on this American Bosch stuff, the system
is easy to disassemble and pretty simple from an engineering sense, too. Makes reverse engineering in the field pretty
nice!
The governor separates from the pump by unscrewing five
bolts, then just pulling the governor housing from the pump housing.
Here’s a view of the pump housing with flyweights.
https://postimg.org/image/xufppi90l/" rel="nofollow">
Here’s a view of the top of the governor housing showing the
sleeve meter control rod attachment point and idle and power setting
adjustments.
https://postimg.org/image/v0ckc2m9x/" rel="nofollow">
And here’s the governor housing, with the collar upon which
the flyweights act.
https://postimg.org/image/s69eylwyd/" rel="nofollow">
You can see the collar and hollow shaft with the governor
springs behind. There are a couple
nested springs which are inserted into the governor housing under a round
cover. The springs press on the shaft
attached to the collar.
You can also see the frame which the hollow shaft engages. The frame has a pivot on the bottom and the
attachment for the sleeve meter control shaft at the top. Inside the housing on the right of the
picture you can also see a copper colored spring which surrounds the throttle
control shaft.
The throttle shaft engages a pivot on the bottom of the
frame. In a balanced state, centrifugal
force of the rotating governor shaft pushes the flyweights out, the flyweights
push on the collar in this picture, compressing the governor springs at the
back of the shaft. As the collar moves
back and forth, it move the frame, the frame pulls the sleeve meter control
shaft, which injects more or less fuel.
Engine speed is maintained at the point that the centrifugal
force of the flyweights exactly balances the strength of the springs at the
back of the shaft. If the engine
experiences more load, the rotational speed will slow, centrifugal force on the
flyweights will decrease but the springs will maintain constant pressure,
meaning the frame will get pushed away from the back of the governor
housing. This action will move the
sleeve metering control rod, meaning more fuel will be injected, meaning more
power will be created, engine speed will increase, increasing centrifugal force
on the flyweights and the system will come back into balance, once again at the
same set engine speed.
If a load is removed from the engine, speed increases, the
flyweights push out, the frame moves into the housing, sleeve meter reduces
fuel injected, power goes down, engine speed goes down and the system once
again seeks balance at the same set engine speed.
The throttle on this governor is interesting in that it
operates by moving the pivot point of the bottom of the frame. Since the flyweight pressure and spring
pressure will always seek to balance each other and opening the throttle moves
the pivot point at the bottom of the frame, the top of the frame will be
pivoted in the opposite direction of the pivot point movement.
Opening the throttle moves the bottom pivot point slightly
towards the rear of the governor housing, meaning in a balanced state, the top
of the frame will move slightly away from the governor housing. This movement causes the sleeve meter control
rod to move away from the governor housing, meaning more fuel is injected,
meaning that more power and more engine speed will be selected for a given
balance state of the governor system.
From all this deduction process and knowing that the pump on
this tractor had sat for years exposed to the elements, I thought that perhaps
the problem with the governor on the tractor was that one flyweight was stiff
or frozen on its pivot. That would only
apply half the centrifugal force to the collar against the governor springs and
theoretically, should result in the governor trying to maintain way to high an engine
speed. The only way to know is to remove
the governor on the tractor and take a look.
Here’s a photo of the flyweights on the tractor.
https://postimg.org/image/3pr949e91/" rel="nofollow">
And here’s a short video.
https://youtu.be/AnZI6iIJxXI" rel="nofollow -
Obviously they are nice and free, so the governor weights
aren’t the problem. I spent some time
looking at and comparing the two governors.
They were nearly identical and for a while I couldn’t figure out why the
tractor one didn’t work.
After a bit of comparing and experimenting, I figured out
that the tractor throttle linkage wasn’t working right. When the throttle shaft on Daron’s was moved,
it moved the bottom of the frame visibly back and forth and I could feel a
difference in the spring pressure on the sleeve meter control rod at the top of
the frame.
When I moved the throttle shaft on the tractor governor, the
frame barely moved at all and I really couldn’t detect a difference in sleeve
meter control rod pressure.
Here’s a short video showing the two moving. The tractor one is a little hard to see
because of the dark oil in there, but I think you can make it out.
https://youtu.be/ks0wOorcaVY" rel="nofollow -
I think I found the problem.
I thought about disassembling the tractor governor housing and swapping
parts or repairing, but decided to save that project for another day.
Comparing the markings on the two pumps, it looks like the
tractor is set for an idle speed of 600 RPM and high idle of 2,200 RPM. Daron’s governor is set for an idle speed of
650 RPM and high idle of 2,600 RPM. The
idle speed difference is probably O. K.
The high idle difference is more significant and would result in
significantly more horsepower than this system is designed for. While I have this governor on here, I’ll have
to be careful about engine top speeds.
Here are photos of the two number plates.
https://postimg.org/image/h6o7n5r5h/" rel="nofollow">
https://postimg.org/image/vd3yie9qd/" rel="nofollow">
https://postimg.org/image/f23um2a39/" rel="nofollow">
Eventually I’ll either repair the tractor governor or figure
out how to adjust Daron’s to bring the high idle RPM back down to 2,200. For now, I’ll just be careful.
Here is a photo of Daron’s governor installed on the
tractor.
https://postimg.org/image/4s1fmvpdh/" rel="nofollow">
And here’s a little video of the engine running with the new
governor. I didn’t check this video
until this morning, so the audio isn’t great because of the radiator fan wind
noise, but you can see and sort of hear what is going on. I’m really happy with the overall control of
the engine now. I think I’ve completed
the injection pump part of the fuel system work.
https://youtu.be/jmBVGGDxazE" rel="nofollow -
Now that I’ve got the injection pump basically working, I
started work on diagnosing a miss. One
cylinder is clearly not firing, but I don’t really have any puffs of smoke, so
I suspect that my dirty field work on the injection pump has probably let a
piece of grit or something into one of the injectors.
Here’s a video from the top of the engine with it running a
bit above low idle. I cut out several
injectors in turn by cracking the lines at each. Cylinder number two appears to be the one
which caused no change in the engine when the line was cracked.
https://youtu.be/KapJ6AgSNVk" rel="nofollow -
I feel I’m getting good clean flow and a good amount (at
least similar to the other injectors) at cylinder number 2. I assume that means this injector is bad and
needs to be swapped, rebuilt or repaired.
Here is a photo of the injector in question.
https://postimg.org/image/k0rd0nqrp/" rel="nofollow">
Can someone help out with information about those
injectors? I assume the removal process
is:
1.
Clean the top of the head.
2.
Remove the supply line and return line.
3.
Unscrew the two hold down nuts.
4.
Pry the injector out of the bore.
Are there any tips or tricks? Does anyone know about these injectors, can they
be field cleaned or repaired, or do they just have to be replaced? I’ve worked on International injectors from
the late 1940’s. Those can be completely
disassembled and cleaned with simple hand tools. I don’t imagine these will be that easy.
Does anyone know where I could get a new or rebuilt
injector? How would I go about finding
the specifications or part numbers on this one to begin the search?
While I was up here and had the engine running for some
time, I noticed another missing piece.
Note the gap between the turbocharger impeller housing and the exhaust
elbow. It looks like there is probably a
collector ring missing.
https://postimg.org/image/4s1fmumsl/" rel="nofollow">
https://postimg.org/image/9qoy1edqt/" rel="nofollow">
https://postimg.org/image/o9w32sz5x/" rel="nofollow">
I see several about 3/8” bolt holes in the impeller
housing. The way the exhaust elbow is
supported on the manifold casting, it can’t be that it has shifted outward,
there needs to be a small piece to fill the gap there. I think I can run it as is if I have to,
although I might not put the hood on to capture all that hot exhaust around the
engine.
I did see a tag on the turbocharger, but I don’t know that
these numbers will be of any help.
https://postimg.org/image/qegg3wg85/" rel="nofollow">
Does anyone have any ideas about how to figure out what
piece is missing and locate a replacement?
Since I’ve got the engine basically functioning, albeit on
only five cylinders for the moment, it was time to turn my attention to other
systems. The hydraulic pump had been removed,
but did come with the tractor. It is
mounted to the side of the engine and belt driven by two V-belts off the crank
pulley. Without the pump installed, I
can’t fill the hydraulic tank. It
appears that the transmission shares the hydraulic fluid with the rest of the tractor,
so I can’t test the transmission without reinstalling the pump.
I also can’t test anything because all of the controls in
the operator’s station are frozen solid.
I decided to attack freeing up the controls first. With the open station, you’d think that would
be easy, but this thing is constructed of a half inch steel tub with a little
square cockpit with the steering wheel and dash in front, a control stand on
each side of a fairly narrow seat and the hydraulic tank and other apparatus
behind the driver’s back. When sitting
in the seat, the sides of the frame are about halfway between the driver’s
elbows and shoulders.
There isn’t much room and all the linkages and controls are
down in the bottom. The floor plates had
already been removed (but also came with the tractor). The only way any work could be accomplished
was by standing on my head.
The controls consist of a parking brake and transmission
control on the driver’s left and two hydraulic control levers, a transmission
range selector and a diverter plunger on the driver’s right and air brake
pedals on the floor. Nothing moved.
To top that off, the first part of the project was
replacement of the rotten fuel lines, which attached to the front fuel tank way
down in the bottom front of the cockpit, about a foot below the floor plates.
Garlic Mom was a bit concerned when she came out to check on
me and saw this.
https://postimg.org/image/d5bpv9bdx/" rel="nofollow">
https://postimg.org/image/goxnl26dx/" rel="nofollow">
https://postimg.org/image/4aavkowv9/" rel="nofollow">
https://postimg.org/image/bqa56i005/" rel="nofollow">
It took a lot of grunting and some choice words and probably
ten minutes, but I was able to wiggle myself into and out of that cockpit.
Here are some photos of the various controls. I have removed the seat, control covers and
anything else I could to facilitate access.
This is the parking brake and transmission control. The transmission control provides forward or
reverse in three speeds. The control
cover has a gated path through which neutral lock is centered and away from the
driver, the first set of forward/reverse slots is low, middle set is
intermediate and closest set to the driver is high.
You can see from the below photo that the linkage works by a
forward reverse control rod operating a crossover shaft with a push-pull rod
back to a transmission valve. The side
to side control rod operates off the side of the lever to a sleeve on the crossover
shaft with another push-pull rod back to another valve on the transmission.
https://postimg.org/image/muuidw35x/" rel="nofollow">
Here are the right side controls, two hydraulic control
levers, transmission range selector and plunger to diver one control from tilt
to blade face angle.
https://postimg.org/image/q1p1xifw5/" rel="nofollow">
Here are the brake pedals.
You can see the fuel tank connections down below the pedals.
https://postimg.org/image/o9w32r9fp/" rel="nofollow">
Garlic Mom’s pictures were taken as I was deep in the bottom
changing those two hoses.
After I got the fuel lines fixed up, most of the other
controls freed up surprisingly easily.
Each one only took some shots of P. B. Blaster and some vigorous jerking
back and forth of the control to eventually begin moving.
I did have to stand on my head with the rosebud to heat that
power brake pedal shaft. It took several
cycles, but eventually even that freed up.
It is pretty exciting using the rosebud down there around all the accumulated
dirt soaked with fuel and hydraulic fluid while standing on your head and
having to wiggle in and out over a ten minute period. I used lots of water bottles putting out
small fires.
The other exception to the freeing process was the two
hydraulic controls. They each worked a
push-pull rod which went up behind the driver’s head to a bell crank which
worked valves on top of the hydraulic tank.
The levers themselves freed up nicely, but the bell cranks
didn’t want to pivot. Here’s a phot of
the control valves. The bell cranks and
their mounting pad have already been removed to the left side of the picture.
https://postimg.org/image/cxjhkzg6d/" rel="nofollow">
Those bell cranks had sat under the louvered cover and
accumulated rain and mist for years and they didn’t want to move.
I heated them with the rosebud and eventually they
yielded. I was surprised that each had a
needle bearing and set of seals. I was
also surprised that there was no grease zerk to service the bearings. I guess they were supposed to be sealed for
life. I’ll have to go to Applied
Industrial Technology this week to match the bearings and seals.
https://postimg.org/image/x4wxdbg8l/" rel="nofollow">
https://postimg.org/image/epcgfyrud/" rel="nofollow">
https://postimg.org/image/gh5favix1/" rel="nofollow">
Next work session I’ll reinstall the bell cranks with new
bearings and seals and all controls should be operable.
I’ll need to figure out the hydraulic pump connections. The pump has two supply connections and two
output connections. The outputs split at
a sort of relief valve. This wheel dozer
uses the hydraulic pump to lift and tilt the blade and also has hydraulic
steering. I assume that the relief valve
split on the outputs is probably really a priority valve to supply the steering
over the blade controls.
I can only see one system pressure connection and one supply
from the tank on the loader, though. I
can see the steering system connections at the wheel and trace them down to
where they disappear inside a frame rail.
I don’t see the other end terminating near the pump, though. Next work session I’ll have to trace those or
try blowing air from the steering wheel end to find the ends of those steering
lines.
Once I can connect the pump and fill the hydraulic tank, I
can see if this thing will move and maybe even lift the blade.
Progress, but in small steps and with many questions.
Pete.
|
Posted By: Garlic Pete
Date Posted: 13 Feb 2018 at 9:05am
Not much progress this weekend. I was able to find a diagram of the injector. https://postimg.org/image/3uininj39/" rel="nofollow"> These look pretty simple and probably field reparable. With the bit of time I had, I decided to try pulling the dead injector. Here's the top of the head after blowing off all the dirt and junk. https://postimg.org/image/xrjh7d0b9/" rel="nofollow"> I pulled the line from the injector pump and the common return line. The hold down nut in the top of the above picture came off easy. The one on the bottom, not so much. That hold down stud had rotted more than half through with rust, so it just twisted off without even putting much pressure on it. Oh well - I'm committed now. I know my buddy Martin is a good welder and if I get the injector out of the way, I'll bet he can weld on a washer and nut and we can get that stud extracted. With the hold down nuts (and one stud) out of the way, I tried to pry that injector out of there. No dice. I had a nice pry bar with one of those short wedge heads that got good purchase under the shoulder of the body where it sticks out and the supply line attaches. I was afraid to pry much on the hold down ears for fear of breaking them off. That injector didn't think about budging. I decided to try removing the cap nut, jam nut, adjusting screw, spring and spindle rod from the top. If I was lucky, maybe I could run some fuel through from the injection pump under pressure with the spindle rod out and dislodge any debris. I realize that the adjusting screw and spindle rod must regulate the supply pressure to the actual valve at the tip, so I counted the turns as I unscrewed the adjusting screw so I could put it back on with the same tension on the spring and spindle rod. Here are the cap nut, jamb nut and seals. https://postimg.org/image/r2cxr6exh/" rel="nofollow"> And here's the adjusting screw, spring and spindle rod. https://postimg.org/image/9cb964lx1/" rel="nofollow"> And here's the body, still in the head but with those parts removed. https://postimg.org/image/6uzhyvp5x/" rel="nofollow"> I reconnected the injector line and ran the engine some. I didn't get any fuel shooting out of the hole in the injector body. Some fuel must have been making it through because some fuel did appear slowly rising from the hold into the cavity where the adjusting screw and spring would be, but it should have really flowed out of there. I disconnected the injection pump line again and blew out the supply port. I didn't see any area which could be further disassembled, no filter or other provision to service that port. I did run some bailing wire down through the hole and was able to fish it down probably two or three inches into the injector body without any resistance or obstruction. I'm pretty sure I'm going to have to get that injector body out of the head and unscrew the nut on the bottom, remove the actual nozzle and valve and clean or free them up. I think that is where the obstruction or frozen parts are. For now, I reassembled everything as it was and will live with the miss. I installed the new bearings and seals in the hydraulic control bell cranks, re-oiled all the control linkages that I had freed up and that was about all I had time for this weekend. Mom and I were a little busy, having to take a load of hand stacked parts and pieces over to Paso Robles Saturday and then Sunday we were asked to bring something small and interesting to Tulare for display at the big International Ag Expo, which is Tuesday, Wednesday and Thursday this week. They give us a booth or two to show the old stuff and promote the big April antique show which is held on those grounds. We decided to take the HD-15AC and a sheepsfoot and Mom High Ten and potato planter. Here's a couple of photos all loaded up and ready to go Sunday morning. https://postimg.org/image/htarh1qlx/" rel="nofollow"> https://postimg.org/image/r12zxr5dx/" rel="nofollow"> https://postimg.org/image/5rfdmxzdx/" rel="nofollow"> Mom drove the truck and I drove the pickup. Here are some shots along the way. https://postimg.org/image/bflodtoat/" rel="nofollow"> https://postimg.org/image/3mv0lvd6t/" rel="nofollow"> https://postimg.org/image/6gy5zacs5/" rel="nofollow"> https://postimg.org/image/qoblrm54l/" rel="nofollow"> https://postimg.org/image/yh29joy9x/" rel="nofollow"> https://postimg.org/image/9b1bcvrut/" rel="nofollow"> https://postimg.org/image/dwxflcfzp/" rel="nofollow"> https://postimg.org/image/bsd2k9m2t/" rel="nofollow"> https://postimg.org/image/76gybxvet/" rel="nofollow"> https://postimg.org/image/jxv4ifxh1/" rel="nofollow"> https://postimg.org/image/6i83soc11/" rel="nofollow"> Next week I should be ready to tackle remounting the hydraulic pump, figure out the plumbing and see if it'll lift the blade and move under its own power. The hydraulic pump is a bit of a conundrum. It clearly has a non-factory mounting bracket. The pump itself may be original or may not. It clearly has been mounted on the tractor before, the sheaves line up with the crank pulley, the non-factory mount and crossmember it mounts to show marks that it was mounted, the belts are there and match. The pump has non-factory galvanized plumbing, including a Y on the supply giving two input connections and a Y and pressure diverter on the pressure line, giving two output connections. One of the supply connections aligns with the non-factory galvanized connection to the hydraulic tank. One of the pressure line output connections from the pump aligns with the factory main system pressure line connections. I can't find a second return or pressure connection anywhere else on the tractor. This tractor has the hydraulic steering similar to an International 806 tractor, where the steering wheel is just connected to a hydraulic motor which is plumbed to the steering rams. No physical connection between the steering wheel and the axle. It makes sense to me that the steering system might be supplied by the main hydraulic pump, but with a separate system to override hydraulic pressure to the steering over the rest of the tractor systems. Most of these steering systems I've seen have their own little pump and reservoir, but clearly that isn't the case on this tractor. I suspect I'm going to find that the second set of pump connections really are for the steering, but I sure can't see where the plumbing is on the tractor to connect it. When I remount the pump, I'm going to plug the two extra connections for now. That'll let me begin to fill the hydraulic tank. If anything leaks out, it'll lead me to where the extra supply connection might be. If nothing leaks, I'll try running it with only one supply and one pressure connection. If everything else works and I have no steering, I'll have to begin tracing those steering lines and figure out that system. Hopefully I'll get through that next weekend. If anyone is going to be at the Tulare Farm Show this week, swing by booth G-52, back near Gate 17 and near the Southeast corner of the grounds. Garlic Mom will be there all three days, along with the HD-15AC and High Ten. She'd love you to say "Hi!" Come to the Tulare Antique Farm Show April 20th through 23rd and the HD-15AC, the wheel dozer (assuming I get it running) and lots of other stuff will be there. You can see them and run them, if you like. They'll also be at the Santa Margarita show Memorial Day weekend, May 25th through 27th. That show is one not to miss. There is more iron there of every type than you can imagine. Pete.
|
Posted By: jerbob
Date Posted: 13 Feb 2018 at 11:02am
Thank you for the great pics. What a road warrior!
|
Posted By: Garlic Pete
Date Posted: 18 Feb 2018 at 9:35pm
I got the time to experiment with the hydraulic pump. It had obviously been previously installed, but also was obviously not the factory item. It was sitting loose on the back of the frame when the tractor was bought. The plumbing attached to it has a relief valve on the pressure side and a Y on the supply side, giving two supply connections and two pressure connections. The tractor only appears to have one supply and one pressure connection. For now, I just put plugs in the extra connections on the pump. Even though it appeared that the pump had been removed as found, I could find no way to fish it into the place where it needed to be, so I removed the sheave and bracket, then reinstalled in the tractor. Here are some photos. https://postimg.org/image/nskbk35id/" rel="nofollow"> https://postimg.org/image/fn29lxoz9/" rel="nofollow"> https://postimg.org/image/5e9sfj0r9/" rel="nofollow"> https://postimg.org/image/63skrwgqd/" rel="nofollow"> https://postimg.org/image/pln87uldx/" rel="nofollow"> https://postimg.org/image/7vljmssdh/" rel="nofollow"> https://postimg.org/image/rdg72q9vp/" rel="nofollow"> https://postimg.org/image/segfsfjbp/" rel="nofollow"> https://postimg.org/image/turya1r85/" rel="nofollow"> https://postimg.org/image/4bzlx0kit/" rel="nofollow"> https://postimg.org/image/5e9sfkirp/" rel="nofollow"> With that pump hooked up and plumbed in, I filled the reservoir. No leaks, so I'm almost ready for a test drive. First, I removed the foot valve for the air brakes. It was frozen up and I'll probably have to get a new one, this piston looks grown together with the aluminum housing. Oh well, I have the big brake out front, so time to give all the systems a test. Here's a short video. https://www.youtube.com/watch?v=_Urn7Sn5Yu4&feature=youtu.be" rel="nofollow - https://www.youtube.com/watch?v=_Urn7Sn5Yu4&feature=youtu.be Overall, it looks like everything works as it should. I still need to get the one fuel injector pulled and cleaned to eliminate the miss, the divider plunger to change from blade slope to blade tilt is still frozen and I need to fix that brake air valve. Then, of course, the entire electrical system. At least I'm at the point that I can play a bit. Pete.
|
Posted By: JohnCO
Date Posted: 19 Feb 2018 at 12:33am
I wonder how a machine like that would work for packing silage?
------------- "If at first you don't succeed, get a bigger hammer" Allis Express participant
|
Posted By: Garlic Pete
Date Posted: 26 Feb 2018 at 5:05pm
This weekend I got some more work done. Still haven't been able to get the bad injector pulled. I'm afraid to put too much "pry" on those hold down ears for fear of breaking one. I did run it around for an hour or two with the hold down nuts loose. I'm hoping that the heat and cool cycles and combustion pressure cycles might help loosen that injector if I just leave it uncontained for a while. If it doesn't work loose soon, I'm considering using a jaw type bearing puller with a spanner bar to maybe put more gentle lifting pressure on those hold down ears. I did get the frozen air brake valve removed from under the floor, disassembled and freed up. Here's a couple pictures of it in situ: https://postimg.org/image/6gjyy4h0l/" rel="nofollow"> https://postimg.org/image/5r16lqtbp/" rel="nofollow"> Removing it was another "Stand on your Head" job. Once it was out, my first thought was to go to Chester Avenue Brake, who have been in town for over 100 years, and see about cheap replacement, rebuild kits or if they could free this valve up. I walked in the door and Phil, the counterman (and one of the sons who now owns the joint) just looked at me, looked at what I had in my hand and began shaking his head. He let me walk up to the counter while, still shaking his head, he asked "Don't you people own ANYTHING that was made after 1954?" He went on to say "Let me tell you how bad this is: See this part here (indicating the body of the valve)? This part is at least a standard Bendix part, it is just one that has been out of production for at least thirty years." We went on to say "See this plate and the plunger which the pedal attaches too? That is no doubt a specific part manufactured by whoever made your machine. That is most likely unobtainable." Then he turned it around a time or two and said "Oh, let me tell you, it's worse than that. This isn't even a Bendix valve body. This is Wagner, which predates Bendix. You'd be lucky if you could find anything related to that anywhere." After giving me all the good news, he did describe what was likely inside, gave me lots of good advice about how to get it apart, freed up and rebuild or repair as necessary. On the way to his shop, I had just thrown the valve in the bed of the pickup. After hearing all this good information, I very carefully wrapped it in a towel and put it on the floor of the back seat. I returned home after buying a new, superstrong, giant flat blade screwdriver in hopes of unscrewing the three flat head machine screws retaining the plate to the valve body. https://postimg.org/image/ecr6e01it/" rel="nofollow"> https://postimg.org/image/lfz1tljt1/" rel="nofollow"> https://postimg.org/image/n7s0oiavp/" rel="nofollow"> Two miraculously came right out. I didn't even have to torque on the screwdriver too much. The third, not so much. I clamped the body in a vice and used all the twist I could muster, but couldn't break it loose. I tried the small crescent wrench on the screwdriver shaft trick. That stripped part of the shoulder on one side of the screw. I used my die grinder and deepened and sharpened the slot a bit. Tried again, to no avail. I cut a new slot crossways, still no dice. Finally, I ended up just grinding down the screw head a bit until I could work the plate off over what was left of the screw, but I got it apart. https://postimg.org/image/42oretw8l/" rel="nofollow"> https://postimg.org/image/f29yqc779/" rel="nofollow"> The inside of the valve looked really great. Springs were nice and clean, O-rings looked nice and fat and flexible. The only real problem was the pedal plunger seized in that unobtainable flat adapter plate. Luckily it was seized in the applied position, meaning I could press the valve from the inside out. Here is the assembly in the press with a couple of large sockets for use as pressing tools. https://postimg.org/image/kdovb1lk5/" rel="nofollow"> https://postimg.org/image/ozkzjdrnp/" rel="nofollow"> I was really worried about breaking that unobtainable plate, so I was very tentative and gentle pumping on that press. I gradually pressed until I had the big spring compressed, then gave it very short strokes, followed by some hammer taps to the side of the plate after each short pump. It still took a fair bit of pressure but after one tap SNAP! and the piston was flush with the plate. No harm done! Phew! https://postimg.org/image/cxplp8q51/" rel="nofollow"> Now that the piston was out, a bit of polish with the wire brush in the die grinder, shoot some blaster and it was soon moving in and out smooth as silk. https://postimg.org/image/svybfgkdx/" rel="nofollow"> https://postimg.org/image/bvff6sf2d/" rel="nofollow"> https://postimg.org/image/ty8hy0qcl/" rel="nofollow"> https://postimg.org/image/vda2mqjpx/" rel="nofollow"> I'm ready to reassemble the valve and reinstall it now. That should put the braking system back to 100%. Now to just fix that pesky injector, then tackle the electrical system! Pete.
|
Posted By: Garlic Pete
Date Posted: 05 Mar 2018 at 10:27am
Saturday was rainy and cold, bought parts instead of working. Sunday was nice. Got the repaired air brake foot valve reinstalled and decide to try removing the stuck injector. It took lots of time, thought and creativity to find a way to pry under the injector hold down ears and get it extracted. I thought a two jaw gear puller was the solution, but there wasn't enough room to get the jaws under the hold down ears. Finally, it came down to using the puller arms and some pipe extensions to very slowly and gradually finally get the injector out of the tube in the head. It fought all the way. Here are some pictures. https://postimg.org/image/6udl9wa2d/" rel="nofollow"> https://postimg.org/image/tj2s9helh/" rel="nofollow"> https://postimg.org/image/9ogqnc4it/" rel="nofollow"> https://postimg.org/image/52kmf0651/" rel="nofollow"> https://postimg.org/image/jn1p99gd1/" rel="nofollow"> https://postimg.org/image/ijhkxv8qt/" rel="nofollow"> With the injector out, I polished up the body that goes down in the bore and cleaned everything on the top end out good. https://postimg.org/image/52kmez3k5/" rel="nofollow"> https://postimg.org/image/bg9pi7t0l/" rel="nofollow"> https://postimg.org/image/wr79ly0p1/" rel="nofollow"> Since I don't have the special knurled wrench to get the bottom nut off, I gave it a bit of a squeeze with a bit set of water pump pliers. I didn't want to risk distorting or stripping it, so I didn't put too much pressure and I couldn't get it to budge. I decided to swing the fuel line out, hook up the injector and run the engine to see what was happening. Here are some photos of the spray pattern and a short video. https://postimg.org/image/8ap3rhn3p/" rel="nofollow"> https://postimg.org/image/d9cm60j6t/" rel="nofollow"> https://postimg.org/image/r30yv2r7p/" rel="nofollow"> https://postimg.org/image/53uk7vpt1/" rel="nofollow"> https://postimg.org/image/rfsd1a4cl/" rel="nofollow"> https://postimg.org/image/jaab348dx/" rel="nofollow"> https://youtu.be/DGrJ-1aaQgs" rel="nofollow - https://youtu.be/DGrJ-1aaQgs That valve sure looks like its working fine to me. Four nice clean jets of very atomized fuel, no drips or dribbles. I also got very strong compression impulses out of the open injector hole, so I don't know why that cylinder isn't firing. I'll have to fix the rotted hold down stud on the injector in order to get it to seal in the cylinder and be able to test run it. Maybe it was stuck or plugged, and just getting it out has caused it to start working again. If that isn't the case, I don't know why that cylinder isn't running. Maybe compression is low there and after the engine gets warmed up it'll eventually cut in, or maybe it just won't ever run on that cylinder. Any thoughts or advice? Pete.
|
Posted By: CAL(KS)
Date Posted: 05 Mar 2018 at 10:58am
get a running compression test on that hole while that injector is out.
------------- Me -C,U,UC,WC,WD45,190XT,TL-12,145T,HD6G,HD16,HD20
Dad- WD, D17D, D19D, RT100A, 7020, 7080,7580, 2-8550's, 2-S77, HD15
|
Posted By: Garlic Pete
Date Posted: 05 Mar 2018 at 11:20am
Good idea, Cal. I was just in Harbor Freight Saturday and noticed a Diesel engine compression test setup. A test should tell me if pressures are low (bad valves, rings, etc.) and let me rule that out or in. I'll see if I can pick up one of those testers, if they fit this hole. I assume I'll need to fix the hold down stud for that, too. Thanks for the suggestion, Pete.
|
Posted By: Garlic Pete
Date Posted: 12 Mar 2018 at 10:02am
We spent Saturday loading the DW-21 at Arlie's house and hauling it home. Other than a detour in the rain because Highway 58 was closed at Tehachapi when we got there, that was a fun day. That left Sunday for a little work on the wheel dozer. I attacked the broken injector hold down stud. The stud that didn't break was also very necked down by rust and had bent a bit in all my prying around. I had also managed to mess up the threads a bit, so the nut went on really hard. I expected it to break off as I was tightening down the injector last weekend. I double lucked out because no only did it not break off, but when I unscrewed it the threads bound enough that the stud screwed out and miraculously didn't break. https://postimg.org/image/rzd5wmfl1/" rel="nofollow"> https://postimg.org/image/4xwkqu5mt/" rel="nofollow"> I got the injector out of the way and cleaned up the area as best I could. https://postimg.org/image/y0automrp/" rel="nofollow"> I used a wire cup brush in a die grinder to polish up the sides of the protruding part of the stud, then covered everything with rags so I could try welding a nut on. https://postimg.org/image/jtv3yg46t/" rel="nofollow"> Even with my welding skills, there was enough of the stud protruding that it wasn't too hard to get the nut on there. https://postimg.org/image/sovy8z8et/" rel="nofollow"> https://postimg.org/image/bblnu32t1/" rel="nofollow"> https://postimg.org/image/l8won5pud/" rel="nofollow"> I was a little tentative and afraid of sticking the stud to the head, so the first couple of tries didn't quite stick. The third time was the charm though. https://postimg.org/image/teeqlblt1/" rel="nofollow"> https://postimg.org/image/t1ncf6t9h/" rel="nofollow"> https://postimg.org/image/cqn8iv1c5/" rel="nofollow"> https://postimg.org/image/lyfgzkg45/" rel="nofollow"> https://postimg.org/image/c14g6ivnp/" rel="nofollow"> A quick trip to Lamont General Store and I installed a couple nice, shiny new studs. https://postimg.org/image/osimd1kv9/" rel="nofollow"> Blew everything out nice and clean and remounted the injector. https://postimg.org/image/6cy5fmz11/" rel="nofollow"> It sealed up nice, no compression leaks. I didn't try any leakdown tests and for now, am a little leery about disturbing any of the other injectors to swap them around. I did run it around loaded pretty good for a while, got the engine right up into the temperature operating range. The miss stayed pretty consistent and I don't think I really saw consistent puffs of blue smoke as I would expect if that injector was working in a dead cylinder. Another tell tale I've noticed is that while running the engine with the return line off the injectors, the other two in this head don't really return any fuel, their ports accumulated just a bit, but didn't really flow any fuel. This injector flowed fuel from the return line port consistently. Now that I have this injector easy to install and remove, I'll try the air pressure tests to look for leaks from this cylinder and consider swapping this injector with another to see if the miss follows. I may also give another shot a disassembly of the bottom end of this injector. The nut on the valve end requires a special splined wrench which I don't have and I'm afraid to clamp on it too much with pliers for fear of distorting it. I guess that work will have to wait until the next available weekend. Pete.
|
Posted By: JC-WI
Date Posted: 09 Jul 2018 at 2:15am
Garlic, did you ever get that miss solved in the DW21?
------------- He who says there is no evil has already deceived himself The truth is the truth, sugar coated or not. Trawler II says, "Remember that."
|
|